Ceramic core carbon dioxide lasers serve a wide range of industries
Over the past 40 years, carbon dioxide (CO2) lasers have evolved from glass-tube, high-voltage designs to metal-tube RF electrode technology. Despite this evolution, all designs are still affected by laser gas mixture degradation, because metal electrodes shed atoms and contaminate the laser gas and/or the helium leaks through porous seals or welds. The resulting power loss is a concern that requires laser gas refilling or laser replacement. This problem has been addressed by a design, patented by Iradion Laser (Uxbridge, MA), that hermetically seals the CO2 laser gas mixture in an aluminum-oxide ceramic core or chamber (see Fig. 1). RF electrodes sandwich the ceramic core, thus exciting the CO2 laser gas externally and eliminating any possible contamination; also, the helium cannot escape.
Figure 2 illustrates the difference between new and older technology. The CeramiCore technology seals CO2 laser gas in a ceramic core with electrodes on the outside, while traditional lasers place CO2 laser gas and electrodes in a metal or glass chamber prone to gas contamination and seal leakage.Other benefits of the ceramic core design include faster pulse rise/fall times (<75 µsec), improved power stability from 2% of rated wattage to maximum power, excellent beam quality (M2 < 1.2), and no laser gas refills. The latter benefit is so important that Iradion provides a laser gas mixture guarantee: in the event of laser gas degradation, a free gas refill of the company’s laser is provided for up to 7 years after shipment date.
It should be noted that CO2 lasers typically produce 10.6 µm wavelengths that are excellent for processing plastics, polymers, and organic materials—a reason for their newfound popularity. Fiber lasers, on the other hand, produce a shorter 1 µm wavelength that is very suitable for metals, but not as useful for non-metals.
Machine builders and system integrators that use CO2, fiber, and other laser types have realized the operational benefits of Iradion’s lasers, as well as their performance and reliability. Let’s examine a few unique product lines and application.
PerfoTec (Woerden, Netherlands)
The PerfoTec laser system extends freshness of fresh produce by optimizing the permeability of the packaging by using a fast respiration meter that quickly measures the optimum respiration rate of fresh fruits and vegetables. Then, software calculates the required film permeability. By precise control of air circulation, the quality and shelf life of fresh produce is guaranteed. This is achieved by microperforating the packaging, using Iradion CO2 lasers, to produce very small-diameter holes consistent in size and numbers to create active modified atmosphere packaging for fruits, vegetables, and even flowers. Figure 3 shows a PerfoTec laser system that performs ‘on the fly’ microperforations. A patented closed-loop-feedback-camera-system inspects each hole, and if necessary, the lasers are automatically adjusted ‘on the fly’ to compensate for packaging film thickening.Martijn de Bruin, PerfoTec president, commented, “The Iradion lasers meet our demanding microperforation requirements and have demonstrated the performance and reliability standards that our customers expect. Eliminating the need for laser gas refills is very significant.”
Trotec Laser (Marchtrenk, Austria)
Trotec, a manufacturer of cutting, engraving, and marking workstations, has expanded its use of CeramiCore CO2 laser tubes with the recent release of its updated Speedy 100 and 300 laser models with Infinity 60–120 W lasers as well as Eternity 30 and 40 W lasers. Speedy models were already the fastest flatbed CO2 lasers on the market, and with the updates, are all now equipped with OptiMotion motion control to boost productivity by maximizing cutting speed at highest cutting quality. The Speedy CO2, fiber, and dual-source lasers can mark, cut, and engrave a wide array of materials, and are available with several options, accessories, and bed sizes from 24 × 12 in. up to 40 × 24 in. Figure 4 shows some of Trotec’s product lines.Trotec’s CEO, Andreas Penz, summarized the company’s focus: “Technology makes the difference, so we always look for the leading-edge advantage. We searched for the right CO2 laser and found that ceramic core technology represents the new industry standard that provides the high performance, excellent power stability, and fast rise/fall times to enhance engraving speeds as well as long-life reliability.”
