PHOTONICS APPLIED: RENEWABLE ENERGY: Overcapacity stifles solar PV equipment suppliers
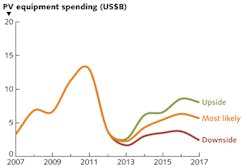
The solar photovoltaic (PV) industry is currently suffering from overly ambitious investments in fabrication (fab) capacity that date back to 2010. Despite continued end-market growth, over-capacity has ushered in a severe and prolonged downturn in PV capital expenditure that is expected to last until 2015. Pricing throughout the value chain is descending to levels that are below the typical production costs of many PV manufacturers. Set against an end market that continues to see year-on-year growth and increasing globalization, this has created huge uncertainty and a strong decline in investor confidence.
As the PV industry seeks to recover from gross-margin levels in the low-single-digit range (at best), the adoption of new technologies has taken a backseat. The technology ups and downs due to this industry "shakeout phase" are resetting many of the assumptions about how next-generation PV technologies will ultimately thrive.
PV industry drivers remain differentiated
The PV industry does not have a common roadmap such as the International Technology Roadmap for Semiconductors (ITRS; www.itrs.net). And as such, there are no technology buy cycles that can offer a glimmer of hope for PV equipment suppliers during cyclic downturns. Until 2012, the PV industry had not actually seen any meaningful capital equipment expenditure (capex) downturn. Therefore, the events of the past 12–18 months represent new territory for PV equipment suppliers whose growth had been founded on PV revenue streams (see Fig. 1).
Fab investments from 2009 to 2012 were based upon a wide range of technologies, including many different thin-film types or process-flow variants. Many of these manufacturers were seeking to challenge the dominance of crystalline silicon (c-Si)-based PV production and were often pursuing technologies that were largely unproven. Conversely, when the vast quantity of c-Si capacity came online in China and Taiwan during 2010 and 2011, this was based on standard cell technologies with limited differentiation. The outcome was a diverse range of manufacturers, none of whom was committed to any single—or necessary—roadmap.
Generally, PV equipment suppliers either satisfied a small group of thin-film producers or supplied standardized tooling to c-Si expansions in Asia. Up until 2011, this was not necessarily a problem for chosen tool suppliers. Investments into all technologies were extensive and being a preferred tool supplier to any gigawatt-level fab expansion was typically sufficient to fill order books. However, the capacity was collectively adding up and it was only a matter of time before chronic over-capacity was to hit the sector.
End-market demand robust, but lacks elasticity
There is no shortage of end-market drivers for renewable energy deployment or for solar PV within any overall energy mix. Almost every country now has a long-term renewable energy plan that sees various share allocations being assigned to solar, wind, hydro, or biomass. Even within solar, there are still allocations being made across both solar PV and solar thermal. Solar PV end-market demand increased to 29 GW during 2012 by which point cumulative PV installations had passed the 100 GW level, with an additional 230 GW set to be added in the next 5 years (see Fig. 2).End-market demand for solar PV does not yet have a global driver. It is still the accumulation of country-specific drivers that promote PV over other renewables within any overall change in energy supply mix. Thus, despite the erosion in system prices that has arisen from the over-capacity and over-supply environment, this has been insufficient to create global demand elasticity. A consequence is that the end market is policy-constrained and not production-led. So the capacity overhang will remain a problem until end-market demand approaches the effective capacity levels in play across the key PV suppliers today.
These realities have a direct impact on capex and technology. Now there is no fundamental requirement to add new capacity. Also, the capacity installed by the dominant market leaders is sufficient to fulfill order books and grow market share. The focus is on prudent capacity utilization, cost reduction, and diligent use of in-house and outsourced manufacturing.
New technologies challenged
The shakeout from several hundred PV manufacturers to a more realistic scenario in which the top 20–30 supply 80–90% of market demand has had a direct impact on the PV technologies being used in production. Several years ago, there was a vibrant and optimistic thin-film segment that included many new amorphous silicon (a-Si)-based equipment suppliers. Having established deposition tool suppliers from the display industry reposition themselves as primary turnkey line suppliers only added credibility to claims that a-Si-based thin-film PV was a natural successor to c-Si manufacturing. But a-Si-based manufacturing failed to offer a competitive solution, with the end market seeing very little pull on panels whose conversion efficiency is pegged at the 10% level.
Similar analogies were seen on the copper indium gallium diselenide/copper indium selenide (CIGS/CIS) thin-film technology front. Manufacturing differentiation and the voice of domestic research communities also played a key role in selling this PV technology type to the investment community. But the failure of most of these startups to ramp production in a competitive manner, or satisfy follow-on funding requirements, has been widely publicized over the past 18 months, especially in the United States where most startup CIGS investment had occurred.
So thin-film solar is no longer seen as the default technology bet for differentiated fab investment and new technology equipment spending. With average selling prices for c-Si modules at the $0.60/W level today, and an overhang of capacity ready to satisfy any new demand at this price point, thin-film investment prospects have never been so low in the PV industry.
For laser industry tool suppliers serving the PV industry, the past two years has been a painful transition phase. Thin-film PV was the great hope of laser tooling suppliers for cell interconnection patterning and panel isolation; most of the revenue forecasts or sales prospects lists were based on the phasing of speculative thin-film capacity additions. In fact, any legacy euphoria from the laser community regarding PV can generally be traced to which suppliers were meeting turnkey line investments for Applied Materials (Santa Clara, CA), Oerlikon (Pfäffikon, Switzerland), ULVAC (Kanagawa, Japan), Jusung Engineering (Kwangju, South Korea) and Apollo Solar (now Hanergy Solar; Beijing, China). Having preferred supplier status to any of these companies generated unbounded excitement in PV when backlogs got inflated, but equally resulted in gloomy assessments of the industry when investments dried up for turnkey thin-film lines.
Across the c-Si segment, ramping proven technologies to multi-gigawatt levels was more important than implementing a new technology that could in theory differentiate existing suppliers of end-market demand. This left little opportunity for tool suppliers that were developing processes for high-efficiency c-Si cell concepts. The end-market application segments and downstream channels were not particularly interested in anything other than what was being offered to them at decreasing pricing levels.
With c-Si supply being dominated by Chinese PV manufacturers, low-cost standard product (mostly multi-c-Si modules) dominated the downstream channels. Some of these suppliers tried to implement new high-efficiency c-Si process flows (typically adding process steps for front- or rear-side cell production) during 2010 and 2011, but success was at best marginal. In fact, it confirms the difficulty with introducing high-efficiency c-Si technology types into volume mass production that only two companies have ever succeeded here—SunPower (San Jose, CA) and Sanyo/Panasonic (Osaka, Japan)—and it took each of these companies a decade of R&D efforts to perfect their recipes.
What's next?
Every equipment supplier to the PV industry now needs a new strategy. For some of the leading tool suppliers, the downturn has resulted in PV-specific business units being phased out or reconfigured within flat-panel display groups. For equipment suppliers that have no other meaningful revenue streams from adjacent technology sectors, the outlook is bleaker and potentially life-threatening.
Fortunately for laser tool suppliers, few had a sufficient pool of leading PV manufacturers on their order books in the first place. Thus the downturn has mainly represented a disappointment rather than a terminal disaster. But there is still the question of where to allocate R&D activities now that thin-film patterning is no longer the great hope for the laser community within PV (see Fig. 3).Consequently, the search resumes for the most likely high-efficiency c-Si cell concept that is going to see widespread adoption when capacity expansions resume. While there are some positive indicators that rear-side passivation layer deposition may offer short-term opportunities for laser tool suppliers, the next big chance will only occur when overall PV capital equipment spending rebounds.
Based upon end-market demand projections and the existing capacity of the major cell and module providers, the next upturn in capex is not predicted until 2015. New order intake is likely during 2014 as investor confidence returns and PV manufacturers start the slow return to profitability. But it is still too early to predict with confidence whether new added capacity will be based upon improved versions of technology used during the last investment phase, or any new technologies will have been qualified sufficiently to be deemed low risk for high-volume capacity additions.
Technology change must come to the PV industry over the next few years. Once cost reduction options are exhausted, the shakeout phase has been exhausted, and leading suppliers are showing a clear path to long-term sustainable profitability, then efficiency gains and technology changes should see greater prioritization. Since a technology roadmap has yet to emerge, there is still hope for those equipment suppliers that missed out in previous rounds of PV capacity expansion.
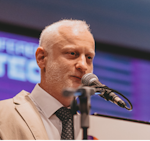
Finlay Colville
Dr. Finlay Colville has been Head of Research at PV-Tech and Solar Media Ltd since 2015. Before this, he spent 5 years as VP and head of solar at market research firm NPD Solarbuzz, and 10 years in various sales and marketing roles at Coherent, Inc. Dr. