Photonics Products: Mounts and Accessories: Tip/tilt mirror mounts deliver accuracy, stability
If any type of optical mount designed for lab experimentation could be called "iconic," it would be the kinematic tip/tilt optical mount, which is most often used along with a flat mirror for beam steering. Given an optical table, a laser or two, a scientist or engineer, and an idea being translated (or, in this case, rotated) into reality, at least a few kinematic mounts will surely be right there, too, fixed to the table.
While both manual and motorized kinematic mounts are available, the manual version most straightforwardly demonstrates the form and function of a kinematic mount. In such a device (which can come in many sizes to fit large or small optics), the mirror or other optic is fastened to a movable plate that is in turn kinematically mounted to the fixed portion of the assembly, allowing the position of the optic to be angularly adjusted in two orthogonal directions (often called tip/tilt).
The three-point "kinematic" link between the fixed and moving pieces consists of a pivot point and two screw actuators placed at 90° to each other in relation to the pivot point to ensure orthogonal adjustment. The pivot point can be a third screw, allowing translational adjustment of the mirror as well. The fixed portion of the mount commonly bolts to an optical post that can itself be mounted rigidly to the table.
Other types of tip/tilt optical mounts include flexure mounts, which use flexures as constraints, and gimbals, which contain orthogonal pivots and are often motorized.
Cone, groove, and flat constraint systems
In addition to initial alignment of laser beams, "kinematic mounts also allow the user to adjust for changes in laser pointing in long-term operation, in addition to correcting boresight and wedging in optical elements throughout the optical setup," says Ra'ef Mikhail, laser optics product line manager at Edmund Optics (Barrington, NJ), which produces both manual and motorized kinematic mounts of many sizes.
"When I was working in our R&D lab, the kinematic mounts were indispensable in our laser experiments," says Mikhail. "Often with long-term operation of our laser systems, the beam pointing will change ever so slightly, causing the entire optical system to fall out of alignment. However, as it is a common practice to use two kinematic mounts at the head of the laser, we were able to precisely control the direction and height of our laser beam, making minor adjustments to ensure our system remained aligned for our precise applications."
The company's TechSpec kinematic mounts use the classic cone, groove, and flat constraint system (see Fig. 1). Mechanical systems are classified by the number of degrees of freedom present. "A 3D rigid body has six independent degrees of freedom including translation in x, y, and z, and rotation in Rx, Ry, and Rz, also known as yaw, pitch, and roll, respectively," explains Mikhail. "A mount is considered kinematic if all degrees of freedom are fully constrained. The adjustment screws include a ball-tip at the end of the screw that contacts each point on the kinematic plate. The cone contact constrains all the translational degrees of freedom (x, y, z). The groove contact constrains both pitch (Ry) and roll (Rz) rotational degrees of freedom. Lastly, the flat contact constrains yaw (Rx)."
Mikhail adds that the TechSpec kinematic mounts also include useful attributes such as removable thumb caps to prevent unwanted changes to the alignment, nylon-tipped locking screws that prevent damage to optics, and finger recesses to ease the mounting of optical elements without contacting the precision optical surfaces. Typical angular tip/tilt range is ±5°, with an angular resolution (based on a 0.25 mm turn) of 0.2°, a sensitivity (based on a 1° turn) of 4 arcsec, and thermal and pointing stability of <5 and 1.3 μrad, respectively.
Standing firm against temperature cycles
"The two most important features of a kinematic mount are its stability and its alignability," says Rick Sebastian, product manager for optomechanics at Newport (Irvine, CA). Stability is a measure indicating how well the kinematic mount stays in place once it is aligned, while alignability is an indicator of how easily a mount can be adjusted to a specific position.
The most advanced and highest performing mirror mounts are made from stainless steel, according to Sebastian. Stainless steel is three times stiffer than aluminum; as a result, a mirror mount made from stainless steel will deflect one third as much as a similar mount made from aluminum, making it easier to align. In addition, stainless steel expands and contracts less than aluminum during a temperature change, which gives it better stability.
The stability of kinematic mounts is typically quantified through thermal testing, Sebastian notes. In a thermal test, a mount is secured in a chamber where the ambient temperature is cycled; during the thermal cycle, the angular position (both pitch and yaw) of the mirror in the mirror mount is monitored and recorded over time, typically with an electronic autocollimator. With the results of this test, a good estimate can be made of the mount's stability. The two key indicators of stability are drift and shift. Drift is a measure of the magnitude of the largest angular deflection during the test, while shift is a measure of how well the mount returns to its original angular position after the mount has returned to its original temperature. Stainless steel mounts exhibit low angular deflection (drift) and excellent thermal repeatability (shift).
"However, not all kinematic mounts use the same type stainless steels," says Sebastian. The thermal expansion coefficients (CTEs) of different stainless steels can vary significantly: for example, certain 400-series stainless steels have almost 40% lower CTEs than 300-series stainless steels.
