X-ray Optics: Normal-incidence multilayer Laue lens focuses hard x-rays
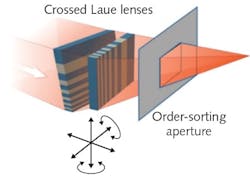
Because of their short wavelengths (on the order of 1 to 0.1 nm) and their high sensitivity to structural, elemental, and chemical differences, hard x-rays can be used to probe complicated nanoscopic structures, such as those inside biological cells, with great precision and often at great speed, "freezing" the biological processes being imaged.
But because such x-rays cannot be focused via conventional optical approaches, unusual techniques must be used—for example, grazing-incidence mirrors. However, grazing-incidence optics are necessarily large—sometimes a meter or more long just to focus an x-ray beam that is much less than a millimeter in width.
A different approach, in which a flat or wedged plate made of two different materials formed into cross-sectional layers of graded width, can serve as a compact, near-normal-incidence one-dimensional diffractive lens similar to a 1D Fresnel zone plate. Two of these devices, which are called multilayer Laue lenses (MLLs), can be crossed to create a point (two-dimensional) focus (see figure), in the same way that two crossed refractive cylinder lenses can form a point focus for visible light.
However, rotationally aligning two crossed MLLs to each other well enough to eliminate astigmatism is difficult. For example, if two crossed MLLs are designed to produce a 10 nm focal spot, an error <0.01° is required. And, because both MLLs must be bonded onto a supporting substrate between them, two identical MLLs are displaced axially from each other enough to cause strong astigmatism.
Making, bonding, and testing MLLs
Researchers at the National Synchrotron Light Source II at Brookhaven National Laboratory (Upton, NY) have solved both of these problems, creating a bonded focusing MLL device that creates a probe focal spot of about 17 × 38 nm for x-rays with a 9.317 keV energy (0.133 nm wavelength).1 The simpler problem that occurred because of the use of two identical MLLs was solved by creating two MLLs with slightly different focal lengths. The rotational-alignment problem was handled via a setup using a reference prism with perfect perpendicular surfaces, allowing alignment to 0.03° (although <0.01° would have been ideal).
An important part of the process was the insertion during fabrication of the MLLs of occasional so-called "marker" layers, which were triple the nominal zone width and were positionally resolved to the nanometer level in scanning-electron microscope (SEM) images of the MLLs. This enabled the expected focusing performance to be calculated. The results indicated that the best focus size would be 13 and 20 nm for the two MLLs, which were 53 and 43 μm in aperture size, respectively.
Reactive ion etching and focused ion-beam milling were used to machine the two MLLs down to a 4 μm thickness and a width of 100 μm. Based on the SEM measurement and the resultant calculations, the two MLLs needed to be 0.724 mm apart axially to produce an astigmatism-free focus—bonding to a spacer resulted in an actual axial gap of 0.715 mm. The Brookhaven scientists, having an x-ray synchrotron on hand as the light source, compensated for the error in axial distance by slightly changing the wavelength of the x-rays.
The MLL assembly was mounted to a mechanical manipulator with five degrees of freedom and positioned in the x-ray beam, which had a rectangular profile defined by an upstream adjustable slit that was set to match the width of the MLL. A gold order-setting aperture was used to block both the zero-order beam exiting the MLL device and the unwanted higher-order beams diffracted from the MLLs. The focusing efficiency of the MLL device was 7.3%.
Using a gold Siemans-star resolution pattern with pattern sizes ranging from 100 to 500 nm, the researchers characterized the performance of the MLL. They then used ptychography, a computationally intensive imaging method that allows focusing after acquisition of the data, to achieve a resolution of 13 × 13 nm. They also discovered fabrication problems, such as the fact that the MLL actually bent during bonding, which they can correct in future versions of this device.
REFERENCE
1. X. Huang et al., Opt. Express (2017); https://doi.org/10.1364/oe.25.008698.
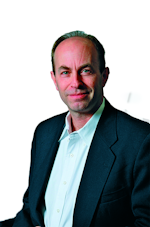
John Wallace | Senior Technical Editor (1998-2022)
John Wallace was with Laser Focus World for nearly 25 years, retiring in late June 2022. He obtained a bachelor's degree in mechanical engineering and physics at Rutgers University and a master's in optical engineering at the University of Rochester. Before becoming an editor, John worked as an engineer at RCA, Exxon, Eastman Kodak, and GCA Corporation.