PHOTONICS APPLIED: NIGHT VISION: Night vision devices offer incredible backyard and battlefield views
Night vision imagers have been available since World War II, when active “Generation 0” devices—a classification defined by the U.S. government to assist manufacturers—that relied on an infrared illuminator were developed. Since then, active infrared has given way to Generation 1 (Gen 1) through Gen 3 passive and thermal night vision systems that with each generation or iteration use advances in detection technology to improve sensitivity and resolution.
While the capabilities of Gen 4 NVDs are typically “classified,” state-of-the-art devices with surprising capabilities—and at surprisingly low cost—are now being used for both military and civilian applications in the backyard and on the battlefield.1
Technology through the generations
Gen 0 and 1 devices can come in the form of a monocular for $100 to $400; technology is typically a passive light amplification device where an objective lens focuses a wide-field image onto a photocathode that in turn converts available light from photons to electrons. The electrons then enter an intensifier tube that amplifies the available electrons, which strike a green phosphor screen to convert the electrons into a visible image (hence the eerie green color). Resolution is typically 40–45 line pairs per millimeter (lp/mm).
For Gen 2 devices (typically $1000–$1500; resolution 28–38 lp/mm), this image intensifier tube is improved by the addition of a fiber-optic microchannel plate (MCP) that significantly increases electron amplification.
Gen 3 devices, even though resolution is comparable to Gen 2 devices, have improved gallium arsenide (GaAs) photocathodes and ion-barrier films that increase intensifier tube life and offer improved sensitivity (jumping in price to $5000–$10,000). Many passive imagers also include a built-in IR illumination that sends a near-infrared beam of light to illuminate the scene.
For thermal or IR imagers that sense the heat generated in a scene rather than amplify photon signals, the “Generation” designations do not apply.
And, yet another NVD option is intensified charge-coupled devices (ICCDs) that operate just like passive light amplification devices using focusing optics, intensifier tube, and phosphor screen; however, the amplified output is sent to a CCD using a fiber-optic coupler. These devices are not only used for night vision but also address scientific and medical research markets.
Civilian search and rescue
Vanderbilt University Medical Center’s (Nashville, TN) LifeFlight air ambulance service is now using night-vision technology once reserved for secret spy missions to help in life-saving rescue operations.2 “It may sound cliché, but the goggles are the ‘difference between night and day,’” says Wilson Matthews, R.N., EMT, and chief flight nurse for LifeFlight’s base in Lebanon, TN. Matthews adds that military night vision equipment is just now becoming available for civilian use after a long time of unavailability due to the numerous wars being waged in the Middle East. Each of LifeFlight’s five helicopters are equipped with three sets of night vision goggles (NVGs)—one for the pilot and one each for the two flight nurses onboard at any time.
LifeFlight aviation site manager for Vanderbilt University Peter Patton says that its night vision goggles are provided by Aviation Specialties Unlimited (Boise, ID), which says it is the “sole authorized dealer” of US Federal Aviation Administration (FAA)-approved night vision systems manufactured by ITT Night Vision (Roanoke, VA). Flying at night presents many hazards to the pilot (telephone or power lines and mountains), especially in rural areas where artificial lighting is sparse, or in rescue situations when it can be nonexistent (see Fig. 1).FIGURE 1. Enhanced vision systems (EVS) are sensitive to long-range infrared wavelengths, improving visibility at night (lower left) compared to a visible-light camera image (upper left). These systems also penetrate fog (lower right) better than a visible-light camera (upper right). (Courtesy of Max-Viz) |
ITT Night Vision’s F4949 AN/AVS-9 Pinnacle binocular imager uses a Gen 3 F9800 Series (MX-10160) image intensifier tube—a high-efficiency 17.5 mm diameter GaAs photocathode bonded to a glass input window, a MCP current amplifier with 6 µm channel spacing, and a phosphor screen deposited on an inverting fiber-optic output window. This NVD has 64 lp/mm resolution and luminous gain values up to 80,000, significantly improving the safety of night-flight operations.
