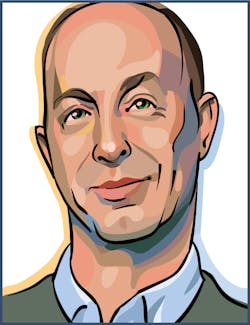
Metalenses—optical elements made of metamaterials rather than from traditional refractive, reflective, or diffractive materials and configurations—have, since their inception, been known as inefficient, poorly performing, and difficult-to-make laboratory devices that have interesting properties but that just don't seem to make the grade as part of a practical optical system. A metamaterial is a structure consisting of arrays of subwavelength dielectric and/or metal structures, usually with a subwavelength period as well. Can you imagine anything less suited for use by manufacturers who are used to traditional optics and optical fabrication techniques?
Multifunctional
However, these interesting properties of meta-optics include ultrathin and lightweight configurations, as well as optical properties achievable in a single metamaterial optical element that would ordinarily require a complicated optical train to duplicate. These properties are good reason to keep pushing the development of meta-optics.
This year, researchers at Harvard University's School of Engineering and Applied Sciences (SEAS; Cambridge, MA) and the University of Waterloo (Waterloo, ON, Canada) have reported the design, fabrication, and testing of a number of metalenses that have good efficiency and imaging properties, as well as novel optical characteristics. (By the way, this Harvard SEAS optics lab is headed by Federico Capasso, one of the inventors of the quantum-cascade laser.)
Laser Focus World reported briefly on one of these developments in our May 2016 issue in a Newsbreak titled "Planar visible-region metalens is practical enough for real use in microscopy." These metalenses, which like many metalenses are monochromatic and thus suited for use with lasers, have a very high numerical aperture (NA) of 0.8 and are experimentally diffraction limited at their design wavelengths of 405, 532, and 660 nm, and have high efficiencies also -- 86%, 73%, and 66% at their respective wavelengths.
Now, I'd like to bring you up to speed on another variation of this type of metalens produced by the SEAS lab and the University of Waterloo. This version has a much lower NA of 0.05 and produces high-quality monochromatic images such as these of a Chrysina gloriosa beetle (see below).1Chiral light separation
But why are there two somewhat different images of the same beetle? The answer is that the metalens actually produces two spatially separated images of the same object by separating the incoming light into its left- and right-circularly polarizad components. So, without the need for any additional polarizing elements, the result is an imaging polarization analysis of the beetle's exoskeleton based on the chiral separation of light.
A scanning-electron micrograph (SEM) of the metalens gives us a clue how it works (see below). The SEM reveals a subwavelength array of titanium oxide nanofins, with alternating rows having alternating nanofin-orientation patterns. All the rows that are similar to the one colored blue focus right-circularly polarized light, while all the rows similar to the green-tinted row focus left-circularly polarized light (to a different spatial location at the image plane).Although the metalens produces sharp images only under monochromatic light, it does produce these sharp images at any wavelength between 450 and 650 nm; only refocusing is required (the spatial separation of the two images also changes a bit).
These metalenses are real optics, already suitable for some experimental optical systems. As development proceeds, I have no doubt we'll be seeing much more of these meta-optics.
Source: http://www.seas.harvard.edu/news/2016/06/ultrathin-flat-lens-resolves-chirality-and-color
REFERENCE:
1. M. Khorasaninejad et al., Nano Letters (2016); doi: 10.1021/acs.nanolett.6b01897
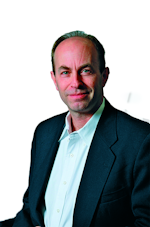
John Wallace | Senior Technical Editor (1998-2022)
John Wallace was with Laser Focus World for nearly 25 years, retiring in late June 2022. He obtained a bachelor's degree in mechanical engineering and physics at Rutgers University and a master's in optical engineering at the University of Rochester. Before becoming an editor, John worked as an engineer at RCA, Exxon, Eastman Kodak, and GCA Corporation.