SmartFiber to develop fully embeddable integrated-photonic systems for intelligent composites
Leuven, Belgium--SmartFiber, a consortium led by Imec and including partners Ghent University (Ghent, Belgium), Airborne (The Hague, The Netherlands), FBGS Technologies (Jena, Germany), Xenics (Leuven), Fraunhofer (Munich, Germany), and Optocap (Livingston, Scotland), will develop a smart miniaturized system for continuous health monitoring of composites that integrates optical-fiber sensor, nanophotonic chip, and low-power wireless technologies. The idea is to create "intelligent" composites.
The embedded systems will monitor the structural health of composites used as structural parts in wind-turbine blades, satellites, airplanes, civil constructions, oil and gas wells, and boat hulls. The European FP7 funded project SmartFiber will demonstrate a smart system small enough (millimeter-scale) that it can be embedded in a fiber-reinforced polymer.
Automated surveillance
The system is based on silicon nanophotonics and springs from Imec's partnership with its associated laboratory Intec at Ghent University. The chip contains a fiber-interrogation scheme or spectral analyzer as a photonic integrated circuit (PIC) several hundred micrometers in size. This low-power PIC will be electrically connected via wireless communication and inductive power coupling, packaged in a millimeter-sized cage, and coupled to optical fiber Bragg grating (FBG) sensors made by FBGS Technologies.
The microsystems will enable automated surveillance of strain and other changes, and will have a long lifetime in harsh environments. One result should be higher safety at lower cost (due to automated instead of manual surveillance). For example, such a microsystem will enable a wind turbine to operate closer to its design limits, increasing wind-energy capture and thus electrical energy output. It will also provide a continuous record of structural data that will inform decisions on maintenance, warning of potentially catastrophic mechanical failures and eliminating costly periodic checks.
For more info, see www.smartfiber-fp7.eu.
Subscribe now to Laser Focus World magazine; it’s free!
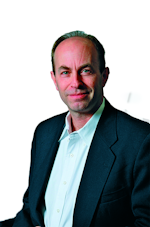
John Wallace | Senior Technical Editor (1998-2022)
John Wallace was with Laser Focus World for nearly 25 years, retiring in late June 2022. He obtained a bachelor's degree in mechanical engineering and physics at Rutgers University and a master's in optical engineering at the University of Rochester. Before becoming an editor, John worked as an engineer at RCA, Exxon, Eastman Kodak, and GCA Corporation.