Fiber Sensing: Medical fiber-optic sensors offer haptics, 3D shape sensing, and pressure sensing
The medical industry has been using various fiber-optic technologies from as early as 1957, when fiber optics were first adopted for use in endoscopes. Since then, the range of medical devices incorporating optical fibers has taken a relatively slow technological growth trajectory, with the bulk of the industry focused on endoscopy and various methods of optical power delivery for cutting, dissecting, and ablating. These technologies utilize an optical fiber's principle mechanism—the ability to guide light from one location to another.
However, optical fibers are able to offer significantly advanced functionality by utilizing their inherent sensitivity to temperature, strain, and pressure. Over the last five years, the medical industry has taken significant steps to adapt historic fiber-optic sensing methods to enable them to be used within in vivo environments.
The main area for recent technological developments driving fiber sensors into the medical industry has focused on minimally invasive surgery (MIS). These procedures are replacing highly invasive surgical procedures, such as open-heart surgery, which would normally leave a patient with significant recovery time and substantial scarring. The shorter post-MIS recovery time enables more rapid turnaround times on hospital beds, reducing the effective cost per procedure, and allows more procedures to be completed within the same duration. For the private health sector, the reduced time and cost enables a significant boost on profitability, while for the public health sector, the cost savings are critical for maintaining high levels of service against an aging population within a fixed budget.
The benefits of MIS are now well founded, encouraging surgical-tool manufacturers to invest their money in new technology developments to pioneer new MIS procedures or to further improve existing procedures. Three exciting recently developed fiber-optic technologies for MIS are focused on here: haptic feedback, 3D shape sensing, and pressure sensing.
Haptic feedback
As MIS requires the use of small tools that can be inserted into the body through a small, surgically created entry point or a natural orifice, the surgeon's hands are physically removed from the area where the procedure is taking place. The remote nature of the surgery means that the surgeon receives minimal or no sense feedback from the end of the tool.
To help surgeons, various visualization technologies are used to give surgeons some level of feedback on the procedures. Laparoscopy (otherwise known as keyhole surgery) and robotically assisted surgery typically use fiber-optic endoscopes or small digital cameras to give a direct in situ view of the tips of the tools. This gives surgeons visual feedback but leaves them without the sense of touch, making it challenging for surgeons to differentiate between the harness and textures of various tissues. In addition, otherwise simple tasks, such as tying a knot in a surgical suture, are not as precise or consistent as can be achieved by human hands. To overcome this challenge, fiber Bragg gratings (FBGs) are finding their way into surgical tools to enable the forces experienced by the tools to be translated back to the surgeon via mechanical force feedback or visualizations.
FBGs inscribed into the core of an optical fiber are highly sensitive to longitudinal strain such that, as the strain increases along an optical fiber, the central wavelength reflection response of the FBG linearly shifts towards higher wavelengths (see Fig. 1a).By utilizing multiple FBGs or manipulating the FBG structure, it is possible to obtain a spatially distributed strain profile (see Fig. 1b). Such FBGs can be applied along the length of a surgical tool to enable haptic feedback at the regions of most concern. A prime example of this is to add haptic sensing to a grasping tool, where both the grasping and spreading forces can be measured and fed back to the surgeon to give an indication of how tightly they are grasping or how much force they are applying to pry tissues apart (see Fig. 1c).
Because of the miniaturization and sterilization requirements for such tools, standard optical fibers tend not to be suitable for such applications. Specialty optical fibers with extremely low bend losses and high-temperature-resistant coatings, such as Fibercore's reduced cladding diameter, polyimide-coated SM1500(5.3/80)P fiber, allow FBGs to be written into the core of the fiber.
This type of fiber has approximately half the overall diameter as a standard telecom optical fiber, and the ability to withstand deployment states that would cause standard fibers to mechanically and optically fail. The specialty polyimide coating allows the fiber to survive multiple autoclave processes without degradation in performance, enabling the fibers to be used for both disposable and semi-disposable medical tools.
To help drive down the cost of such sensors and to improve mechanical reliability, Fibercore has been offering femtosecond-laser-written FBGs where the FBGs are inscribed into the core of the fiber without the need to remove the coating. This helps to ensure that the mechanical strength of the fiber is not compromised by the need to chemically etch away the coating, as is required by other FBG manufacturing techniques.
