Photonics Products: High-speed Imaging: How to choose a high-speed camera: Understanding new imaging sensors and techniques
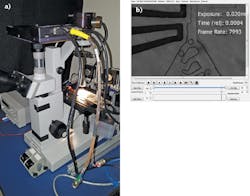
According to Wikipedia, high-speed cameras are those that exceed frame rates of 250 frames per second (frames/s). However, in scientific terms, those types of speeds are child's play. Even inexpensive digital cameras routinely exceed 1000 frames/s, and streak cameras have been designed that reach one trillion frames/s.
But the scientific workhorses found in most laboratories for studying laser-based ignition events, ultra-rapid industrial production-line assembly and processing, chemical and biological events, and even vehicle crash-test outcomes are those complementary metal-oxide semiconductor (CMOS) or charge-coupled device (CCD) cameras with imaging speeds that range from several thousand to around one million frames/s.
Of course, imaging speed is tightly coupled with imaging resolution and light level. An analysis of the always-improving capabilities of high-speed imaging cameras highlights the photonics advances that allow users to freeze time for a continually expanding parade of applications.
At its heart
Every camera is a complete optoelectronic system with optics, optomechanics, detector, housing, and electronic data storage and control components. But in general, the performance parameters of any camera are dictated by its imaging sensor, around which all other system components are designed.
Typically, CMOS sensors are considered optimal for high-speed imaging applications. Unlike CCD sensors with a limited number of pixels that each convert input light to a voltage that is sent off the chip through a limited number of output nodes (one up to a few) as an analog signal, CMOS sensors contain the amplifiers and digital-to-analog converters (DACs) within the sensor chip, avoiding the power-hungry, slower-readout trap of off-chip CCD image processing.
"The CMOS sensor is at the heart of many high-speed cameras, with key consideration to its higher number of sensor taps/channels for rapid photon-to-electron conversion to quickly 'rip' electrons from the sensor," says Andrew Bridges, director, sales & marketing at Photron (San Diego, CA). "Large numbers of DACs can be big heat generators, as can the increasing demand for more memory. Fortunately, the ideal onboard memory scenario can also be accomplished in CMOS via rapid data-off-loading techniques."
In addition to minimizing heat generation and sensor noise, "Light sensitivity is a critical factor in high-speed imaging applications," says Bridges. "When the FASTCAM SA5 was released around 2008, the ISO value of 10,000 was impressive. Now, the new sensor electronics in our FASTCAM SA-Z provides ISO 50,000 for the 12-bit monochrome and 20,000 for the 36-bit Bayer color version, both using 20 μm square pixels." Bridges says sensitivity was improved by developing a new circuit design that greatly reduced noise while increasing gain.
"We measure our FASTCAM cameras to the true industry ISO Ssat 12232 standard for exemplary light sensitivities at high frame rates, with shorter shutter/exposure speeds, and greater depths of field under the same lighting conditions without added illumination," says Bridges.
An alternative to standard area-scan cameras are line-scan cameras that measure speed not in frames per second, but in the frequency at which a few lines with thousands of pixels gather data as moving objects are scanned by the sensor. With short exposure times, these cameras are typically accompanied by high-brightness light sources for industrial machine-vision applications.
Chromasens (Konstanz, Germany) trilinear cameras achieve high levels of color precision by arranging three RGB sensor lines in extremely close proximity to capture an image of a moving object. The allPIXA wave camera is based on a quadlinear CMOS color line-scan sensor with line lengths up to 15,000 × 4 lines and operates at speeds of 150 kHz with 850 Mpixels/s throughput.
Although its CCD camera line rates are typically in the tens of thousands, Teledyne DALSA (Waterloo, ON, Canada) developed a custom sensor and camera in 2003 capable of imaging at 100 million frames/s. This high-frame-rate camera had a custom pixel design for an application that required very short-term imaging (bursts) and captured a limited number of images (10–15) that were read out slowly, providing detailed information related to an incident around a single event.
