First James Webb Space Telescope flight mirror completes cryogenic testing
The first mirror segment that will fly on the James Webb Space Telescope, built by Northrop Grumman Corporation (Redondo Beach, CA), has completed its first series of cryogenic temperature tests in the X-ray and Cryogenic Facility at the Marshall Space Flight Center (Huntsville, AL).
The mirror segment is the first of 18 flight mirror segments that will be joined to make a 6.5-meter-diameter (21.3 ft.) hexagonal mirror. The segments will be subject to temperatures of -414 degrees Fahrenheit in a 7,600 cubic-foot helium-cooled vacuum chamber at NASA Marshall.
Engineers will measure how the mirror changes shape going from room temperature to cryogenic temperatures, as its metal expands and contracts. They can model these changes to some extent, but not perfectly. The mirrors will be polished to about 100 nanometers accuracy at room temperature, based on the expected changes. Then it will be cooled down to cryogenic temperatures and engineers will measure the mirror's surface, creating a "hit map" of unexpected changes.
"This is what we have done so far with the first flight mirror segment," said Jonathan Gardner, Webb Telescope deputy project scientist at NASA's Goddard Space Flight Center (Greenbelt, MD). "Now, engineers will warm it up and polish out the 'hit map' areas to get the mirror to 20 nanometer accuracy--a process which will take months. The mirrors will then be brought back down to cryogenic temperatures to verify the increased accuracy." In addition to this testing, engineers also did some "cryo cycling"--or, in other words, bringing the mirror up and down in temperature (without polishing in between) to test the repeatability of the changes.
Since there are 18 mirror segments, each measuring about 1.5 meters (4.9 ft.) in diameter, they will be tested in batches of six and chilled to cryogenic temperatures four times in a six-week time span. It takes approximately five days to cool a mirror segment to cryogenic temperatures. All flight mirror tests are expected to be completed by June 2011. The Webb telescope is scheduled for launch in 2013.
Northrop Grumman is the prime contractor for the Webb telescope, leading a design and development team under contract to the Goddard Center.
"It has taken years of intense effort for the Webb Telescope team to begin flight mirror cryotesting and we're gratified that testing was successful," said Martin Mohan, Webb telescope program manager for Northrop Grumman's Aerospace Systems sector. "Along the way, we've had to invent entire manufacturing and measurement processes because no one has ever built a telescope this large that has to operate at temperatures this extreme."
The James Webb Space Telescope will be the next-generation premier space observatory, exploring deep-space phenomena ranging from distant galaxies to nearby planets and stars. The Webb Telescope will give scientists clues about the formation of the universe and the evolution of our own solar system, from the first light after the Big Bang to the formation of star systems capable of supporting life on planets like Earth.
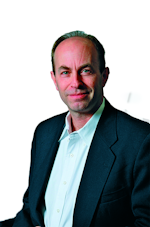
John Wallace | Senior Technical Editor (1998-2022)
John Wallace was with Laser Focus World for nearly 25 years, retiring in late June 2022. He obtained a bachelor's degree in mechanical engineering and physics at Rutgers University and a master's in optical engineering at the University of Rochester. Before becoming an editor, John worked as an engineer at RCA, Exxon, Eastman Kodak, and GCA Corporation.