Thin-disk laser master oscillator power amplifier (MOPA) has advanced cooling arrangement
Researchers at the U.S. Army Research Laboratory (ARL; Adelphi, MD) have boosted the power of a thin-disk laser power amplifier design of theirs that has greatly enhanced cooling properties.1 The amplifier allows power scaling to be extended up to two and a half times, while maintaining a very high quality beam. Their results in 2010 showed a 12 W optical output; the new results show outputs up to 55 W.
In a master-oscillator power-amplifier (MOPA), the extent to which the power of the master oscillator (seed laser) can be scaled is inherently limited by the heat generated and the laser system's ability to deal with it.
One way to limit the heat generated in the amplifier is to operate it in quasi-continuous-wave (QCW) mode at a duty cycle less than 100%. By pulsing the PA pump power, the overall thermal load on the pumps and the laser-gain element is reduced, while still allowing for the same momentary power of CW operation without output-beam-quality degradation.
These kinds of source are used in a range of applications within machining, medicine and nonlinear optics, as well as military applications, including rangefinders and designators, but their power scaling is still limited by cooling requirements.
Thin-disk geometry
"Any laser system has its power limit and further power scaling requires additional sophistication in thermal management of the gain element," says ARL researcher George Newburgh. "Legacy-design thin-disk lasers (TDLs) offer advanced thermal management compared to rod-based or slab-based lasers, due to their much larger surface area to gain volume ratio, but their thermal management is still limited by single-sided cooling."
The ARL researchers address the cooling issue by using an optically transparent heat sink to allow the gain medium to be cooled from two sides, extending the possible power scaling range by a factor of around 2.5.
As well as the normal copper heat sink attached to the nonlasing side of the gain element, their design uses a transparent, single-crystalline silicon carbide (SiC) component to act as a heat sink on the lasing/pumping side. This component is as thermally conductive as copper, providing excellent heat transport without interfering optically with the laser's operation.
Minimizing mechanical stress
The compact amplifier has also been designed to minimize mechanical stress between the SiC heat sink and the gain medium through the choice of yttrium orthovanadate (YVO4) as the laser host medium. The thermal expansion coefficients of SiC and Nd:YVO4 are nearly the same, allowing the amplifier to operate at high temperatures without the SiC and YVO4 layers delaminating.
The ARL reserachers hope that this work, along with the latest developments in high quality laser ceramics, including composites, and recent advances in alternative high optical quality transparent materials, such as gallium nitride and magnesium oxide, will encourage more research and development using transparent materials with high thermal conductivity.
In the shorter term, the authors think the design could be used almost immediately in power amplifiers for nanosecond pulse amplification in a hybrid fiber/bulk solid-state MOPA system to meet high pulsed energy requirements, where fiber amplifiers are severely limited by stimulated Brillouin scattering.
Source: http://www.theiet.org/resources/journals/eletters/5016/clear-cooling.cfm
REFERENCE:
1. G. A. Newburgh and M. Dubinskii, Electronics Letters (2014); doi: 10.1049/el.2014.1900
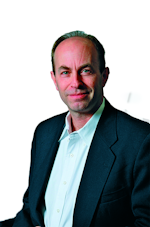
John Wallace | Senior Technical Editor (1998-2022)
John Wallace was with Laser Focus World for nearly 25 years, retiring in late June 2022. He obtained a bachelor's degree in mechanical engineering and physics at Rutgers University and a master's in optical engineering at the University of Rochester. Before becoming an editor, John worked as an engineer at RCA, Exxon, Eastman Kodak, and GCA Corporation.