PHOTONIC FRONTIERS: JAMES WEBB SPACE TELESCOPE - Space telescope to see farther in the IR
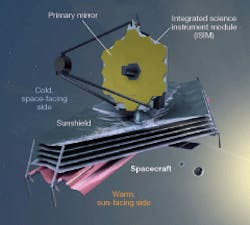
The successor to the Hubble Space Telescope is slowly taking shape. Like Hubble, the James Webb Space Telescope is intended to be the premier space telescope of its time, peering back into the distant universe to observe the birth of stars and galaxies. To achieve that goal scientists will have to overcome a formidable set of technical challenges quite different from those faced by Hubble.
Hubble’s designers didn’t have to start from scratch on the optics for the 2.4-meter telescope. Spy satellites used lightweight mirrors of similar size to look down at the Earth so Hubble designers modified the optics to look up at the sky. Hubble fit into the space shuttle, and was designed for regular service missions by astronauts-a choice that proved to be its salvation when it was launched with a misfigured main mirror. Webb doesn’t have that luxury. After the Challenger explosion in 1986, NASA stopped designing satellites that required regular astronaut service missions. Webb’s 6.6 m main mirror is too large to fit on any existing launch vehicle, so it will be folded on the ground and opened up in space. Because it will observe in the infrared (IR), it must be kept cool, which requires careful thermal design and an orbit 1.5 million kilometers from Earth.
It hasn’t been easy. But by the end of this year, all the critical technologies will have been tested, a key milestone on the road to a 2013 launch.
Looking deeper into the universe
Webb began as the Next Generation Space Telescope, but astronomers didn’t want just to build a bigger and better version of Hubble. They wanted to go farther back in time, closer to the big bang, to watch the birth of galaxies and stars. That meant observing at IR wavelengths, where astronomers can see the red-shifted light from the earliest stars and galaxies.
The Spitzer Space Telescope is the latest in a series of satellites that show the potential of IR astronomy in space. The atmosphere absorbs many IR wavelengths, but the most fundamental problem is the brightness of the IR sky. Thermal emission clouds the IR sky, making ground-based astronomy virtually impossible, even in atmospheric windows at longer wavelengths. Looking for IR sources at the edge of the universe requires the dark sky of space. It also requires a big telescope to collect the faint light. Original plans were for an 8 m primary mirror, but budget problems decreased the size of the primary to 6.6 m.
Thermal radiation from the observatory itself can also contaminate images, so the whole Webb telescope and its imaging instruments must be kept cold. That means selecting an orbit 1.5 million kilometers beyond the low-Earth orbit of Hubble at the Earth’s Lagrange 2 (L2) point, so the planet’s thermal radiation does not affect the telescope. The observatory also includes a reflective sunshade that will be unfurled in space to keep the telescope in the shade (see Fig. 1).
A giant deployable mirror
The most challenging technology is the primary mirror, says Webb project scientist John Mather—2006 Nobel Laureate in Physics—of the NASA Goddard Space Flight Center (Greenbelt, MD). Nothing like it has ever been done “at this level of light weight and precision.”The primary will be assembled from 18 lightweight beryllium hexagons, each 1.32 m across. Each segment will be figured to one of three aspheric shapes, depending on its location in the primary. The time-consuming fabrication process is already well under way. Mather says grinding of ten of the primary-mirror segments has been finished at the Axsys Technologies plant in Cullman, AL. Nine have been shipped to Tinsley Laboratories (Richmond, CA) for polishing. Gold coatings will make the finished mirror highly reflective from 0.6 to 29 µm.
Blocks of three segments on opposite sides of the mirror will be hinged so they can be folded into a compact package for launch and then opened up in space (see Fig. 2). The tripod-mounted secondary also will be folded down for launch, then opened up in space before the mirror is unfolded, one flap at a time.
Alignment of the mirror segments will be maintained by a wavefront sensing and control system that analyzes photos of bright stars taken by Webb to determine how to adjust the segments to the desired figure. The mirror is designed to be stable enough that the segments will need adjustment only once a week, giving more time for observations. Specifications call for the primary surface to be diffraction-limited at 2 µm, with a Strehl ratio of 0.8. The telescope has an effective focal length of 131.4 m, with the primary focusing light onto a 74 cm secondary mirror. A tertiary mirror and a flat fine-steering mirror will direct light onto the instruments behind the primary and provide fine pointing of the telescope. Reaction wheels will adjust coarse pointing of the whole telescope.