Laser Engineering (Nashville, TN)
Laser Engineering, a pioneer in applying CO2 laser technology to develop solutions for surgical medical challenges, developed one of the first CO2 laser scalpel instruments using a CO2 glass laser tube over 30 years ago. Another innovative instrument was the CO2 metal laser tube workstation used to perforate damaged heart tissue, allowing oxygenated blood to enhance healing and helping over 5000 patients improve cardiac performance.
In 2021, the company released the Aurora MD CO2 isotope laser with dual beam delivery: the articulated arm and the Ultralase Hollow Waveguide (see Fig. 5). Iradion supported Laser Engineering’s new product line by developing a special Eternity 40 W, 11.2 µm wavelength to enhance the performance of surgical procedures. The laser beam can be effectively delivered through the flexible Ultralase Hollow Waveguide to precision, narrow surgical tools for gynecological and endoscopic procedures or through the counterbalance articulated arm for typical procedures.Brian Sanders, Laser Engineering sales manager, explained how Iradion assisted the new product development: “Iradion management understood the challenges of the project, and dedicated engineering and testing to meet our specifications. The ceramic core CO2 technology provides the performance and reliability that the medical industry demands.”
Nexa3D (Ventura, CA)
Nexa3D’s QLS 350 represents a breakthrough in thermoplastic additive manufacturing by offering one of the largest polymer powder bed work zones—350 × 350 × 400 mm. It harnesses the precision beam quality of four Iradion Infinity 100 W ceramic core CO2 lasers and uses four galvo scanners to achieve its exceptional performance capabilities.
As a result, the QLS 350 can achieve 4X the print speed of traditional laser sintering technologies, delivering a polymer-based production alternative to injection molding.
Designed for “lights-out” 24/7 operation and equipped with movable powder build units, the QLS 350 facilitates continuous precision part production of a wide range of selective laser sintering materials (see Fig. 6). The explosive growth of new applications using glass, plastics, fiber, polymer, and other exotic materials has impacted many industries, from medical to aerospace to automotive.Tomasz Cieszyński, Nexa3D director of technology, explains, “The ceramic core CO2 technology proved to be an excellent alternative to the traditional metal tube lasers, offering unique performance features as well as addressing the issue of long-term CO2 laser gas integrity of older technologies.”
Vytek Laser Systems (Fitchburg, MA)
Since 1989, Vytek Laser Systems has been manufacturing laser cutting, engraving, and marking equipment with easy-to-use software for a wide variety of markets and applications. Recently, a customer requested the ability to link to their online ordering system, record a SKU number, map it to a cut file, and then process the material using a roll/pass-through option. For this stencil cutting application, an Iradion 250 W laser was integrated into a modified 3-axis galvo CO2Cab system (see Fig. 7). The stencil material is fed from side to side using a material support system. The work area is a 600 × 600 mm scan field with a downdraft fume extraction system to remove fumes from an interchangeable aluminum blade table or a honeycomb table.Vytek’s president, Dirk Burrowes, remarked, “Iradion has become one of our most reliable laser suppliers providing CO2 lasers with excellent performance and reliability, but also on-time shipments and rapid response to technical requests.”
ACKNOWLEDGMENTS
CeramiCore and OptiMotion are trademarks of Trotec Laser.
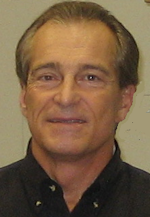
Robert Kloczkowski | Sales and marketing manager, Iradion Laser
Robert Kloczkowski, Iradion Laser (Uxbridge, MA) sales and marketing manager, has worked in the laser industry for over 30 years. After graduating from Boston University with a MS in Physics, he worked for Cincinnati Incorporated, a machine tool builder, for 15 years as a sales manager, and then as a laser product manager. This was followed by a laser product manager position at Rofin-Sinar, selling a variety of laser sources including CO2, fiber, picosecond, and femtosecond wavelengths, as well as systems and workstations. After Coherent acquired Rofin-Sinar in 2017, he moved to Iradion Laser to promote its patented ceramic-core CO2 laser technology to OEM system builders and integrators in North and South America.