Edmund Optics (EO; Barrington, NJ) has added new aspheric polishing equipment to its manufacturing facility in Pennsburg, PA, effectively doubling its precision aspheric manufacturing capacity. The new equipment allows EO to expand its production of both stock and custom aspheres for the medical, defense, and commercial markets.
"Aspheres continue to grow in demand," said Walt Czajkowski, vice-president of global manufacturing for EO. "Aspheres have the potential to replace multiple elements in any given system; effectively designed and implemented aspheres can save thousands of dollars in the volume production of such products as imaging lenses, medical devices, and night-vision goggles."
The asphere production capacity at EO includes design, fabrication, and metrology, and consists of two main areas: precision machined optics, and molded optics.
Precision machining
Machined aspheres produced at EO are fabricated on CNC (computer numerical controlled) fab equipment: a CNC cell can handle about 50 to 200 optical components at a time, according to Joe Tipps, EO's general manager. Machining equipment at EO includes grinding and polishing equipment, and in addition, MRF (magnetorheological finishing) post-polishing systems from QED Technologies (Rochester, NY). The MRF process relies on a polishing fluid with physical properties that can be changed by varying an associated magnetic field, making the polishing process completely predictable and computer-controllable--unlike traditional asphere polishing, which is more of an art. Aspheres produced at EO have a surface roughness of 8 to 10 Å or better, says Tipps.
Also at EO is an array of asphere metrology equipment, including contact profilometers, white-light interferometers, and a SSI (subaperture stitching interferometer) system (the SSI is also produced by QED Technologies).
Molding
Edmund Optics is getting into molded optics in a big way. The company has glass-molding equipment made by Toshiba Machine (Shizuoka, Japan), as well as the tooling to manufacture the molds. The capacity of the molding equipment is in the tens of thousands of optical components a month, says Tipps. Matt Tardiff, lens fabrication manager at EO, says that the Toshiba equipment can fabricate optics ranging from 15 mm to 120 mm in diameter, turning them around quickly and at a low price.
Aided by a grant from the US government, EO is also gearing up to produce molded aspheres for the infrared wavelength range (current production is primarily for visible light). In general, EO is producing molded optics on a multiple-shift basis, and is moving toward round-the-clock production, notes Tipps. "We see high demand for aspheres in the year ahead," he says.
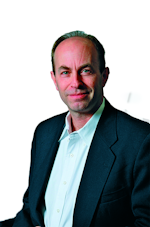
John Wallace | Senior Technical Editor (1998-2022)
John Wallace was with Laser Focus World for nearly 25 years, retiring in late June 2022. He obtained a bachelor's degree in mechanical engineering and physics at Rutgers University and a master's in optical engineering at the University of Rochester. Before becoming an editor, John worked as an engineer at RCA, Exxon, Eastman Kodak, and GCA Corporation.