The alignability of a kinematic mount is heavily dependent upon the sensitivity of the adjustment screws used, which in turn depends primarily on the thread pitch, which is typically measured in threads per inch (TPI; see Fig. 2). The TPI value is simply the number of threads counted over one inch of the adjustment screw. Note that the reciprocal of the TPI value represents the travel of the adjustment screw for exactly one rotation of its knob. Sensitivity can be calculated from TPI by assuming that the smallest manual knob rotation is 1°. When applied to a mount, the sensitivity measurement is changed from being linear to angular.Adjusters with the highest TPI count will provide the best sensitivity for a mirror mount," says Sebastian. "For many years, the best adjustment screws only had 100-TPI threads, but recently this value has more than doubled." For example, Newport's SX100 series mirror mounts use adjusters with a 254-TPI thread pitch.
Epoxy-free optics retention
Some of the more common delimiters for a kinematic mount include number and type of actuators, optic size and shape that can be housed, how the optic is retained, optomechanical mounting features, and material, explains Brett D'Alessio, lead engineer for the Polaris product line at Thorlabs (Newton, NJ). "The most common application for a kinematic mount is beam steering, but some of Thorlabs' specialized kinematic mounts were designed for other uses like aligning a retarder so that it is normal to the optical propagation direction, beam pointing, and optical-fiber alignment," he says.
In 2009, Thorlabs initiated a program to design and manufacture a product line of kinematic mounts for demanding applications that would normally require a custom-built mount, says D'Alessio, resulting in the Polaris line.
"Some of the early challenges in the program dealt with understanding how material choices affected the performance of the mount; for example, hardened steel, carbide, sapphire, and other materials were all considered for the kinematic actuator seats," notes D'Alessio. "The testing included standard concerns like durability, but it also looked at what happened when the temperature of the mount was cycled or the system was subjected to an impulse force. After being perturbed, the ability of the actuator to return to its original position is highly dependent on the hardness and smoothness of the surface." It was determined that optical-quality sapphire inserts provide the best overall performance, and thus they are standard on Polaris mounts.
Another key performance feature is the retention of the optic. Early in the program, Thorlabs consulted high-end users in industry and academia about their experience and frustrations regarding the use of kinematic optical mounts. One of the reoccurring responses was that reasonable performance required fixing optics to the mount with epoxy. This information led to an extensive effort to design and test the retention mechanism in the optical mount, an activity that is still ongoing six years later. Currently, there are two retention mechanisms found in the Polaris line, says D'Alessio. The first is a flexure lock, and the second uses a (patent pending) retaining ring and wave-spring combination. Both mechanisms allow the user to achieve the performance specifications of the mount without using adhesive to secure the mount.
The engineering challenges to create a sub-10-fs laser capable of thousands of hours of maintenance-free operation are significant, notes Peter Fendel, head of Thorlabs' Laser Division, who upgraded the mounts in the cavity of the Octavius Ti:Sapphire laser to Polaris-class optical mounts (see Fig. 3). Mode-locked laser cavities are very sensitive to misalignment, and the Thorlabs lasers need to withstand extreme temperature differences often exceeding 10°C, particularly during shipping; the laser's mounts also must be made of low-outgassing materials to prevent contamination of the cavity optics.
Flexure mounts
Another approach to achieving tip/tilt adjustment is by using a mount that is based on flexures rather than the usual cone, groove, and flat constraints of a kinematic mount (see Fig. 4). In this case, the entire mount can be machined from a single piece of metal, leaving two thin regions that serve as orthogonal hinges. This approach is taken by Siskiyou (Grants Pass, OR), which manufactures both kinematic and flexure optic mounts."Our monolithic flexures excel where drift must be minimized," says Mark Mittelstaedt, western regional sales manager at Siskiyou. "Heat flows easily through the part, and the monolithic design eliminates built-in stresses. Kinematics and flexures are available in top-adjust versions for tight layouts, with a drive mechanism (patent pending) that does not apply rotational torque to the optic mounting surface. The top-adjust design enables a smaller footprint and field accessibility." The flexure mounts are available in aluminum and nickel-plated steel.
Siskiyou also makes kinematic mounts; rather than conventional setscrew optics mounting, which can distort optics, they use mounting clips that, according to Mittelstaedt, eliminate tilt, reduce wavefront distortion, and provide a more secure mount for optical systems in challenging environments. Many Siskiyou mounts have pin pockets in the base to eliminate unwanted rotation, he adds.
Gimbals for low path-length variation
Some optical systems require extreme precision in all their mounts, but many other systems can get by with less-expensive mounts. Qioptiq (Göttingen, Germany) makes both types; the company's Lees mounts are the "premium" line, while the LINOS Adjust.X mounts are lower in cost. Because Adjust.X mounts with integrated base plates have dimensions compatible with those of the Lees mounts, they can be upgraded at any time with little trouble.
The Lees optical mounts have fine adjustment screws that are specially ground for mutual fit with the least possible backlash, counter surfaces of sapphire, and special lubricant, says Olaf Meyer is the LINOS product catalog business-line manager at Qioptiq (Göttingen, Germany). These mounts have an open-plate mount and are suitable for use in laser devices, interferometers, and complex optical-table laboratory setups, says Meyer. The Adjust.X have either an open or closed mounting plate; an application example for these mounts are laser spectrometers, Meyer notes.
