FIBER-OPTIC-SENSORS: Miniature read-out sensor resolves wavelength changes to 50 fm
Many optical sensors rely on the detection of small wavelength changes in response to changes in temperature, strain, adhesion of bioparticles, or change in the chemical environment for the system under test. Examples include fiber-Bragg-grating (FBG)-based sensors, laser-cavity, microsphere, or microring-based sensors, and surface-plasmon-resonance or photonic-crystal sensors. Despite advantages that include electromagnetic-interference (EMI) immunity and use in remote and distributed-sensing applications, optical sensors typically require bulky and expensive interrogation systems (such as a broadband light-source/grating-based spectrum analyzers or a tunable light source with photodetector) capable of resolving small wavelength shifts to subnanometer or even picometer resolution. But a new technique developed by researchers at Palo Alto Research Center (PARC; Palo Alto, CA) incorporates a position-sensitive detector to create a miniature read-out interrogator unit that can resolve wavelength changes as small as 50 fm.1
Since their presentation at Photonics West 2010, the researchers have developed a prototype read-out wavelength monitor that fits in a standard transistor-outline (TO) header.
The wavelength-shift detector
To monitor minute wavelength changes at a rapid rate, a linear variable optical filter is placed on top of a position-sensitive detector (either a linear photodetector array or a position-sensitive photodetector). Because the optical properties of the filter change linearly with position in a specified direction of the filter, the laterally varying transmission defines the correlation between the wavelength of the incoming light and the position of the light spot transmitted by the filter; thus, the position of the transmitted light spot yields the wavelength of the incident light. By optimizing the filter coatings, different wavelength ranges can be accessed. In operation, a linearly varying Fabry-Perot filter on top of a split diode translates the spectral information of the incident light into spatial information on the position-sensitive detector.
For the linear variable filter, the researchers developed an optimized 1550 nm Fabry-Perot filter coating that consists of two distributed Bragg reflectors that are separated by a laterally graded cavity. The gradient of the filter—2.4 nm/mm—specifies the spectral shift of the transmission peak when the location on the filter is changed. To optimize the detector for selected applications, the researchers developed a Matlab (The Mathworks; Natick, MA)-based simulation tool that takes into account optical sensing noise factors such as detector dark current, amplifier noise, and shot noise—the latter being the dominant noise source for the low optical input power of most FBG and other optical biosensors.
Proof of concept
A prototype wavelength-shift detector was assembled in a TO header and used to record output from a FBG strain sensor in response to a piezoelectric actuator (see figure). A 1550 nm superluminescent LED (SLED) is coupled to the optical fiber that guides the light to a FBG mounted on a piezo actuator inside an environmental chamber. The reflected light from the FBG (90% reflectivity at the resonance peak with FWHM of ~0.2 nm) is guided to the wavelength-shift detector as the piezoelectric actuator drives a 100 Hz vibration signal, inducing strain in the FBG and causing a spectral response. The observed amplitudes of the vibration signal are 0.04 με and 0.08 με strain, corresponding to detected wavelength shifts of 50 fm and 100 fm, respectively.REFERENCE
1. K. Bellmann, P. Kiesel, and N. Johnson, "Compact and fast read-out for wavelength-encoded biosensors," Proc. SPIE, 7593-32 (2010).
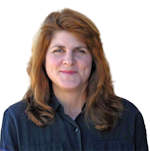
Gail Overton | Senior Editor (2004-2020)
Gail has more than 30 years of engineering, marketing, product management, and editorial experience in the photonics and optical communications industry. Before joining the staff at Laser Focus World in 2004, she held many product management and product marketing roles in the fiber-optics industry, most notably at Hughes (El Segundo, CA), GTE Labs (Waltham, MA), Corning (Corning, NY), Photon Kinetics (Beaverton, OR), and Newport Corporation (Irvine, CA). During her marketing career, Gail published articles in WDM Solutions and Sensors magazine and traveled internationally to conduct product and sales training. Gail received her BS degree in physics, with an emphasis in optics, from San Diego State University in San Diego, CA in May 1986.