Motion Control: Linear motion devices: What is a voice-coil actuator?
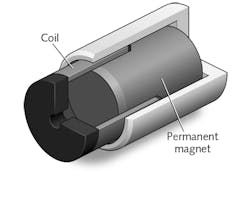
JAMES MITCHELL
A voice-coil actuator, also known as a noncommutated DC linear actuator, is a type of direct-drive linear motor. The term “voice coil” comes from one of its historically first applications: vibrating the paper cone of a loudspeaker. These devices are currently used for a wide range of applications, including moving much larger masses. For example, in optics, voice-coil actuators are typically used in focusing applications, oscillatory systems, mirror tilting, and miniature position control of up to three axes.
This type of actuator consists of a permanent-magnetic-field assembly (a combination of permanent magnets and ferrous steel) and a coil assembly. The current flowing through the coil assembly interacts with the permanent magnetic field and generates a force vector perpendicular to the direction of the current. The force vector can be reversed by changing the polarity of current flowing through the coil.
Noncommutated DC linear actuators are capable of a displacement of up to 5 in. and come in a range of sizes, from devices that generate a few ounces of force to others that generate several hundred pounds of force (see Table 1). In addition, voice-coil actuators can move bidirectionally, have a relatively constant force over the entire stroke, and can be used for either open- or closed-loop position or force applications.
TABLE 1. Typical specifications for voice-coil actuators
Type | Stroke | Peak force | Diameter | Power consumption | Frequency range |
Moving coil | 0.1 to 5.2 in. 0.1 to 134 mm | 0.1 to 1755 lbs 0.1 to 7020 N | 0.4 to 10 in. 10 to 254 mm | 1 to 2700 W | 1 to 500 Hz |
Moving magnet | 0.1 to 4 in. 0.1 to 101 mm | 0.1 to 419 lbs 0.1 to 1865 N | 0.4 to 6.5 in. 10 to 164 mm | 1 to 3400 W | 1 to 500 Hz |
A voice-coil actuator generates a force based on an interaction of current-carrying conductors in a permanent magnetic field. The force generated by the voice coil is proportional to the cross product of the current flowing through the coil and the magnetic flux in the permanent magnetic field, as dictated by Lorentz’ force equation. In a simple illustrative example, the force F produced on a straight wire of length L carrying a current I and oriented perpendicular to a magnetic field B (F, I, and B are vectors) is:
F = IL × B
(The calculation is more complicated for real devices because of their nonstraight wire geometry and varying orientation of voice-coil wires with respect to the magnetic field.)
The force generated is relatively constant throughout the stroke of the actuator, with minor decreases in force at the beginning and end of the stroke. Either the coil assembly or permanent-magnetic-field assembly can be used as the moving member in a voice-coil actuator.
Moving coil
Voice-coil actuators come in a variety of packages—the type that most people are familiar with is the moving-coil actuator. These typically comprise a coil wound around a bobbin, which can be made from and of numerous nonmagnetic materials, and which moves in and out of a permanent-magnetic-field assembly consisting of a steel housing with a concentric permanent-magnet assembly at its center (see Fig. 1).
Moving magnet
Another common type of actuator is the moving-magnet design, where the coil is fixed and the magnet assembly moves. This construction change prevents coil leads that require movement during operation. The package operates similarly to the moving-coil design, except that instead of an exposed coil that moves in and out of the magnet assembly, the moving-magnet device has a permanent-magnetic-field assembly piston that moves inside a cylindrical coil tube (see Fig. 2). This style often comes with the permanent-field assembly attached to a shaft and end caps that contain bearings, so that this style is most commonly supplied with an integrated bearing system.Variations exist on these actuator designs that allow for unique geometry and the integration of voice coil actuators into numerous types of applications. A few examples of customizations available are:
- Large radial clearances so that the voice coil can be used in limited-rotation applications
- Designs in which the voice-coil motor is intentionally operated in an arc (this is commonly referred to as a rotary voice-coil actuator)
- The use of low-outgassing materials to enable use in vacuum environments
- Integration of feedback devices for closed-loop control
Advantages of voice-coil actuators include:
- Simplicity of construction
- Very low hysteresis
- Small size
- High accelerations
- No cogging (no “preferred” positions) or commutation
Amplifier selection
An amplifier capable of providing the needed current and voltage to make the desired move is required. To size the amplifier to the voice-coil actuator, the continuous and peak current, back emf (to determine required DC bus voltage), and the actuator resistance and inductance should be known.
Brushed-type amplifiers are used to run single-phase (two-lead) actuators. These amplifiers can have some built-in intelligence and may require additional software. A linear amplifier is ideal for running low-inductance actuators.
Voice-coil actuators vs. solenoids
Another type of motion device, the solenoid, is sometimes confused with the voice-coil actuator. However, while a voice coil generates a force based on an interaction of a current carrying conductor in a permanent magnetic field, a solenoid generates force based on an electromagnetic field that is created by a current carrying conductor.
A solenoid consists of a coil that is contained in a ferrous steel housing and a movable steel slug or washer. An electromagnetic field is generated by current being applied to the coil. The magnetic-field intensity determines the amount of force that can be generated by the solenoid. When the power is turned off, the force drops to zero and the spring returns it to its extended position.
The forces are initially high—but as the stroke increases, the force decreases. Solenoids are typically used to open latches or open or close valves, and are either used to apply a holding or latching force.
The question of whether to use voice-coil actuators or solenoids for small-displacement motion control applications comes up often. If your application simply requires opening or closing a valve, a solenoid might be an option. However, solenoids have limitations when it comes to force linearity and stroke length.
Because voice-coil actuators typically cost more than an off-the-shelf solenoid, many customers try to use a solenoid when a voice-coil actuator is the more appropriate solution. Some applications require a constant force throughout the travel length, and in these situations a solenoid is insufficient because of the diminished force through the travel, whereas a voice-coil actuator provides constant force (see Table 2). This is particularly important in oscillatory systems. Another advantage that the voice coil provides is force control without a feedback device because the force output (at any position in the stroke) is directly proportional to the current input.
TABLE 2. Comparison of voice-coil actuators and solenoids
Voice-coil actuator | Solenoid | |
Force | Low to medium | High |
Stroke | 5 in. maximum | ¼ in. maximum |
Constant force | Yes | No |
Reversible | Yes | No |
Position/force control | Yes | No |
Cost | Moderate | Low |
Voice-coil actuators generally lend themselves to a higher force density, thus achieving higher strokes and forces in a smaller package size than their solenoid counterparts.
James Mitchell is a senior engineer at H2W Technologies, Santa Clarita, CA; e-mail: [email protected]; www.h2wtech.com.