“Mike Atwood at Aviation Specialties Unlimited is the real ‘unsung hero’ associated with bringing military NVG capabilities to civilian aviation and the helicopter EMS [emergency medical services] community,” says Chuck Crompton, VP of dealer programs at Max-Viz (Portland, OR). “He was the first to work with the FAA to help them ‘write the book’ for civilian use guidelines and he is regarded as a real expert and pathfinder in this field.” Crompton says that according to published statistics, helicopter EMS death rates are nine times higher than the riskiest occupations (such as mining and crab fishing), with a disproportionate 49% of all accidents occurring at night even though only 38% of all flights were flown at night.
Crompton explains that even though NVGs using intensified (image tube) night vision (up to 1 µm wavelengths) are currently being deployed in civilian aviation, enhanced vision systems (EVS) or long-range thermal IR imaging systems that detect and display typically 8–14 µm energy are also being deployed in these applications. In fact, Crompton says that many EMS operations are choosing to use both NVG and EVS technology together. Both technologies have their strengths and weaknesses. Night vision goggles require only a small amount of ambient light, but they will not operate in total darkness. Enhanced vision systems can operate in total darkness, but they do require a thermal contrast between a target and its background.
Max-Viz specializes in EVS long-wave IR solutions because longer wavelengths can penetrate larger particle fields, improving visibility through blowing dust and fog. “As droplet sizes become larger than 1 micron, the NVG scene will begin to shut down, just as it does to the naked eye,” says Crompton. “The long-wave IR window will only begin to close down when droplet sizes grow larger than 12–14 microns.” But he cautions, “The laws of physics dictate infrared energy attenuation in thick fog or clouds. We employ some great engineers in this industry, but to date we still have not found any that have been able to change the basic laws of physics.”
Finally, Crompton adds that while the initial capital investment for NVGs is relatively small ($10,000 for an NVG) compared to the $80,000 or so for an EVS system, NVG recurring training, as well as the fact that several binoculars/monoculars are needed for individual viewing compared to just one LCD for an EVS that can be viewed simultaneously by all crew members, make costs comparable for both technologies.
Backyard enthusiasts
Sofradir-EC, formerly Electrophysics (Fairfield, NJ), has been supplying NVDs for 30 years. The company originally supplied devices for near-IR conversion and astronomical observation based on Gen 0 and Gen 1 devices, respectively. Its AstroScope product line includes a number of models that convert digital single-lens reflex (SLR) cameras, video camcorders, and professional news cameras into low-light imaging systems for news journalists, bird watchers, astronomers, and other nighttime enthusiasts (see Fig. 2).
“For some time, it was thought that thermal imaging devices would replace image intensifiers as the night vision technology of choice. The primary reason was because image intensifiers require a minute amount of light for the amplifier to deliver adequate images over noise,” says Frank Vallese, president of Sofradir-EC. “On the other hand, since thermal imagers create images from the IR radiation generated by objects, no light is required.” Sofradir-EC’s AstroScope incorporates a Gen 3 intensifier tube that transforms starlit scenes into bright, high-resolution images equivalent to a ten F-stop improvement in light gathering capability. “For many reasons, it is clear that both technologies are valuable for different aspects of nighttime imaging,” adds Vallese. “In fact, some night vision goggles fuse the thermal and intensified images in order to deliver further capability for the soldier.”
Battlefield ready—day or night
FLIR Systems (Wilsonville, OR) has been making thermal imagers since the 1960s for applications ranging from building inspection and maritime security to border control and battlefield threat identification (see Fig. 3). Its thermal imaging systems take the form of fixed-mount, handheld, weapon sighting, pole-mounted, helmet-mounted, and gyro-stabilized gimbal configurations.
“Most manufacturers buy detectors from one supplier, lenses from another, and image-processing electronics from a third—then try to make them all work together,” says David Strong, VP of marketing in the Government Systems Division at FLIR Systems. “This piecemeal approach has negative impacts on the final performance of the system being built. FLIR builds and designs everything to work together from the ground up, ensuring maximum performance.”
