Photonics Products: Imaging for Surveillance and Security: SWIR cameras cut through haze for surveillance and security
The use of imaging systems for security, defense, and surveillance depends greatly on taking advantage of the infrared (IR) spectrum, which can be divided into near-, shortwave-, midwave-, and longwave-infrared (NIR, SWIR, MWIR, and LWIR, respectively). NIR cameras for security and surveillance are typically low-light (night vision) devices, while MWIR and LWIR cameras accomplish their tasks via thermal imaging. However, SWIR cameras are useful security and surveillance devices in their own right—sometimes by themselves, and often in combination with other imagers.
The spectral border between NIR and SWIR is commonly stated to be around 1.4 µm, although for this article, an exact figure is not important. The boundary between SWIR and MWIR is generally stated to be 3 µm.
Imaging through haze
Sensors Unlimited (Princeton, NJ), a part of Collins Aerospace, produces a wide variety of SWIR imagers, including handheld SWIR scope systems, area cameras, line-scan cameras, and linear photodiode arrays. The sensor technology, based on indium gallium arsenide (InGaAs), was brought to market in 1991 by Sensors Unlimited.
Applications for these SWIR devices include facility, port, and border security and surveillance, as well as other covert operations; low-light-level imaging; military driver vision enhancement; and military IR laser spotting and tracking. As an example, the GA1280JSX SWIR camera has a high-definition (1280 × 1024 pixel) sensor that images at 60 frames per second (fps) at full resolution with high sensitivity in the 0.9–1.7 µm spectrum and covers NIR/SWIR from 0.7 to 1.7 µm or, optionally, visible/SWIR from 0.5 to 1.7 µm.
“One of the most compelling security and surveillance uses of the GA1280JSX high-definition SWIR camera involves imaging through atmospheric haze,” says Curt Dvonch, an applications engineer at Sensors Unlimited. “These two images [see Fig. 1] were captured simultaneously and clearly demonstrate how SWIR cameras outperform visible cameras in polluted, hazy environments. The SWIR camera outperforms the visible camera primarily because SWIR photons are able to penetrate through atmospheric haze and smog, while visible-wavelength photons are scattered in air that is heavy with particulate matter.”
Multiple target tracking
FLIR Systems (Wilsonville, OR) makes InGaAs SWIR cameras based on its focal-plane array (FPA), which the company also sells separately. These FPAs have a capacitive transimpedance amplifier circuit design that is optimized for applications ranging from security imaging to high-speed scientific laser testing (which requires multiple outputs and dynamic windowing).
One of FLIR’s SWIR cameras, the Boson, is optimized for size, weight, and power plus cost (SwaP+C). With a 21 × 21 × 28 mm size, 15.5 g lensless weight, and power consumption of <1.6 W, the camera is military-qualified—it has no thermoelectric cooler (TEC), which helps it achieve its SwaP+C optimization. The Boson’s slightly larger cousin, the Tau, does have a TEC, which gives it the temperature stability needed for precision use in the field. The camera is 38 × 38 × 36 mm in size and consumes 3.2 W or less of power. Both cameras come in SWIR (0.9 to 1.7 µm) and visible/SWIR (0.6 to 1.7 µm) versions.