For ultrahigh-speed events with durations from tens of microseconds to tens of nanoseconds such as laser-induced shock, micro-detonations, hyper-velocity impacts, and other ballistic events and certain biological processes, Specialised Imaging (Tring, England and Temecula, CA) uses multiple very-high-resolution (up to 1360 × 1040 pixels) sensors built around an optical beamsplitter. By sequentially firing each sensor at any frame rate from 100 frames/s up to 1 billion frames/s, one avoids the limitation that comes with having to rapidly read out the sensor data. The beamsplitter splits the primary image into as many as 16 ports while maintaining distortion-free images with > 100 lp/mm spatial resolution and near-zero parallax.
Specialised Imaging cameras use intensified CCD (ICCD) sensors that act as an electrooptical shutter with gate times as short as a few nanoseconds and also act as a gain stage to amplify the short exposures of light to a recordable level for the CCD that is fiber-optic-coupled to the microchannel tube plate. By using a fast (300 ns decay) phosphor and a line-transfer type CCD, two frames can be captured from one ICCD within 550 ns between frames, essentially creating a 16-frame camera with top speed of 14.5 million frames/s—all from an 8-channel ICCD camera.
Frame rates and data storage
"A few years back, our FASTCAM ultima APX-RS was the fastest high-speed video camera available with 250,000 frames/s at a very small resolution of 128 pixels wide × 16 pixels tall," says Bridges. "Today, the FASTCAM SA-Z can record 2.1 million frames/s at 128 × 8 pixels [wide × tall] or 252,000 frames/s for a 384 × 128 pixel image."
But Tim Brandt, product manager at Fastec Imaging (San Diego, CA), reminds us that higher frame rates are not always the best way to capture meaningful information. "With higher resolution, it's possible to do a better job covering a larger field of view. Suppose you wish to capture five images of an object moving through the frame in order to characterize its movement. An object without impediment will move through a very limited field of view much more quickly than it would a larger one, so in order to capture five images in the limited field of view, you will need a higher frame rate," he says. "But there are two major advantages to using the larger field of view. First, you don't need such a high frame rate, and second, you will get images of the object over a longer period of time, which will yield more and better information about its behavior."
Fastec TS and IL high-speed cameras top out with frames rates from 18,000 to around 60,000 frames/s with a sweet spot of about 5000 frames/s for a 768 × 300 pixel image-mid-range performance at a significantly lower cost than million frames/s camera alternatives (see Fig. 1).
"Most high-speed cameras record high frame rates for only seconds at a time, as there are limits to the quantity of high-speed memory that can be offered in a camera. For example, at 1 Mpixel resolution, an 8-bit camera recording 1000 frames/s creates 1 GB of raw image data per second," says Brandt. "Our TS/IL4 and TS/IL5 can record directly to an internal solid-state disk [SSD] drive with up to 1 TB capacity for many minutes, depending on frame rate and resolution and maintain data rates up to 450 MB/s to internal drives using 8 GB of internal high-speed memory as a buffer to accommodate lapses in SSD bandwidth."
Brandt continues, "All Fastec IL and TS cameras with SSDs can partition their memory into as many as 16 segments, recording high-speed video to each segment in turn while the previous segments are being transferred to the drive—a 'FasFire' feature that allows the user to continually record high-speed bursts while saving to nonvolatile memory." Brandt says that it takes so little time for the images to be saved to the SSD that the user rarely, if ever, has to wait for the camera to clear its buffer for the next shot, changing the workflow to a point where many tests may be run consecutively in a very short period of time for expanded high-speed applications coverage.
And of course, frame rate is tightly correlated to resolution. The Vision Research (Wayne, NJ) Phantom Miro C-110 with 12-bit, 0.5 inch CMOS sensor (color or monochrome) can record 800 frames/s at its full 1280 × 1084 resolution, but up to 29,840 frames/s at lower resolution values. With 8 GB of internal memory, users can record up to 5 s at full resolution and maximum frame rate.
Enabling applications
Beyond the classic image of a bullet piercing a block of wood or shatter-proof glass, high-speed imaging can reveal events critical to expanding the scientific understanding of important scientific, biological, and industrial processes (see Fig. 2).And in the world of aeronautics, high-speed cameras play an important role in improving understanding of jet components and in-flight maneuvers. NASA engineers have used the Fastec handheld TS3 in the cockpit of a jet fighter to get high-speed Schlieren images of the shock waves produced by another jet, using the sun's rays obstructed by the wing of a third jet to create the requisite collimated illumination.
