Southampton, England--The world's first laser-sintered or laser "printed" aircraft was designed and flown by engineers at the University of Southampton. The Southampton University Laser Sintered Aircraft (SULSA) plane is an unmanned aerial vehicle (UAV) whose entire 'snap fit' structure—wings, integral control surfaces, and access hatches—was printed in a laser sintering or laser additive manufacturing (LAM) process. The machine used was an EOS GmbH (Krailling/Munich, Germany) EOSINT P730 nylon laser sintering machine, which fabricates plastic or metal objects by building them up layer by layer by fusing the materials with a laser.
The electric-powered aircraft, with a 2 m wingspan, has a top speed of nearly 100 miles per hour and is almost silent in cruise mode. Laser sintering allows the designer to create shapes and structures that would normally involve costly traditional manufacturing techniques. This technology allows a highly-tailored aircraft to be developed from concept to first flight in days rather than months if using conventional materials and manufacturing techniques such as composites. And because no tooling is required for manufacture, radical changes to the shape and scale of the aircraft can be made with no extra cost.
The SULSA project was led by professors Andy Keane and Jim Scanlan from the University’s Computational Engineering and Design Research group. Scanlon says, "The flexibility of the laser sintering process allows the design team to re-visit historical techniques and ideas that would have been prohibitively expensive using conventional manufacturing. One of these ideas involves the use of a Geodetic structure. This type of structure was initially developed by Barnes Wallis and famously used on the Vickers Wellington bomber which first flew in 1936. This form of structure is very stiff and lightweight, but very complex. If it was manufactured conventionally it would require a large number of individually tailored parts that would have to be bonded or fastened at great expense."
Keane adds, "Another design benefit that laser sintering provides is the use of an elliptical wing planform. Aerodynamicists have, for decades, known that elliptical wings offer drag benefits. The Spitfire wing was recognised as an extremely efficient design but it was notoriously difficult and expensive to manufacture. Again laser sintering removes the manufacturing constraint associated with shape complexity and in the SULSA aircraft there is no cost penalty in using an elliptical shape."
SULSA is part of the EPSRC-funded DECODE project, which is using leading-edge manufacturing techniques, such as laser sintering, to demonstrate their use in the design of UAVs. The University is even launching a groundbreaking course that enables students to take a Master's Degree in unmanned autonomous vehicle (UAV) design. NASA expects UAVs to become 'standard tools' in fields such as agriculture, earth observation and climate monitoring.
SOURCE: University of Southampton; www.soton.ac.uk/mediacentre/news/2011/jul/11_75.shtml
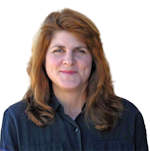
Gail Overton | Senior Editor (2004-2020)
Gail has more than 30 years of engineering, marketing, product management, and editorial experience in the photonics and optical communications industry. Before joining the staff at Laser Focus World in 2004, she held many product management and product marketing roles in the fiber-optics industry, most notably at Hughes (El Segundo, CA), GTE Labs (Waltham, MA), Corning (Corning, NY), Photon Kinetics (Beaverton, OR), and Newport Corporation (Irvine, CA). During her marketing career, Gail published articles in WDM Solutions and Sensors magazine and traveled internationally to conduct product and sales training. Gail received her BS degree in physics, with an emphasis in optics, from San Diego State University in San Diego, CA in May 1986.