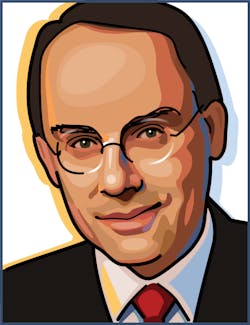
On April 26 and 27, the 4th UKP Workshop: Ultrafast Laser Technology united experts from the academic and industrial ultrafast laser community in Aachen, Germany. The workshop reflects the trends in this exciting field from basic research up to fully automated systems for manufacturing.
While everyone agrees on the benefits of ultrafast (aka, ultra-short pulse) lasers, namely an extremely precise ablation without debris, there is much debate at the moment how the new generation of high power systems with up to 100 W can be used to drive productivity.
It’s fast and precise but not cold!
Beside productivity, some findings from the academic research were particularly exciting this year: Beat Neuenschwander from Bern University of Applied Science (Switzerland) and Thomas Graf from Stuttgart University (Germany) showed experimental and theoretical evidence that the concept of cold ablation does not hold for high power ultrafast laser processing of metals.In fact, heat is deposited and transferred to adjacent material from high repetition rate ultrafast pulses. Neuenschwander showed a lot of interesting experimental findings beyond that. For example, he found a maximum ablation efficiency for several metallic materials depending on the laser fluence.
Both scientists agreed on the fact, that thermal effects are critical for ultrafast laser ablation in industrial applications. To retain benefits such as a very limited melt zone or debris free processing, the laser parameters have to be selected carefully. Proper laser parameters have been investigated for materials such as copper or steel, but a complete description of the underlying physics and material science is currently not available.
How to get the horse power on the road?
So far ultrafast lasers have occupied some niche markets. Productivity is now seen as the key to larger markets. Today, big sources are available; the main obstacle is seen in the process and system technology for using such power on larger areas.
Two ways for enhanced productivity have been presented: Fast scanners with more than 1,000 m/s (from Scanlab) and multi-beam solutions where patterns with up to 600 beams are generated out of one beam (from Fraunhofer ILT). Both approaches are promising, but still under evaluation.Another important trend is the use of special fibers for the flexible distribution of ultrafast laser beams. PT Photonic Tools presented photonic crystal fibers with a damage threshold of up to 1 GW/cm². Additional effects such as beam shortening or frequency conversion will be available from gas-filled fibers.
Trends and applications
Two sessions were devoted to industrial applications. Fully automated systems for applications in semiconductor and glass processing were presented. One had two heads for more productivity (from Manz AG), another one combined pico- and nanosecond lasers in one machine (from GF Machining Solutions). New applications are expected in texturing, structuring, and engraving on large surfaces for automotive, ICT, and packaging.
Still, a simple machine tool is missing, as workshop organizer Arnold Gillner from Fraunhofer ILT pointed out in the end. It will be worth watching for the next UKP workshop on April 10-11, 2019, since one major outcome of this year’s workshop is that: The industrial application of ultrafast laser is just at the beginning.
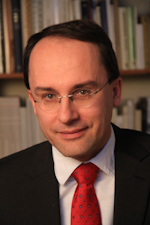
Andreas Thoss | Contributing Editor, Germany
Andreas Thoss is the Managing Director of THOSS Media (Berlin) and has many years of experience in photonics-related research, publishing, marketing, and public relations. He worked with John Wiley & Sons until 2010, when he founded THOSS Media. In 2012, he founded the scientific journal Advanced Optical Technologies. His university research focused on ultrashort and ultra-intense laser pulses, and he holds several patents.