OLEDs: Plasmon-coupled OLED produces white light from green phosphorescent material
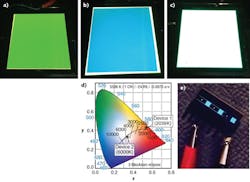
The thin-film nature of white organic light-emitting diode (OLED) lighting elements allows them to be made into large-area, glare-free lamps and luminaires shaped unlike any other, and to be embedded in walls and furniture. Two things holding OLEDs back from wider use, though, are their short lifetime and their high cost. Conventional white OLEDs are created by combining individual blue, green, and red phosphorescent emitting materials. While the green- and red-emitting materials are relatively long-lived and low in cost, today's organic blue phosphorescent materials are weak, extremely short-lived emitters that are quite expensive.
Researchers at the Industrial Technology Research Institute (ITRI; Hsinchu, Taiwan) say they have solved the blue light problem, creating emitters they call plasmon-coupled OLEDs (PCOLEDs) that use a single green light-emitting material to generate red, blue, and green light without the use of color filters. In the technique, nanostructured layers are added that create surface plasmons from the single green-emitting OLED material. In an effect based on a double-metal-layer nanostructure (DML)—a layer that does not rely on nanomaterials such as graphene, carbon nanotubes, or nanoparticles—the green light can be upshifted to produce blue light and even downshifted to produce red light as well, resulting in white light (see figure).
Conventional OLED structures focus on reducing thermal energy loss by suppressing surface plasmons. In contrast, PCOLED reverses the idea by amplifying the plasmons into visible light with the DML. As a result, two surface plasmons are coupled to produce light at the desired wavelength.
According to Ming-Shan Jeng, senior principal researcher and division director of the Intelligent Energy-saving Systems Division at ITRI, the amount of blue shift depends on the emitting materials and the device structure. In some cases, the wavelength downshift can be up to 60 nm. In this case, the shift is enough to create a blue that is blue enough to replace the conventional blue-emitting layer. Substituting plasmon-created blue and red light for conventional OLED materials not only lowers cost and increases life, it also effectively triples power efficiency, says Jeng.
As for hard figures, the researchers say that the PCOLED technology increases the life span of OLED displays and lamps to up to 300,000 hours, or by up to 20-fold. In addition, switching light-emitting materials to just one reduces materials cost to as low as 1.0–2.4% of that for existing hybrid OLED devices with blue fluorescent materials. It also leads to a simpler manufacturing process that is straightforward to integrate with conventional OLED manufacturing.
Cool and warm white
The spread in wavelengths between the blue, green, and red emitters is enough to produce good-quality white light. In fact, white light of different color temperatures from very warm white, like a candle, to very cool white, like office fluorescent bulbs (see figure). In the warm-white example, the color temperature is 2039 K, the color-rendering index (CRI) is 77, and the International Commission on Illumination (CIE) color coordinates are (0.54, 0.43). The cool-white device produces a color temperature of 6000 K and has CIE coordinates of (0.33, 0.33). (Note: a CRI of 77 is not extraordinary by any means, but is acceptable for some purposes. The result would be a color that approximates that of a candle or other low-temperature visible blackbody emitter, but does not do so precisely. Such a result is perfectly fine for a prototype—the CRI can always be refined.)
The PCOLED blue-shifting technology has been implemented in an existing production line to produce a passive-matrix OLED display. ITRI is filing for patents on the technology.
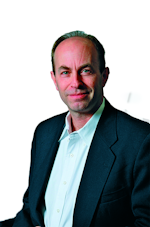
John Wallace | Senior Technical Editor (1998-2022)
John Wallace was with Laser Focus World for nearly 25 years, retiring in late June 2022. He obtained a bachelor's degree in mechanical engineering and physics at Rutgers University and a master's in optical engineering at the University of Rochester. Before becoming an editor, John worked as an engineer at RCA, Exxon, Eastman Kodak, and GCA Corporation.