2D and 3D SPAD imagers demonstrated in EU MiSPiA project
Milan, Italy--A three-year program coordinated by Politecnico di Milano, Dipartimento di Elettronica e Informazione, Italy, launched in June 2010 and supported by a $3.5 million dollar grant from the European Union Seventh Framework Program (FP7), the MiSPiA Project or "Microelectronic Single-Photon 3D Imaging Arrays for low-light high-speed Safety and Security Applications" has resulted in the successful demonstration of two- and three-dimensional (2D and 3D) single-photon avalanche diode (SPAD) technology.
The MiSPiA project involves seven partners (Universities, Research Centers, and SMEs) from four different countries, working on SPAD technology, SPAD arrays and single-photon instrumentation, CMOS sensor fabrication and advanced SOI processes, design and fabrication of microlens arrays, development of time-correlated single-photon counting detection modules and imaging cameras, and safety applications in the automotive field and security surveillance of sensitive areas.
The MiSPiA project goal is to deploy an enabling technology for those many social needs requiring the acquisition of 3D scenes at ultra-low light levels, at video or even higher frame rates, and also with centimeter distance resolution. Commercial cameras cannot simultaneously offer high speed and ultra-high sensitivity; CCDs reach sensitivity close to single-photon levels, but but require cooling and long integration times (very low frame rates); and CMOS active-pixel sensor (APS) imagers provide video-rate images, but with relatively limited detection efficiency, thus requiring bright illumination scenes.
In the first 18 months of the MiSPiA project, working SPAD detectors with outstanding performance have been demonstrated. At the beginning of the project, the requirements and specifications were defined for both 3D ranging imagers (based on direct and indirect time-of-flight (TOF) techniques) and for 2D imagers (based on photon counting). The characteristics and specifications of individual SPAD detectors, smart pixels, array chips, and full imagers were defined based on the accurate exploitation of a cost-effective standard CMOS fabrication technology.
The design of test structures for SPADs, smart-pixels, and mini-arrays for 2D imaging was completed by the end of the first year of the project. Different smart pixels for TOF-based 3D ranging imagers were proposed and implemented, and different light sources (highly efficient LEDs and pulsed lasers) were considered and evaluated for assessing the best candidates for the safety 3D short-range (20 m) automotive ranging applications and the security 3D long-range (1 km) applications. Work is ongoing to complete the full specifications.
SOURCE: MiSPiA; www.mispia.eu
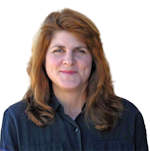
Gail Overton | Senior Editor (2004-2020)
Gail has more than 30 years of engineering, marketing, product management, and editorial experience in the photonics and optical communications industry. Before joining the staff at Laser Focus World in 2004, she held many product management and product marketing roles in the fiber-optics industry, most notably at Hughes (El Segundo, CA), GTE Labs (Waltham, MA), Corning (Corning, NY), Photon Kinetics (Beaverton, OR), and Newport Corporation (Irvine, CA). During her marketing career, Gail published articles in WDM Solutions and Sensors magazine and traveled internationally to conduct product and sales training. Gail received her BS degree in physics, with an emphasis in optics, from San Diego State University in San Diego, CA in May 1986.