3D shape sensing
For robotic surgery and laparoscopy, visualization of the procedure is relatively simple through the use of fiber endoscopes or miniaturized cameras, but not all procedures have the cavity space to enable insertion of such direct visualization methods. As a result, vascular and interventional radiology (VIR) was invented to allow image-based guidance of angioplasty- and catheter-delivered stents. These procedures typically have a narrow-gauge catheter inserted into the femoral artery near the groin and, via the use of guide wires, have the catheter guided through the artery up to the heart, neck, or brain for coronary, carotid, or cerebral procedures (see Fig. 2). Once the catheter is in the desired localized area, the procedure, such as stent or balloon placement, can proceed.At present, the dominant methods of visualizing the progress of the catheter are through x-rays, CT, MRI, or ultrasound. Each of these devices presents significant drawbacks, ranging from exposure to radiation and the need to wear heavy protective clothing (x-rays) through to limitations on being able to use metallic materials during the procedure (MRI).
To address this issue, fiber-optic 3D shape sensing has been developed by a number of commercial groups to enable a dramatic reduction in the need for prolonged exposure to the visualization methods, as the optical fiber can track itself in three dimensions and thus, if laid within a catheter, can recreate the shape of the catheter. This technique relies on a mixture of FBG and fiber technology, where a very special fiber has been developed specifically for this application—this fiber is known as spun multicore fiber (see image at the top of this page).
By monitoring the FBG responses in each core, the relative strain levels between the cores can be measured. The FBGs on the inside of a bend will experience compression, while the cores on the outside will experience extension. To enable twist to be detected, the optical fiber is spun during the manufacturing process to enable a helical path of the outer cores—the FBGs on the outer cores respond differently if a twist is applied to the fiber with or against the helical path of the cores. To then calibrate for temperature and longitudinal strain variations associated with pushing the spun multicore fiber along a catheter, the central core gives a calibration point, as it is not sensitive to bending or rotation.
By combining all of these factors together, it is possible to recreate the shape of the optical fiber in three dimensions. If an initial image of the patient is taken using the existing visualization processes to obtain an internal body map, then the 3D shape sensor's computed position can be overlaid onto the body map. As the catheter is guided, the VIR imaging methods are switched off, relying solely on the optical fiber's feedback for the position.
Pressure sensing
Optical fibers can be optimized to be sensitive to the hydrostatic pressures experienced within the body. Fibercore's THE1500(5.5/80)P twin-hole fiber with an elliptical core, reduced cladding diameter, and polyimide coating (see Fig. 3a) allows FBGs to be inscribed that display a separation in the peak position of the FBG reflection on the fast and slow polarization axes.When the fiber is exposed to hydrostatic pressure, the twin holes create an asymmetric stress profile across the core of the fiber that creates a differential stress optic coefficient on the fast and slow axes (see Fig. 3b). This in turn creates birefringence, which is the key driver behind the increased (or decreased) separation of the FBG peaks. As a result, an increase in hydrostatic pressure will move the peaks further apart and a decrease in hydrostatic pressure will move them closer together.
This opens up various biomedical applications such as the precise location and measurement of pressure fluctuations within an artery that can be indicators of coronary artery disease (atherosclerosis), which causes heart attacks, and carotid artery disease, which causes strokes.
These new applications are being opened up by a mixture of economic desire and technology development. Specialty optical-fiber manufacturers continue to pioneer new fiber designs that medical-device manufacturers are able to exploit. This enables a greater diversification of medical-device product ranges and opens up new procedures that were not previously possible with minimally invasive surgery.
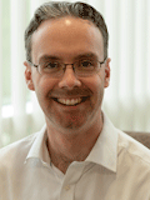
Andy Gillooly | Business Development Manager, Fibercore
Andy Gillooly is the business development manager at Fibercore (Southampton, U.K.).
In 2001, Andy graduated from the University of Birmingham, with a master’s degree in physics and received a PhD in fiber Bragg gratings (FBGs) from Aston University, England.
He spent over four years as a senior development engineer at SPI Lasers, developing FBGs and pulsed fiber lasers. After SPI, Andy joined Sharp Laboratories of Europe, responsible for the optical design and technical customer interactions for Sharp’s wafer-level camera project. Later, Andy joined Fibercore, where he is currently responsible for driving the company forward into new markets with new products; he has currently been with Fibercore for 14 years.