Refractory metal powders for laser additive manufacturing
6K Additive (a division of 6K; North Andover, MA), which produces sustainable advanced materials for additive manufacturing and energy storage, has introduced refractory metal powders for laser additive manufacturing. Materials such as tungsten, rhenium, tungsten/rhenium, and niobium-based powders used for defense, aerospace, and medical industries are sought-after materials for high-temperature, high-strength applications.
6K’s UniMelt microwave plasma process manufactures production-scale volumes of tungsten, tungsten/rhenium, tantalum, niobium, and molybdenum. For example, Quadrus Corporation (Huntsville, AL) recently used 6K Additive’s expert services for making spherical tungsten-rhenium to produce a non-eroding throat insert for a solid rocket motor nozzle. Tungsten/rhenium powder spheroidized by 6K processed exceptionally well in the company’s selective laser melting machines.
At 6K Additive’s 45,000-sq-ft. powder production facility in Burgettstown, PA, two UniMelt microwave plasma systems are installed, with two more scheduled for installation in Q4 2021. The company will also begin construction to expand the powder manufacturing building in Q4 2021 to add space for six additional systems. Installation of the additional systems will begin in Q1 2022.
6K Additive currently produces, as commercially available powders, Ti6Al4V (Grade 5 and Grade 23), SS316L, and nickel superalloys Ni718 and Ni62.
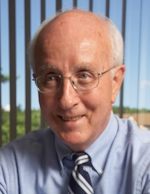
David Belforte | Contributing Editor
David Belforte (1932-2023) was an internationally recognized authority on industrial laser materials processing and had been actively involved in this technology for more than 50 years. His consulting business, Belforte Associates, served clients interested in advanced manufacturing applications. David held degrees in Chemistry and Production Technology from Northeastern University (Boston, MA). As a researcher, he conducted basic studies in material synthesis for high-temperature applications and held increasingly important positions with companies involved with high-technology materials processing. He co-founded a company that introduced several firsts in advanced welding technology and equipment. David's career in lasers started with the commercialization of the first industrial solid-state laser and a compact CO2 laser for sheet-metal cutting. For several years, he led the development of very high power CO2 lasers for welding and surface treating applications. In addition to consulting, David was the Founder and Editor-in-Chief of Industrial Laser Solutions magazine (1986-2022) and contributed to other laser publications, including Laser Focus World. He retired from Laser Focus World in late June 2022.