Industrial Lasers: Beam shaping enables new ultrafast laser manufacturing applications
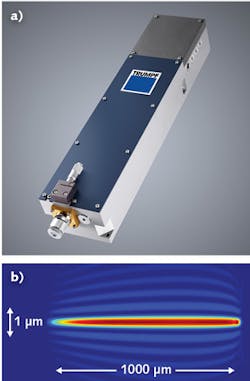
YVONNE GUERTLER and MAX KAHMANN
For many years, laser beam shaping has enabled users to achieve optimized process results as well as manage challenging applications. The latest advancements in industrial lasers and processing optics have taken this a step further, as users are able to adapt the beam shape to meet specific application requirements in a very flexible way. Over the past years, TRUMPF has developed an understanding of how to create any beam profiles at the work piece, which offers the best preconditions for optimized material processing.
The beam shaping technology is based on optimized wave optics design and improved fabrication methods for transmissive components made from fused silica. It can be used with ultrafast (a.k.a. ultrashort) pulse lasers as well as multi-kilowatt continuous-wave (CW) lasers. And it produces high efficiency and power handling capability while facilitating flexible beam shaping approaches for different laser applications, from fundamental to multi-mode and ultrafast to continuous emission within a wide spectral range.
The beam shape can be adapted in all three dimensions (x-y-z direction), which allows maximum flexibility. Besides an adapted intensity profile, multi-spot geometries can be produced. The approach is cost-efficient because standard laser equipment can be used, which means that a standard laser source and, in the case of CW lasers, a standard fiber can be used without any special adaptations necessary.
Using this beam shaping technology, we have developed new and optimized processes. Two of the most recent application developments include cutting glass and synthetic sapphire with ultrashort pulse lasers, and enhanced brazing capabilities of hot-dipped, zinc-coated steel for automotive applications. Both developments lead to more efficient and flexible production processes, and open the door to new market opportunities. They also indicate the potential of beam shaping techniques since they can be applied to both single-mode laser sources and multi-mode sources.
Separating synthetic sapphire and glass
Since glass is transparent to light in the visible and near-infrared spectral range, it might seem illogical to process it using a laser at a wavelength within this range of transmission. However, when using ultrafast pulsed laser light in the picosecond or femtosecond range, the light does not simply pass through the material. Instead, the massive spatial and temporal density of the photons in the pulse facilitates a nonlinear, multiphoton absorption process that generates free electrons. Subsequently, these free electrons absorb additional photons. The modified absorption mechanism in these transparent materials makes it possible to use laser beams to process synthetic sapphire and glass.
The success of the process is based on material modification. Instead of working directly through the material pulse by pulse as with ablation, ultrafast pulsed laser beams are focused inside the glass, where they modify a narrow zone along the desired cleavage line. The material fractures along this tailored narrow laser-generated weakness within the modification zone. The surface remains very smooth and accurate to a hundredth of a millimeter, regardless of whether it is straight or curved.
This technique was recently developed to cleave thin, hardened glass such as that used as the front cover glass in smartphone displays, and is achievable at a speed of 1 m/s with the TRUMPF TOP Cleave optics, with beam shaping applied. The intensity of the laser light is uniformly distributed along the propagation axis of the beam (z-direction). In this way, the focus is stretched in length and the beam spot becomes a focus line exhibiting an extreme aspect ratio of >1000:1. The laser pulses no longer scan the glass level by level, but instead modify—in a single pass—the complete interior separation surface (see Fig. 1).
Depending on the pulse energy and the material, the glass may be up to 2 mm thick. Making use of the TruMicro lasers equipped with TOP Cleave at this thickness, it is possible to achieve cutting speeds of up to 1 m/s—100 times faster than is possible without this arrangement. Even sapphire, the second hardest transparent material, may be processed in this manner. For example, using the TruMicro 5080 laser—which has a repetition rate of up to 1000 kHz, energy pulses up to 500 μJ, and average power >150 W—and TOP Cleave optics, it is possible to create a long focus line of laser light that can separate glass more than 1 mm thick.
Brazing of hot-dipped galvanized material
The automotive industry has an increasing interest in using hot-dipped galvanized materials. In addition to practical differences such as increased resistance to corrosion, hot-dipped galvanized metals are less expensive than electrogalvanized materials and more readily available worldwide.This process is achieved using a standard fiber-delivered 6 kW solid-state laser (TruDisk 6002) with a standard laser light cable to deliver the beam to the tactile seam tracking optic from Scansonic. The Scansonic Adaptive Laser Optic ALO3 serves as the laser processing head and, for this application, requires just a minor modification.
When brazing hot-dipped galvanized materials, the three spots on the surface of the material have different diameters and power intensities. The small spots play a vital role. The zinc coating can be pre-conditioned and a preheating of the surface of the parts is achieved. The new brazing process is smoother and the brazing speed can be increased.
With this solution, it is possible to ensure that the position of the spots in relation to each other and to the wire is independent from the rotation and the positioning of the tactile arm of the optic. Therefore, the Scansonic ALO3 can be used without any limitations, which is specifically advantageous for tailgate processes and the beginning/end of the seams where large reorientations of the optic-handling robot takes place (see Fig. 3).
The beam shaping allows the brazing process to be realized so that there are no difficulties if, for example, a laser light cable has to be changed. The advantages are also seen in standard maintenance procedures because users need only a single optic as a spare part for aluminum welding and brazing. The spot geometry and intensity profile, and especially the distribution of power between the individual spots, are inscribed in the beam shaping component. In addition, the orientation of the spots is fixed with respect to this component, and as such, it does not depend on any other parameter.
While this is the first application in the multi-kilowatt range for a customized beam using this beam shaping technology, other beam shape geometries are possible, which open up the potential for similar applications such as different brazing seam dimensions.
Yvonne Guertler is industry manager automotive and Max Kahmann is product manager ultrafast lasers, both at TRUMPF Laser- und Systemtechnik GmbH, Ditzingen, Germany; e-mails: [email protected] and [email protected]; www.trumpf.com.