SPECTROSCOPY: Spark-plug laser sensor characterizes IC engines as they run
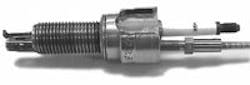
Since the enactment of emission limits for cars and the 1973 oil embargo, much engineering effort has gone into making internal-combustion (IC) engines the marvels of efficiency that they now are. But further advances require IC engineers to rely on ever more sophisticated tools. Researchers at Stanford University (Stanford, CA), Physical Sciences (Andover, MA), and Nissan Motor Co., (Kanagawa, Japan) have created just such a tool-a diode-laser-based water-concentration and temperature sensor that measures combustion-chamber conditions using wavelength-modulation spectroscopy with second-harmonic detection.
Turbocharging and even supercharging are becoming more common in production automobiles; in addition, new engine designs, such as homogenous charge-compression ignition (which combines spark- and diesel-type ignition schemes) are being developed. The temperature and chemical makeup of the combustion-chamber air-fuel mix in all these schemes must be well characterized throughout the combustion cycle to provide useful data for IC-design engineers. The new diode-laser sensor, which is built into a spark plug and does not alter the plug’s operation, is designed to survive and characterize the wide range of temperatures and pressures encountered in the combustion cycle prior to ignition (up to 50 atm and from 500 K to 1050 K) at a 7.5‑kHz bandwidth.
The light from two fiber-coupled distributed-feedback lasers is multiplexed into a single-mode fiber that terminates at the spark-plug probe. The lasers, which emit near 1.39 µm, are wavelength-modulated (by varying their current) through a 0.7 cm-1 range, one laser at 70 kHz and the other at 85 kHz. The light emitted from the fiber passes through a sapphire window at the probe and is focused by a mirror back through the window onto an adjacent multimode light-collecting fiber; the total path length in the combustion chamber is 12 mm. The multimode fiber terminates at an indium gallium arsenide photodetector with a 500-kHz bandwidth. The return laser signals are frequency-demultiplexed with phase-sensitive digital lock-in amplifiers, which pass the first (1f) and second (2f) harmonics of the two modulation frequencies.
Second-harmonic detection
Because wavelength modulation with second-harmonic detection is sensitive to the curvature of the spectral feature, rather than the magnitude of absorption, it is well suited to low absorbances and pressure-broadened spectral features. The 2f signal is strongest when the ratio of the laser modulation depth to the half-width at half maximum (HWHM) of the spectral feature is about 2.2; thus, broader features require larger wavelength modulation. The 1f signal is used to normalize the 2f signal (after the 2f nonzero background for no absorption is subtracted) for laser intensity and detector gain.
Finally, the sensor was tested in a fired single-cylinder engine running at 1200 rpm, a 12:1 compression ratio, an air-to-fuel ratio of 14:1, and an intake water mole fraction of 1.4%. Resulting data included temperature as a function of crank angle (see figure). Comparing the data from fired and unfired cases reveals phenomena such as the heating of incoming gas by the hot intake and cylinder walls-the sort of data needed to help engineers design cleaner engines.
“When properly designed and mixed, the spark will initiate a high-intensity, smoothly burning, and completely combusting event,” says Mark Allen, vice president of photonics enterprise at Physical Sciences. “This improves power, reduces engine wear, and minimizes unwanted pollutant formation. The sensor allows engineers developing new engine designs to accurately measure the effect of their designs upon the gas mixture properties at the spark plug. This type of instrumentation has not been previously available.” The device could also be useful in the design of other types of IC engines, such as those for aircraft, large stationary power, tractors, and lawn mowers, says Allen.
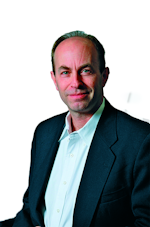
John Wallace | Senior Technical Editor (1998-2022)
John Wallace was with Laser Focus World for nearly 25 years, retiring in late June 2022. He obtained a bachelor's degree in mechanical engineering and physics at Rutgers University and a master's in optical engineering at the University of Rochester. Before becoming an editor, John worked as an engineer at RCA, Exxon, Eastman Kodak, and GCA Corporation.