Fraunhofer working on laser fabrication of complex lightweight mass-market components
Aachen, Germany--As part of the FibreChain and InProLight projects, researchers at Fraunhofer ILT are developing better and lower-cost laser-based ways of structurally joining lightweight components, including aluminum, high-strength steels, magnesium, titanium, and—above all—fiber-reinforced plastics (FRPs). FRPs consist of an organic matrix reinforced either with carbon fibers or glass fibers.
Production of FRP products is currently hindered by long cycle times and low levels of automation—two significant obstacles to mass production. The EU project FibreChain (funded by the European Union) and the InProLight project (funded by the German Federal Ministry of Education and Research) have set themselves the goal of developing various integrated process chains ranging from specialized schemes to the mass production of fiber-reinforced thermoplastic composites. Fraunhofer ILT’s primary task here is to optimize methods of cutting and joining lightweight components.
Joining plastic to metal by laser
Structurally joining lightweight components traditionally means adhesive bonding or riveting -- two comparatively expensive methods that require extensive preliminary work and extended process time. Andreas Rösner and his colleagues at Fraunhofer ILT have overcome these drawbacks by joining the components using a laser, depositing energy directly into the joining zone. Several complex individual parts can be combined this way and, in addition, structures such as reinforcements can be created via laser. As an extension of the process, the joining of plastics with metal was realized in a two-stage laser process. First, the metallic component is structured with a high-brightness laser beam, and then is heated using a diode laser. Softened plastic penetrates into the structured metal, leading to an excellent mechanical claw bonding between the joined parts.
Cutting without damaging edges
As well as cutting raw material, it is necessary to trim components and cut out the required holes and sections. Conventional laser cutting techniques often damage edges due to the size of the heat-affected zone. Frank Schneider and his colleagues developed a series of new cutting methods, one of which uses an innovative short-pulse CO2 laser, achieving a nearly complete elimination of thermal damage. Even highly sensitive material combinations in aeronautics can be processed economically by these lasers at powers up to 500 W.
To demonstrate practical feasibility, the Fraunhofer scientists have successfully applied these techniques to car-seat backs made by the company Weber. Applications of the technique will include auto and aircraft manufacturing, shipbuilding, spaceflight engineering, highly dynamic machines, and civil engineering projects.
Laser Lightweight Construction Center
Fraunhofer ILT’s Laser Lightweight Construction Center is currently being set up in the Institute's laser machine facility. It will be presented as part of the “Laser Technology Live” event at the International Laser Technology Congress AKL’12 on May 11, 2012. The new Center will bring together various laser systems under one roof, including a gantry system for fiber-coupled machining of 3D sheet metal and FRP components and a 2D laser machine with acceleration parameters of up to 5 g. Fraunhofer ILT’s Lightweight Construction Centre will also include a machine with 3D capabilities and a CO2 laser for the machining of FRP components. Rounding out the center’s facilities are high power ultrashort pulse lasers that can process carbon-fiber-reinforced plastic components in particular.
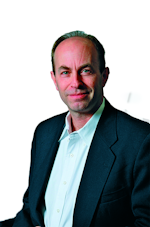
John Wallace | Senior Technical Editor (1998-2022)
John Wallace was with Laser Focus World for nearly 25 years, retiring in late June 2022. He obtained a bachelor's degree in mechanical engineering and physics at Rutgers University and a master's in optical engineering at the University of Rochester. Before becoming an editor, John worked as an engineer at RCA, Exxon, Eastman Kodak, and GCA Corporation.