Shutter options are also important in turbine and propeller imaging applications. "Today's CMOS sensors use global electronic shutters, where all pixels are exposed at the same time," adds Bridges. "This prevents issues long associated with rolling shutters, where each line of pixels is exposed one after the other, permitting the object to move from one line to the next and resulting in visible aberrations (see Fig. 5)."Limitations
High-speed imaging is difficult to achieve for low-light applications that typically require longer exposures to gather appropriate image detail. "For imaging cell function, for example, high speed must be combined with extreme sensitivity. Physiological relevance depends not only on quantitative performance; maintaining a homeostatic environment means limiting illumination to the absolute minimum-a difficult requirement when combined with high frame rates," says Rachit Mohindra, product manager at Photometrics (Tucson, AZ). "EMCCD [electron-multiplying CCD] cameras address this speed vs. sensitivity tradeoff through use of a high-bandwidth output amplifier combined with on-chip multiplication of image signal. The result is an input-referred electronic read noise of < 0.3 electrons RMS. To further improve detected signal under these conditions, the sensors are back-illuminated with > 90% QE [quantum efficiency]."
"In the quest for even more speed for imaging highly dynamic cellular events, field of view is the first sacrifice made, with smaller regions of interest (ROIs) being used to achieve the required faster frame rates," adds Mohindra. Photometrics developed its LightSpeed mode for its Evolve 512 Delta camera to pipeline pixel readout to achieve even higher frame rates with critical flexibility-placing no restrictions on the location of ROIs, and able to be used in conjunction with binning. LightSpeed mode maximizes detection of high-speed events at frame rates of up to 3000 frames/s.
While several thousand frames per second may be challenging for certain low-light biological applications, even millions of frames can be inadequate for some emerging applications. "Despite our multi-million frames per second cameras, customers continue to seek even higher frame rates for certain laser and x-ray analytics, high-end ballistics, and ultrafast crack-propagation studies," concludes Bridges. "And even though in situ image storage or ISIS-an unfortunate acronym in light of current events on the world stage-wherein the frames of an image are stored on the sensor itself, ISIS sensor architecture can only save 180 frames at 5 million frames/s, equating to just 36 μs of recording time. Many customers are more accustomed to several seconds' worth of data, greatly easing the burden on reliably triggering a camera so as not to miss the event. In essence, the sensor architecture and support electronics ultimately limit imaging speeds."
For More Information
Companies mentioned in this article include:
Chromasens
Konstanz, Germany
www.chromasens.de
Fastec Imaging
San Diego, CA
www.fastecimaging.com
Photometrics
Tucson, AZ
www.photometrics.com
Photron
San Diego, CA
www.photron.com
Specialised Imaging
Tring, England and Temecula, CA
http://specialised-imaging.com
Teledyne DALSA
Waterloo, ON, Canada
www.teledynedalsa.com
Vision Research
Wayne, NJ
http://visionresearch.net
For a complete listing of companies making high-speed cameras, visit the Laser Focus World Buyers Guide (https://www.laserfocusworld.com/directory).
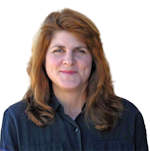
Gail Overton | Senior Editor (2004-2020)
Gail has more than 30 years of engineering, marketing, product management, and editorial experience in the photonics and optical communications industry. Before joining the staff at Laser Focus World in 2004, she held many product management and product marketing roles in the fiber-optics industry, most notably at Hughes (El Segundo, CA), GTE Labs (Waltham, MA), Corning (Corning, NY), Photon Kinetics (Beaverton, OR), and Newport Corporation (Irvine, CA). During her marketing career, Gail published articles in WDM Solutions and Sensors magazine and traveled internationally to conduct product and sales training. Gail received her BS degree in physics, with an emphasis in optics, from San Diego State University in San Diego, CA in May 1986.