Advances in Imaging: Cooled infrared detectors advance the state of the art
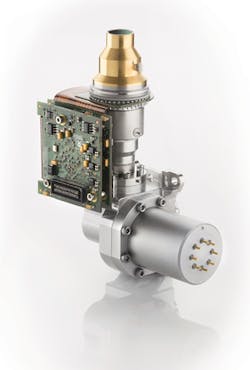
CLAIRE VALENTIN
For many decades, cooled infrared (IR) detectors have been key enablers in enhancing the capacity of defense systems to detect, recognize, and identify threats. Because they can perform at night, these sensors have been widely used for surveillance and both space-based and terrestrial defense applications.
Today, smaller-form-factor products such as handheld thermal imagers (HHTIs), unmanned aerial vehicles (UAVs), and small gimbals are driving the demand for more compact and lower-power-consumption cooled IR detectors. As a result of end-users requiring devices that are easy-to-use, have a fast cool-down time (under five minutes), exhibit excellent portability, and have low acoustic noise—with no tradeoffs in reliability and performance—manufacturers have been heavily focused on furthering technological developments.
SWaP considerations
Current-generation detectors, coolers, read-out circuits, and proximity electronics boards have all undergone innovation to meet size, weight, and power (SWaP) reductions (see Fig. 1).
The primary benefit of SWaP reductions is the obvious decrease in physical area and weight that has helped to shrink the overall footprint of portable IR detector systems by 20% in recent years. This greatly benefits the soldier for whom each additional kilogram is a challenge to carry—it frees up space in the backpack. Smaller components also ease the payloads of UAVs. Nonetheless, future IR detectors (focal-plane array + cooler + electronics) will have to offer at least another 30% reduction in volume and weight.
Secondly, lower power consumption components (<3 W) increase the battery autonomy of portable systems. This enables the soldier to carry fewer spare batteries and/or provides additional capacity to extend the mission time. As a goal, future IR detectors will need to offer at least a 25–30% reduction in power consumption.
Finally, better reliability enables missions to be carried out uninterrupted. The cost of periodic maintenance quickly becomes prohibitive. Equally important is the design of the detector, which can be optimized to both lower manufacturing costs and offer higher manufacturing yield.
Higher image resolution trend
Imaging equipment, especially in the visible band, has progressed significantly towards higher imaging resolutions coupled with high-definition (HD) image formats. Until a few years ago, 30 μm followed by 15 μm pixel pitches were seen as cutting-edge technologies on IR sensors. With new advances in 10 μm pixel pitch technology, however, cooled IR detectors can now achieve both higher image resolution and high image quality (see Fig. 2).Switching from a VGA 15 μm format to XGA or HD720 with a 10 μm pixel pitch improves resolution and range (of the official detection, recognition, and identification or DRI range) or increases the field of view. For instance, a system with f/2 optics based on a 15 μm pixel detector would benefit from pitch reduction, leading alternatively to a smaller system size or increased identification performance (see Fig. 3).
In another example, to achieve a 60% increase in the DRI performance range, a redesign of the optics encompassing a 33% increase in focal length and pupil parameters produces an image with twice as many pixels as VGA format at a focal-length number of f/2 and with 1280 × 720 format.
To achieve a 30% increase in DRI range, the same optics characteristics (same focal-length number, same pupil characteristics) would extend the field of view by 33% and would offer 1.5 times as many pixels as VGA format at f/2.
And finally, to achieve and even smaller system size, a redesign of the optics with the same field of view would provide a 33% reduction in focal length.
Large-format detectors are used for surveillance, InfraRed Search and Track (IRST) systems, recognition, and targeting pods. These tactical applications are also very sensitive to maintenance periodicity and in several cases maintenance is critical regarding uptime required for missions. Moreover, maintenance has a cost that becomes quickly prohibitive when the cooler or the vacuum has to be frequently repaired.
Improving precision-guided weapons
The precision-guided weapon is another segment application where IR sensors play an important role. With the increase in complexity of the mission and the environment, precision-guided weapons make more rigorous demands on IR imaging seekers, de facto for the IR cooled detector.