Scientific instruments
Four scientific instruments share the telescope’s field of view with the fine-guidance sensors. Their fields of view don’t overlap, so all can be used simultaneously for observations or monitoring. All instruments will operate all the time-whether or not data is being collected-to aid in thermal management.
The Near-Infrared Camera splits input light with a dichroic filter, directing the 0.6-to-2.3 µm band to a set of eight 2048 × 2048 arrays of mercury cadmium telluride detectors, and the 2.4-to‑5 µm band to a separate pair of 2048 × 2048-element detectors. Each band has filter wheels with a dozen filters, for selecting observation bands. The NIR camera’s field of view is 2.2 × 4.4 arcminutes.
The Near-Infrared Spectrograph can simultaneously observe spectra of more than 100 objects in a field 3 arcmin square. Six gratings can take spectra at two different resolutions in three bands from 1 to 5 µm; a single prism takes lower-resolution spectra from 0.6 to 5 µm.
The separate Tunable Filter Imager uses Fabry-Perot etalons to select a narrow range of near-IR wavelengths for imaging a 2.2 arcmin field.
Imaging and spectroscopy from 5 to 29 µm are performed by the Mid-Infrared Instrument using 1024 × 1024-pixel arrays of arsenic-doped silicon (As:Si) detectors. Separate channels handle imaging and spectroscopy. An active cooling system, powered by Webb’s solar array, will cool the MIRI assembly to 7 K for low-noise operation. This system does not require a cryogen, so it should not limit Webb’s operating life.
Orbit and thermal management
Passive cooling will keep the rest of Webb at a temperature below 50 K. The key component is a large Kapton sunshield with a coating that reflects sunlight away from the cold parts of the observatory. After the sunshield unfolds in space, Webb will remain behind it, avoiding solar heating and gradually cooling to the desired operating temperature.Working behind the sunshield at the L2 point, Webb will be able to use more than 70% of its telescope time for observations, much more than Hubble can in low-Earth orbit. About 40% of the sky will be observable at any time (see Fig. 3). NASA says that Webb will be able to observe all parts of the sky for at least 51 continuous days during some part of the year, and to observe 30% of the sky for at least 197 continuous days. Small areas around the poles will be observable all year. That’s a big advantage over Hubble, whose observing intervals are limited by its low-Earth orbit.
The L2 point is not dynamically stable, so Webb will orbit it with a six-month period, and will require periodic station-keeping to maintain proper position. Webb will carry enough station-keeping propellant for a 10-year lifetime; when it’s exhausted, the telescope will gradually drift away from the L2 point.
Status and outlook
Like Hubble, Webb has fallen behind its original schedule and is well over its planned budget, but Webb itself has also grown. When planning started in 1996, NASA had set aside $500 million to build a 4 m telescope with one instrument. Then former NASA administrator Dan Goldin suggested aiming for 8 m, and astronomers added more instruments. By the time the first requests for proposals were issued in 2001, the construction budget of the bigger and better instrument was around $2 billion. Later changes in NASA accounting added a few hundred million dollars to the budget, and last year overruns and delays added about another $1 billion. NASA now estimates the complete lifecycle cost-including about $1 billion in operations-will be $4.5 billion, not counting an Ariane V launch being supplied by the European Space Agency in 2013.
But Mather says the program has stayed on budget and on schedule since last year’s changes. Key technologies are being tested to meet milestones at the end of this year. The primary-mirror segments, which have the longest lead times, are already in production. And mindful of the fiasco of Hubble’s misshapen primary mirror, NASA has planned an end-to-end test to check how the fully assembled Webb transmits light on the ground before launch.
FURTHER READING
J.P. Gardner et al., in press, Space Science Reviews; on line at www.jwst.nasa.gov/resources/JWST_SSR_JPG.pdf.
About the Author
Jeff Hecht
Contributing Editor
Jeff Hecht is a regular contributing editor to Laser Focus World and has been covering the laser industry for 35 years. A prolific book author, Jeff's published works include “Understanding Fiber Optics,” “Understanding Lasers,” “The Laser Guidebook,” and “Beam Weapons: The Next Arms Race.” He also has written books on the histories of lasers and fiber optics, including “City of Light: The Story of Fiber Optics,” and “Beam: The Race to Make the Laser.” Find out more at jeffhecht.com.