The latest development for the battlefield from ITT Night Vision is its enhanced night vision goggle, or ENVG (AN/PSQ-20), that optically combines image intensification and thermal IR imaging into one goggle. Fusion gives the ground-based soldier greater situational awareness and expanded viewing capability even in total darkness and through battlefield obscurants such as fog or smoke. ITT is currently developing a digital version of its ENVG and says that the main challenge to these fused devices is minimizing the image latency inherent in digital systems. In the current state, using the prototype systems can cause nausea for soldiers due to the lag between the displayed image and real time. The other main challenge is reducing size, weight, and power consumption to a reasonable level for the ground soldier.
Combining forces
As noted in the previous sections, a common trend for night vision applications is to combine visible light, thermal, and ICCD or intensified images. Lockheed Martin Gyrocam Systems (Sarasota, FL) has a gimbal-mounted remote vision system that uses a combined day, thermal, and night vision camera with ICCD technology from Stanford Photonics (Palo Alto, CA) (see Fig. 4). Other weapons imaging systems such as the MK-47 Striker—a 40 mm grenade machine gun from General Dynamics Armament and Technical Products (Charlotte, NC)—also incorporate ICCDs as well as other spectral band imagers. In the past two years alone, Stanford Photonics has built and shipped more than 1000 ICCDs to specialized night vision applications.“Direct-view NVGs are cheap [$5000 for top-of-the-line Gen 3 devices], low power [8 hours on battery], and compact,” says Mike Buchin, president of Stanford Photonics. “No matter how good our ICCDs are, they cannot come close to matching the dynamic range [bright to dark] and resolution of the human eye staring at a direct-view NVG. So, most electronic-based night vision [ICCD and thermal] goes where the eye/brain interface can’t: on gimbals, weapons, UAVs, or remote viewing stations. Under those conditions, ICCDs can do what nothing else can.” Stanford Photonics continues to build 1.4 Mpixel off-the-shelf ICCD sensors but acknowledges that to get orders for hundreds of ICCDs, they have to price at levels comparable to direct-view NVGs.
Buchin says that a key discussion point at the Institute for Defense and Government Advancement (IDGA; www.idga.org) Night Vision Systems 2009 conference was that an intensified camera would need to have 5 Mpixels to replace or supplement direct-view NVGs. “At 5 Mpixels, the pixel size of the sensor has to be small to fit within the 16–18 mm active diameter of the intensifier tube,” says Buchin. “Smaller pixels mean less dynamic range and more power to clock out 5 Mpixels at 60 fps. CMOS sensors promise lower power but often need substantial digital signal processing to compensate for sensor fixed pattern noise; plus, DSP needs more power and increases size of the device. Catch 22,” says Buchin. “There is still a lot of work to do. Reliability testing, ruggedization, and production logistics all play into the pace at which the new technologies make it out to the real world.”
REFERENCES
1. www.optics4birding.com/night-vision-generations.aspx
2. www.mc.vanderbilt.edu/news/releases.php?release=1406
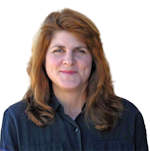
Gail Overton | Senior Editor (2004-2020)
Gail has more than 30 years of engineering, marketing, product management, and editorial experience in the photonics and optical communications industry. Before joining the staff at Laser Focus World in 2004, she held many product management and product marketing roles in the fiber-optics industry, most notably at Hughes (El Segundo, CA), GTE Labs (Waltham, MA), Corning (Corning, NY), Photon Kinetics (Beaverton, OR), and Newport Corporation (Irvine, CA). During her marketing career, Gail published articles in WDM Solutions and Sensors magazine and traveled internationally to conduct product and sales training. Gail received her BS degree in physics, with an emphasis in optics, from San Diego State University in San Diego, CA in May 1986.