European SMARTFIBER project produces miniaturized fiber-optical monitoring system that can be embedded in composite material
Nanoelectronics research center imec (Leuven, Belgium), Ghent University (Ghent, Belgium), and their partners in the European FP7 project SMARTFIBER have demonstrated the first miniaturized fiber-optical sensor system than can be fully embedded in a composite material. The result will be "smart" composites that enable continued and automatic monitoring of the structural health of the composite material in, for example, tidal blades, wind turbines, airplanes, and marine structures (masts, antennas, yacht hulls, navy ships, and propellers).
The sensor system was assembled by Optocap (West Lothian, Scotland) on an electronic board designed by Xenics (Leuven). The optical subsystem is made of a silicon-photonic integrated circuit developed by imec, along with photodiodes and readout ICs provided by Xenics. Fraunhofer IIS (Erlangen, Germany) was responsible for the wireless interface, which provides power to the embedded system and at the same time reads out the acquired data at high speed.
After connecting the system to an optical-fiber sensor chain manufactured by FBGS international (Jena, Germany and Geel, Belgium), the assemblage was cast in an epoxy shape specifically designed by Ghent University to minimize the impact on the composite material. Finally, together with the attached fiber-sensor chain, the device was embedded in the blade of a tidal turbine made by Airborne Marine (The Hague, The Netherlands).
The silicon-photonic integrated circuit, which has an arrayed waveguide grating (AWG) acting as a spectrometer, forms the core of the sensor system and allows interrogating the fiber Bragg grating (FBG) sensors connected to it with high accuracy. The advantages of these FBG sensors compared to other strain monitoring techniques (such as electrical strain gauges) are their compactness, light weight, immunity to electromagnetic interference (EMI), high resistance to corrosion, high temperature operation, and good multiplexing capability.
The FBG sensors were designed to minimally impact the strength of the composite material. Automatic techniques were developed to embed them in the composite; this, together with the use of silicon-based microfabrication processes on a well-established industrial infrastructure, are intended to substantially lower the cost of embedded strain sensors.
Source: http://www2.imec.be/be_en/press/imec-news/imec-smartfiber-fp7-photonic-read-out-demonstrator.html
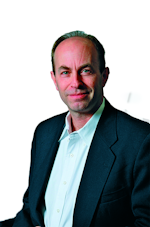
John Wallace | Senior Technical Editor (1998-2022)
John Wallace was with Laser Focus World for nearly 25 years, retiring in late June 2022. He obtained a bachelor's degree in mechanical engineering and physics at Rutgers University and a master's in optical engineering at the University of Rochester. Before becoming an editor, John worked as an engineer at RCA, Exxon, Eastman Kodak, and GCA Corporation.