The earliest fiber laser is credited to Elias Snitzer in 1961, and the first coherent light emission from a semiconductor diode (the first diode laser) was demonstrated in 1962 by two US groups at GE and IBM. Fiber laser technology has since been scaled up into power levels as high as those achieved by the older, “historic” CO2 laser technology. It is at this 50 kW average power level that the differences in the technology are brought into the sharpest focus: A 50 kW CO2 laser occupies the space of a small house, whereas the space occupied by a 50 kW fiber laser is closer to that of a large freezer cabinet.
Other benefits of fiber lasers such as ease of use, lack of complexity, near-zero maintenance, wall-plug efficiency, and low running costs are now well accepted. The incumbent CO2 technology will always be difficult to displace as some users will prefer to stick with familiar products and technology, as well as established laser supplier relationships.
Fiber laser structure
A fiber laser comprises a series of fiber components physically spliced together so the laser beam never leaves fiber-optic cable until it emerges from the fiber to be focused onto the workpiece. When this engineering approach is combined with the use of single-emitter pump diodes, the result is the most robust and longest-lasting laser tool available. The mean time between failure (MTBF) lifetimes for single-emitter pump diodes are 300,000 h. Although based on solid statistical data, these numbers are simply too high for some laser users to believe. Perhaps the lack of credibility given to these typical telecom lifetime numbers is at least partly due to the lifetime issues associated with using diode bars or diode stacks for pumping; many diode bar and especially diode-stack pumped solid-state (DPSS) lasers had acquired a rather poor reputation for reliability just before the advent of fiber lasers.
Fiber laser technology has faced many challenges: sensitivity to backreflection, the mysterious effect of photo-darkening or fiber degradation over time, and most recently the differences between all infrared (IR) solid-state lasers (both disk and fiber) and CO2 lasers when cutting materials thicker than 15 mm. Although a full explanation of the solutions to these problems is beyond the scope of this article, all of these issues have now been resolved.
Low-power fiber laser developments
The economies of scale that have been achieved by vertical integration have been realized due to high-volume sales at both the high- and low-power ends of the spectrum. At low power, sales of flashlamp-pumped laser markers have been eclipsed by low-power fiber laser sales. Tens of thousands of these low-power units have been sold, and almost every marking-system manufacturer has a fiber-laser-based marker in its product lineup.
This coverage of the whole laser power range, based on in-depth understanding of the science of fiber lasers, has been necessary as has tight control of the specifications of every fiber-based component in each fiber laser system. This has led to the buildup of a large “toolbox” of fiber-based components that can be mixed and matched to produce a very extensive range of lasers. A brief examination of the range of fiber-laser components that are being produced and utilized by the ultrashort-pulse laser community illustrates this point.
Where is this scalable modular technology going in the low-average-power regime? The answer is in many different directions. We will cover several but not all of these directions at the low-power end of the scale.
Nanosecond to microsecond pulsed fiber lasers
Standard nanosecond laser marking modules have satisfied the majority of run-of-the mill laser marking applications until recently. These lasers are available at power levels up to 50 W with an identical footprint and with no decrease in brightness.
This combination of high average power and high brightness is required to maintain the high ablation efficiencies shown in the table. In fact, a derivative of this same laser type is available at up to 500 W average power with pulse energies up to 50 mJ. Exciting new applications for this laser include very high-speed removal of a range of films and coatings.
Variable-pulse-length fiber master oscillator power amplifier (MOPA) systems at the 20 W power level have been available for years with pulse lengths as short as 4 ns. Only recently has this extra refinement been appreciated as users become more familiar with advanced laser-marking techniques. One example is using a low-nanosecond laser to produce a black mark in polycarbonate that is almost completely sub-surface; this satisfies applications where a minimum of surface disruption is required. An additional interesting development of this process is to use this mark as an absorber for a subsequent polymer welding process using the same nanosecond IR laser.
