MICROELECTRO- MECHANICAL SYSTEMS (MEMS): TI's DLP chip powers more than picoprojectors
Microelectromechanical systems (MEMS)-based digital-light-processing (DLP) technology from Texas Instruments (TI; Dallas, TX) is finding its way into many more arenas than just well-known picoprojector applications—so many in fact that this year's Photonics West 2010 MOEMS–MEMS Conference 7596 was almost entirely devoted to DLP and other digital-micromirror-device (DMD)-based applications. In addition to display applications and dynamic speckle reduction, several other medical and industrial DLP applications are emerging.
Medical imaging and illumination
Researchers at the University of Texas at Arlington (UTA), TI, the National Institute of Standards and Technology (NIST; Gaithersburg, MD), and the University of Texas Southwestern Medical Center (Dallas, TX) are collaborating on a hyperspectral imaging system with a DLP-based light source from Optronic Laboratories (Orlando, FL) that can rapidly analyze biological tissues using reflectance spectroscopy.1 The spectral illuminator operates from 380 to 780 nm with a full-width half-maximum (FWHM) bandpass of 8.55 nm when using a 350 µm slit. Reflected data is sent to a 1392 × 1040 pixel (with 6.45 × 6.45 µm pixels) CCD image sensor with a 12 or 14 bit, 10 or 20 MHz digitizer. The clinical-grade imager projects light through a liquid light guide and gathers reflections using a standard Nikon 50 mm lens. The reflected spectroscopic images are formatted into a 3D hyperspectral image cube; applying a proprietary chemometric algorithm results in a chemically encoded image visualizing the chemistry of the tissue at near-video rates.
At the Parkland Memorial Hospital (Dallas, TX) burn unit, the hyperspectral system gathered both visible-range and near-IR data on burn wounds to determine percent contribution of oxyhemoglobin in the tissue at different depths in order to establish how much "dead" tissue should be removed to speed healing. Using a slightly different setup, the instrument is also being used to study diabetic retinopathy by analyzing hyperspectral data from the retina that indicates oxygenated blood perfusion. Finally, the speed of DLP technology enables advanced imaging for laparoscopic surgery, aiding navigation through tissues during gallbladder and kidney surgery for improved post-operative healing.
Another medical-imaging system from O2view (Marken, the Netherlands) and collaborators from Quest Innovations (Middenmeer, the Netherlands), Optec (Parabiago, Italy), and Leiden University Medical Center (Leiden, the Netherlands) takes illumination a step further by using the DLP device to provide selective, programmable illumination based on visual feedback from one or more cameras.2 The stereoscopic system uses multiple CCD sensors to gather RGB and near-IR spectral data from a patient. Based on the converted image data, the DLP chip can be programmed to project light from several LED and low-level light therapy (LLLT) laser sources back to the patient in the form of a checkerboard pattern for skin-resurfacing applications, or in the recreated pattern of cancerous tissue locations to target affected areas, for example.
Rapid prototyping
Various stereolithography and additive manufacturing processes can be used for rapid prototyping. For hearing aid and dental markets, EnvisionTEC (Ferndale, MI) is using DLP-based technology in an additive manufacturing process to manufacture dental and hearing aid components.3 When a fixed lamp or LED source is used to fabricate these parts, the cure depth in a particular voxel (pixel volume) is typically fixed to something on the order of 100 µm. But by adding a DLP chip in the illumination path, programmed movements of the individual MEMS pixels within the DLP chip enable rapidly varying gray-scale illumination that can deliver variable cure depths (and improved contour shapes) to individual voxel areas, further increasing the speed of the prototyping process (see figure). By projecting a varying illumination field (with voxel cure depths from, say, 0 to 100 µm) across the material to be cured, fabrication rates can be increased 2 to 3 times compared to using uniform illumination.
REFERENCES
- K.J. Zuzak et al., "The robustness of DLP hyperspectral imaging for clinical and surgical utility," Photonics West MOEMS-MEMS Conf., San Francisco, CA, paper 7596-03 (Jan. 27, 2010).
- R.G.M. van Melick et al., "DLP technology's pivotal role in O2view's versatile medical projection/illumination device," Photonics West MOEMS-MEMS Conf., San Francisco, CA, paper 7596-02 (Jan. 27, 2010).
- A. Siblani, "The use of DMD technology in rapid manufacturing equipment for mass customization applications," Photonics West MOEMS-MEMS Conf., San Francisco, CA, paper 7596-14 (Jan. 27, 2010).
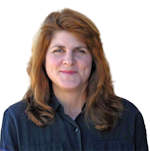
Gail Overton | Senior Editor (2004-2020)
Gail has more than 30 years of engineering, marketing, product management, and editorial experience in the photonics and optical communications industry. Before joining the staff at Laser Focus World in 2004, she held many product management and product marketing roles in the fiber-optics industry, most notably at Hughes (El Segundo, CA), GTE Labs (Waltham, MA), Corning (Corning, NY), Photon Kinetics (Beaverton, OR), and Newport Corporation (Irvine, CA). During her marketing career, Gail published articles in WDM Solutions and Sensors magazine and traveled internationally to conduct product and sales training. Gail received her BS degree in physics, with an emphasis in optics, from San Diego State University in San Diego, CA in May 1986.