In short, IR cooled detectors should offer easy installation (aided by low weight and small size); short time to operation (rapid acquisition of first image); high reliability, as missiles are expected to work even after long storage periods; high sensitivity for improved target engagement range, even at very long distances; and low cost to justify one-time use.
Heat-seeking missile designers are required to take into account the combat situation, the mission profile, or the integration constraint to define the appropriate IR solution that fits the missile purpose. To begin with, missile-seeking sensors have to image very wide dynamic range scenes and are exposed to large shifts in the operating point because of dome heating and internal operating temperatures (stressing detector non-uniformity and narcissus corrections). For example, the 3–5 μm radiance ratio of a flare with 1000°C temperature difference with the aircraft fuselage requires an approximate 80 dB signal dynamic range.
Significant developments have been made on focal-plane arrays (FPAs). The FPA trend toward larger format and smaller pixel pitch has been occurring since the 1980s. The capability to scale down pixel size also offers a better design space for a well-sampled system and opens the door for reducing the overall SWaP and cost of the system. As FPAs progress, the field of view decreases, making image stabilization very important. Modern seeker sensors provide images with sizes ranging from small (128 × 128) in air-intercept seekers to relatively large (384 × 288 or 640 × 512) in air-to-ground seekers.
In addition to pixel format improvements, FPA frame rates have also improved. The faster the frame rate, the easier the interception of fast-moving targets. High frame rate and controllable exposure time are beneficial both for temporal noise reduction and high-speed target tracking. In general, image frame rates range from 50 to 200 Hz are adequate for the image-processing capabilities of current IR sensor systems.
As previously mentioned, size reduction is important—there are volume constraints in many heat-seeking missile applications. One of the main motivations for reducing the unit cell size in IR FPAs is to enable smaller form-factor cameras. The combination of smaller pixels and relatively small numbers of pixel elements (384 × 288, for example) is generally preferred, as these parameters allow the sensor to achieve lower cost, size, and weight.
Missile seeker development drivers
Most missile-seeking systems require a short time to operation. Guided bombs or cruise missiles with long flight durations soften the requirements on cool-down time (in the range of 15–120 s). The time to impact for targets say 5 km out is relatively short—just a little more than 11 s. As a consequence, the short-range weapons (man-portable air defense systems or MANPADS) require a shorter cool-down time (in the range of 10 s), as they allow little margin of error to effectively counter the threat.
In some cases, the seeker is cooled a long time before being fired as it also functions as a sensor providing tactical information to the flight crew. In that case, the cool-down requirement can be softened.
Seekers must also exhibit high reliability for one-time use. The severe environments for seekers demand that IR detectors survive and operate under gravitational forces of several-thousand G in acceleration and severe shock in any axis. Temperature ranges vary from -46° up to nearly 100°C, and tremendous vibrations are experienced during the missile's thrust. Often transported outside a fast-moving airplane or on a ship or vehicle in motion, even the storage and transportation environments can be severe.
IR shortwave market trends
The last major trend in the IR world is the development of the shortwave market. Ranging from 0.9 to 1.7 μm, the short-wavelength infrared (SWIR) spectral band is an attractive domain because of its intrinsic properties: since it is close to visible wavelengths, the interpretation of SWIR images is easier for users in the field.
In addition, complementary information can be extracted from the SWIR band and bring significant added value in several applications, including night vision and active imaging for defense and security, Earth observation for space-based imaging, automotive safety details for the transportation industry, and nondestructive process control for industrial applications.
These SWIR developments are driven by demand from defense applications in which the short-wavelength information is added to thermal imaging profiles to improve the identification features of the sensor-especially in bad weather conditions like fog. Commercial applications such as machine vision, laser beam analysis, and spectroscopy also benefit from SWIR information.
Claire Valentin is director of marketing at Sofradir, Palaiseau, France; e-mail: [email protected]; www.sofradir.com.