Integrated Optics: Circular single-mode polymer waveguides are created using the Mosquito method
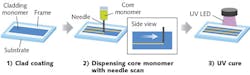
High-bandwidth single-mode fibers pair well with the single-mode nature of silicon (Si) photonic circuits, providing fast connections between photonics-enabled chips at datacenters. However, connecting these fibers and photonic chips would be made easier by some sort of easy-to-fabricate type of single-mode optical waveguide.
Polymer waveguides, which can be fabricated a number of different ways, including photolithography and ultraviolet (UV) imprinting, could serve this purpose. However, although nominally single-mode polymer waveguides can be created using the above methods, fabricating circular single-mode polymer waveguides is more difficult.
Engineers at Keio University and Huawei Technologies Japan (both in Yokohama, Japan) are now using the so-called Mosquito method to create high-quality circular single-mode waveguides in polymer that are intended for use at 1310 and 1550 nm wavelengths.1 First developed to fabricate multimode polymer waveguides, the Mosquito method is named after the way it forms the waveguide—with a needle.
Starting with a coating of a thick monomer liquid on a substrate, the needle of a syringe filled with a different, higher-refractive-index liquid monomer is inserted into the coating and moved so that a thread of the second monomer is deposited in the first monomer at a distance underneath the surface of the coating (see figure). The combined structure is cured under UV light. The researchers say the whole process takes 15 minutes or less to fabricate a 5-cm-long, 12-channel single-mode polymer waveguide structure.
Single-mode via the Mosquito method
The researchers used two different versions of a silicate-based organic-inorganic hybrid resin for the core and cladding-the refractive-index difference between the two versions was about 0.6%. The resin, called Sunconnect and developed at Nissan Chemical (Tokyo, Japan), is thermally stable enough to withstand even the heat from solder reflow processes.
To create single-mode rather than the original multimode waveguides using the Mosquito method, the researchers decreased the dispensing pressure for the core monomer, increased the needle-scan velocity, and used a thinner needle. Data showed that the core diameter was inversely proportional to the square root of the needle-scan velocity. With a high-enough needle-scan speed, core diameters as small as 5 μm could be created. The researchers settled on a 40 mm/s scan speed, producing a core diameter of 7.9 μm—the 12 waveguides were spaced 254 μm apart.
Near-field intensity profiles of the waveguides closely fit a Gaussian profile with mode-field diameters (MFDs) of 8.27 and 9.47 μm at 1310 and 1550 nm wavelengths, respectively. For comparison, the MFDs for a standard single-mode fiber were also measured, and were 6.41 and 7.36 μm for 1310 and 1550 nm wavelengths.
Propagation losses for the fabricated waveguides were also measured using the cut-back method, in which ever-shorter lengths of the same waveguide are characterized and the loss then calculated. The propagation losses were determined to be 0.29 and 0.45 dB/cm at 1310 and 1550 nm wavelengths, which are very low and show that the core-cladding boundary is smooth, minimizing scatter.
Insertion and coupling losses were measured using a standard single-mode fiber coupled into the waveguide without using any index-matching fluid. The insertion loss (which takes into account the coupling losses and the loss within the waveguide itself) was 2.52 and 4.03 dB at 1310 nm and 1550 nm, respectively, while the coupling loss was estimated to be 0.5 dB at 1310 nm per end, including the Fresnel reflection loss. Fiber-to-waveguide misalignment tolerances for a 0.5 dB loss were measured to be about ±1.5 and ±2.0 μm at 1310 nm and 1550 nm, respectively.
The researchers also coupled the 12-channel waveguide array to a 1 × 16 channel optical splitter with a 127 μm pitch-half that of the 12-channel array, meaning that only eight of the connections could be made because of the geometry of the devices. The eight connected channels showed high intensity.
Finally, narrow-pitch versions of the 5-cm-long polymer-waveguide arrays were evaluated for crosstalk. While a 30 μm pitch produced a lower than -30 dB crosstalk, a 20 μm pitch resulted in a high crosstalk on the order of -10 dB, probably because of mode-coupling.
REFERENCE
1. K. Yasuhara et al., Opt. Express (2017); https://doi.org/10.1364/oe.25.008524.
About the Author
John Wallace
Senior Technical Editor (1998-2022)
John Wallace was with Laser Focus World for nearly 25 years, retiring in late June 2022. He obtained a bachelor's degree in mechanical engineering and physics at Rutgers University and a master's in optical engineering at the University of Rochester. Before becoming an editor, John worked as an engineer at RCA, Exxon, Eastman Kodak, and GCA Corporation.