MATERIALS PROCESSING: 100 kW fiber laser, power meter serve industry
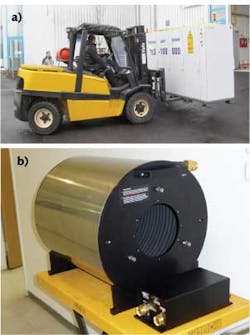
The first commercial 100 kW fiber laser, a surprisingly small system developed by IPG Photonics (Oxford, MA), has been sold to the NADEX Laser R&D Center (Nagoya City, Japan), a materials-processing research laboratory that is using the laser to weld 300-mm-thick metal parts. The industrial-class 1070.5-nm-emitting laser, which stands only 1.86 × 3.6 × 0.8 m and has a mass of 3600 kg (see figure), has been in operation at NADEX for six months. The lab is using the laser as part of its effort to develop a robust laser-based manufacturing environment using off-the-shelf hardware.
Uses include shipbuilding, rock-cutting
The laser was developed for heavy-duty applications such as shipbuilding (mobile cutting and welding), remote welding and cutting of large-scale products in the field, “in-field” ultrahard rock and concrete cutting and drilling, construction of components for nuclear power plants, and other heavy industrial deep-penetration welding and cutting, says Alexei Markevitch, market-development manager at IPG Photonics.
The laser’s output is directed into a 10-m-long, 300-μm-diameter feeding fiber; this output in turn can be coupled into a 50-m-long, 500-μm-diameter process fiber for remote delivery of the laser’s output. With an optical output of 101.3 kW at the output end of the process fiber and a 286 kW electrical power consumption, the complete system has a high wall-plug efficiency of 35.4%.
The laser is made up of 90 individual laser modules, each with a 1.4 kW optical output and a beam quality (M2) of 1.05. Six integrated fiber-to-fiber, 19-to-1 combiners make up the first beam-combining stage; the second stage contains a single fiber-to-fiber, 7-to-1 combiner. The measured beam-parameter-product (BPP) value of the beam exiting the feeding fiber is less than 16 mm*mrad, while the BPP of the beam exiting the process (remote delivery) fiber is 25 mm*mrad.
The laser’s optical output changes by no more than 0.2% root-mean-square (RMS) over 30 minutes, says Markevitch. In addition, there are no detectable nonlinear effects in the output spectrum, even at highest power. The laser turns on in 40 μs and off in 25 μs, and can be modulated digitally or analog at rates up to 5 kHz. The entire system is easy to transport, notes Markevitch.
Calorimetric power meter
Of course, the question arises: How does a user measure the output power of a 100 kW laser? Conventional laser power meters that rely on absorbing surfaces can measure laser powers to 30 kW; however, an output of 100 kW is another thing entirely.
To solve this problem, Ophir Photonics (North Logan, UT) has developed a new laser power meter that relies on a calorimetric design to measure beam powers of up to 100 kW. Gary Wagner, general manager of Ophir Photonics, notes that the 100 kW laser power meter is a fully commercial product and that the first one is installed at NADEX along with the IPG Photonics fiber laser. Engineers at NADEX have already used the Ophir power meter to measure the full output power of the fiber laser (which has its output end mounted on a robot arm).
The Ophir measurement unit itself is barrel-shaped, 300 × 110 × 150 mm in size, and intended to be placed in a diverging beam produced after the focus of a lens with a 500 to 1000 mm focal length. Inside the unit is a highly reflective deflecting cone that receives the beam at approximately 100 mm in diameter. The cone deflects the light to the sides of the barrel, which are lined with a coiled, black-absorber-coated copper tube through which water flows; the arrangement traps more than 99% of the laser light. By measuring the volume of water flow and the temperature rise, the laser power dumped into the power meter can be calculated. Linearity is ±1% or better over a power-level range from 10 to 100 kW, says Ophir.
The power meter is calibrated for a 1070 nm wavelength (matching that of the IPG 100 kW fiber laser); this wavelength will make up the majority of applications, says Wagner, although other wavelengths can be calibrated if needed. With the meteoric rise in fiber-laser powers these days, “we are focusing more and more on high power optics as a company,” notes Wagner.
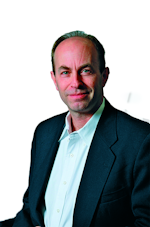
John Wallace | Senior Technical Editor (1998-2022)
John Wallace was with Laser Focus World for nearly 25 years, retiring in late June 2022. He obtained a bachelor's degree in mechanical engineering and physics at Rutgers University and a master's in optical engineering at the University of Rochester. Before becoming an editor, John worked as an engineer at RCA, Exxon, Eastman Kodak, and GCA Corporation.