Will Zhang, an astrophysicist at NASA’s Goddard Space Flight Center (Greenbelt, MA), has shown in repeated testing that single-crystal silicon works exceptionally well as an X-ray optic. Given the cost of building space observatories, the goal is to develop easily reproducible lightweight optics without sacrificing quality.
According to Zhang, use of silicon would give x-ray astrophysicists what they have long wanted: lightweight, super-thin mirrors that offer a significantly larger collection area and dramatically improved resolution, all at a reduced cost.
To date, no one has created an x-ray mirror that addresses all these performance goals. Furthermore, no one has polished and figured silicon for x-ray optics, which take a grazing-incidence configuration and thus must be curved and nested inside a canister-like assembly to collect highly energetic x-ray photons.
Silicon, which doesn't warp even when cut or exposed to fluctuating temperatures, offers a viable solution, says Zhang.
Another Goddard technologist, Vince Bly, had previously investigated the material’s use of silicon for mirrors, ultimately producing a thick, yet lightweight spare mirror for the Goddard-built Thermal Infrared Sensor, one of two instruments developed for NASA’s Landsat Data Continuity Mission. Though the mission didn't use the mirror because the optic had never flown in space, Bly says testing indicated that it offered a viable option.
Crystal eliminates internal stresses
When Zhang heard about Bly's work, he and Bly started working together, benefiting from each other's experience. "Single crystal silicon is an excellent material for making space-flight x-ray mirrors," he says. He notes that silicon's crystalline structure makes it immune from the internal stresses that can change the shape of x-ray mirrors made of glass.
In the new process, a block of silicon is first heated to eliminate any stress that may have arisen from its handling. With a band saw, Zhange then creates the approximate shape and uses other machining tools and chemicals to further grind and refine the block's surface. He then cuts a thin substrate measuring a fraction of an inch in thickness from the block and polishes the surface. The last step is coating the individual segments with iridium to improve reflectance.
With NASA funding, Zhang and his team are perfecting techniques for aligning and bonding 6000 mirror segments to form metashells that would be integrated inside a mirror assembly projected to weigh about 200 pounds and stand 1.6 feet tall. Ultimately, he would like to create six metashells and automate the alignment process.
Source: https://www.nasa.gov/feature/goddard/2017/nasa-advances-first-ever-silicon-based-x-ray-optic
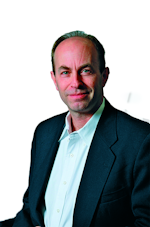
John Wallace | Senior Technical Editor (1998-2022)
John Wallace was with Laser Focus World for nearly 25 years, retiring in late June 2022. He obtained a bachelor's degree in mechanical engineering and physics at Rutgers University and a master's in optical engineering at the University of Rochester. Before becoming an editor, John worked as an engineer at RCA, Exxon, Eastman Kodak, and GCA Corporation.