Another example for metals is the technique known as “dark marking.” This is well known for high-contrast, indelible, and corrosion-resistant marks on stainless steels for the medical device industry. The technically incorrect term often applied to this technique is “anneal marking.” In this case, a low-power laser technique is used at high repetition rate to ensure high spot overlap and even, localized heating of the surface of various stainless steels to grow a smooth, crack-free, and corrosion-resistant coating with high contrast. This specialized mark is widely used on surgical instruments as no surface disruption is involved.
Although there is a widely held view that shorter pulse lengths or pulse durations are preferred in every case, pulse length is only one of several important variables involved in these processes: A level of pulse energy and fluence or peak power density is also required, hence the importance of brightness. The next generation of this laser type is already available with M2 as low as 1.2 (some may call this singlemode), pulse lengths down to 1 ns, and peak powers up to 40 kW. Picosecond versions will be available early in 2012.
Microsecond to millisecond high-pulse-energy fiber lasers
Another recent development is known as the quasi-continuous-wave (QCW) fiber laser. This is another extension of the fiber-laser concept that takes it into one of the last bastions of flashlamp-pumped laser technology: high-pulse-energy, low-duty-cycle laser processing. In this case, vertical integration and highly cost-effective manufacture of pump diodes, an understanding of nonlinear thresholds, and careful design have enabled a flexible range of lasers with a maximum pulse energy of 60 J. The lowest-power-level laser at 150 W has a capability of 15 J and 10 Hz in a pulse length identical to that a flashlamp-pumped laser of 10 ms (see Fig. 1).
Can this 60 J of pulse energy really be generated in a singlemode fiber? Clearly the question has now been answered in the affirmative, although very few real-world applications actually need this level of pulse energy. Trials have shown that the laser can not only produce the sort of large weld-nugget diameters required by many low-power welding applications but it is also capable of cutting high-reflectivity materials such as aluminum and copper up to several millimeters thick.
Temporally shaped millisecond pulses
The latest addition to the capability of the QCW lasers is a laser control package known as the pulsed signal generator (PSG); this allows a very high number of complex temporal pulses to be programmed.
Temporal pulse control was widely applied to flashlamp-pumped lasers many years ago and was seen as essential to certain spot-welding applications. The need arose when a slow ramp-down was required at the end of the laser pulse to prevent porosity associated with the collapse of the pseudo-keyhole at the end of a seam of overlapping laser spot welds. The advantage of the fiber laser in this instance is that the pump diodes have much shorter switch-on times than the flashlamps employed in conventional flashlamp-pumped lasers; therefore, smaller increments or sectors of pulse length and more complex shapes are possible.Longer-wavelength fiber lasers
Erbium and thulium rod lasers emitting in the spectral range of 1.5–2 µm have been in existence for some time but have not previously been used for materials processing. High-brightness fiber laser variants have been deployed in a variety of medical and airborne applications for a number of years.
Many polymers have increased absorption at these wavelengths; it has only recently been established that this level of absorption is suitable for welding optically clear polymers, thus eliminating the need for specific IR absorbers. When using singlemode high-brightness lasers, even collimated beams produce more than enough power density to produce high-quality optically clear joints in both the butt and lap weld configurations. The absorption of a few polymer types is shown in the table.
The startling speed with which these advances have occurred is evidence of the inherent scalability of the fiber-laser concept. Scaling to even higher powers and adding more fiber and more pump diodes may be achieved by fiber laser experts who fully understand the nonlinear thresholds involved.
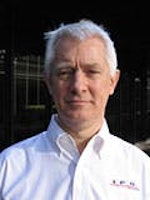
Tony Hoult
Dr. Tony Hoult is trained as a Materials Engineer and has been working for many years as a Laser Materials Processing specialist. He worked in the UK on early high power solid state lasers followed by a lengthy period as a Researcher at the University of Warwick.
He moved to the US in 1999 and set up the IPG Photonics Applications facility in Silicon Valley eight years ago. Since then, he has been working on laser processing with a wide range of advanced fiber laser sources at multiple laser wavelengths.