"The adjustment screws for the Lees mounts are made from stainless steel in phosphor bronze bushings and are considered to have the finest resolution available today," says Meyer. "We were the first to offer sapphire hard-seat technology. These seats are so tough, they have been known to work flawlessly even when the mount has been dropped. Sapphire technology was chosen for its hardness, second only to diamond, and an optical quality polished surface finish."
Qioptiq also provides a set of mounts for special tasks; the mirror mounts are designed for applications in which space is restricted or where optics adjustment is only possible from above. One example is usage in high-power laser applications where optics alignment at or below beam level might be harmful. For these types of mounts, the adjustment screws are top-mounted, explains Meyer. To discriminate between the adjustment screws for the roll and pitch axes, the screws are color-coded.
The company also makes a gimbal mirror holder; for this mount, the surface of the mirror in the center point is always at the mirror's rotation point, avoiding translational movement of the rotation point during tip/tilt adjustments. The gimbal mount also has a 360° coarse angular translation as well as micrometer movement and fine angular translation.
"For a lubricant, we use Krytox greases which have vapor pressures of 8 x 10-8 to 6 x 10-9 Torr at 30°C, according to Du Pont, and thus are unlikely to outgas on your expensive optics," adds Meyer. "Krytox also has a high degree of chemical inertness and outstanding oxidation resistance. Therefore, the adjustment screws will maintain their original smooth feeling if used daily, monthly, or yearly."
Another company that makes gimbal mirror holders is OptoSigma (Santa Ana, CA); their two-axis 360° gimbal structures can point the reflective surface of a mirror in any direction with no limits (at least until almost grazing incidence, at which point the mirror-holder frame would start to block the beam).
Two types of fine-adjustment mechanisms can be combined with the gimbal: a fine-angle gimbal, which causes minimal optical path length variations, or a kinematic fine adjustment, which causes some variation in path length but has more stable temperature and long-term characteristics (and is thus more suitable for use in laser cavities).
Steering very large mirrors
Aerotech (Pittsburgh, PA) manufactures gimbals and other optical mounts that can provide mirror cells in excess of 600 mm in diameter; the mirror cells cells are available with a variety of shapes and attachment options to accommodate custom payloads, says Tom Markel, group leader, of Aerotech's research, aerospace, and defense group.
The gimbals are manufactured either with direct-drive brushless, slotless servomotors, or are gear-driven using brushless rotary motors. They are designed to provide 360° rotation of azimuth and elevation or, alternately, can have limited travels, depending on the application. Aerotech optical mounts use a patented sub-arcsecond resolution manual drive to position large, heavy optics or other components.
"Common applications of our gimbals include optics, laser, antenna, and sensor positioning to precise pointing angles, missile seeker test and calibration, lidar, electro-optical sensors and FLIR testing, airborne target tracking, optical testing of space-based sensors in a vacuum, and angular testing of inertial sensors such as gyros, MEMS, accelerometers, and inertial reference units," says Markel. "Common applications of our optical mounts include major fusion and high-powered laser research and development projects due to their excellent thermal stability and sub-arc-second resolution."
Aerotech AMG series gimbals are used in beam steering, target and star tracking, gyro and inertial sensor testing, and electro-optic calibration of seekers, sensors, and optics, notes Markel. "AMG gimbals use direct-drive, slotless, brushless servomotors to provide high accuracy, zero gear vibration, zero gear-wear accuracy loss, zero backlash, fast tracking, and low-maintenance elevation and azimuth motion," he adds. "The direct-drive motors result in highly stable, smooth, and accurate positioning, especially important in research and defense applications." Accuracy is to ±5 arcsec, repeatability is ±0.5 arcsec, and resolution is to 0.027 arcsec.
For More Information
Companies mentioned in this article include:
Aerotech
Pittsburgh, PA
www.aerotech.com
Edmund Optics
Barrington, NJ
www.edmundoptics.com
Newport
Irvine, CA
www.newport.com
OptoSigma
Santa Ana, CA
www.optosigma.com
Qioptiq
Göttingen, Germany
www.qioptiq.com
Siskiyou
Grants Pass, OR
www.siskiyou.com
Thorlabs
Newtown, NJ
www.thorlabs.com
FOR A COMPLETE LISTING OF COMPANIES making mounts and accessories, visit the Laser Focus World Buyers Guide (https://www.laserfocusworld.com/directory).
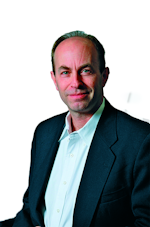
John Wallace | Senior Technical Editor (1998-2022)
John Wallace was with Laser Focus World for nearly 25 years, retiring in late June 2022. He obtained a bachelor's degree in mechanical engineering and physics at Rutgers University and a master's in optical engineering at the University of Rochester. Before becoming an editor, John worked as an engineer at RCA, Exxon, Eastman Kodak, and GCA Corporation.