In addition to cameras, FLIR produces an entire all-terrain reconnaissance and surveillance vehicle called the LTV-X (see Fig. 2), which carries swappable mounted sensors and imagers of various types, including NIR, SWIR, thermal, laser rangefinding, and radar. The vehicle can be transported in a V-22 Osprey tilt-rotor military aircraft and, with its camera control system, can track up to 500 threats simultaneously.OEM variants
Raptor Photonics (Larne, Northern Ireland), which has been making InGaAs-based cameras for 13 years, has built up a range of both SWIR and visible/SWIR cameras with various resolutions and pixel sizes from 320 × 256 to 640 × 512 and, most recently, a new high-definition camera with 1280 × 1024 pixel resolution. Using InGaAs sensors from several suppliers, both off-the-shelf and custom-designed, the company designs low-noise core modules. As described by Mark Donaghy, the company’s vice president of sales and marketing, Raptor can then offer custom variants including mechanical layout, interface, cooling, optical design (see Fig. 3), and so on to meet the exact needs of its surveillance and security customers. “In fact, 90% of what Raptor ships each year are OEM variants,” Donaghy says. “For example, there are now 16 different OEM variations of the OWL 640 camera, each one designed to the specific needs of individual customers.”With a 1280 × 1024 InGaAs sensor, the OWL 1280 camera has a spectral range that extends all the way across the visible spectrum, resulting in a total range of 0.4 to 1.7 µm at high sensitivity. The 10 × 10 µm pixel pitch enables high-resolution imaging with less than 40 electrons (e-) readout noise and with a large intra-scene dynamic range of 69 dB, enabling simultaneous capture of bright and dark portions of a scene, Donaghy says.
The camera runs from 10 up to 60 Hz and has onboard automated gain control (AGC) to enable optimal contrast images from low light to bright light. The camera is temperature stabilized with no fan. Donaghy notes that it is well suited for low-light and nighttime imaging for land and airborne applications.
“The OWL 1280 has been adopted into several gimbal programs by OEMs and prime contractors,” he explains. The HD format offers much better resolution for the operator and the VIS-SWIR range enables imaging through smoke, haze, sea fog, as well as other low-visibility conditions. It is also critical for seeing key laser lines—for example, 1550 nm. Being housed in a gimbal, the OWL 1280 is designed to offer optimum SWaP performance and the camera can handle extreme environmental conditions such as temperature (-40˚C to +75˚C) and moisture (conformally coated electronics). Each camera is built to ISO9001:2015 standards, meaning the camera’s quality and reliability is exceptional, crucial for mission-critical applications.
Donaghy notes that for one specific customer, the camera is being provided in a board format laid out with flexible cables in a configuration designed so that the assembly can be “concertinaed” (compressed) into a tight space envelope.
High-speed imaging
First Light Imaging (Meyreuil, France) has unveiled an uncooled SWIR camera, the C-RED 3, which is optimized for low SwaP+C. The camera is based on a TECless InGaAs sensor sensitive from 0.9 to 1.7 µm and has a more than 70% quantum efficiency (QE), says Jean-Luc Gach, the company’s founder and scientific advisor. The camera has a refresh rate of up to 600 fps with a readout noise below 50 e-.
The C-RED 3 includes an embedded electronic shutter with an opening width lower than 5 µs. While the camera is intended primarily for industrial use, it is also well suited for surveillance via fixed mounting or on mobile platforms such as unmanned aerial vehicles (UAVs).
The camera supports a high-dynamic-range mode (HDR) providing 93 dB dynamic range and a true 16-bit linear response, having at the same time a low noise below 50 e- and a full well capacity of more than 106 e-. The C-RED 3 can work also in AGC mode at standard dynamic range. It is especially well suited for short exposure times in applications where very high speed is needed.
For More Information
Companies mentioned in this article include:
First Light Imaging
Meyreuil, France
FLIR Systems
Wilsonville, OR
Raptor Photonics
Larne, Northern Ireland
Sensors Unlimited, a part of Collins Aerospace
Princeton, NJ
DISCLAIMER: While we try to include information from the broadest possible number of companies that manufacture the products featured in our Photonics Products series, because of limited word count as well as deadlines that cannot always be met by requested contributors, we cannot possibly include all companies and regret if your company is not included in our series.
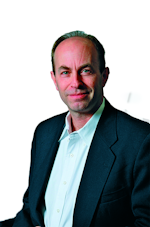
John Wallace | Senior Technical Editor (1998-2022)
John Wallace was with Laser Focus World for nearly 25 years, retiring in late June 2022. He obtained a bachelor's degree in mechanical engineering and physics at Rutgers University and a master's in optical engineering at the University of Rochester. Before becoming an editor, John worked as an engineer at RCA, Exxon, Eastman Kodak, and GCA Corporation.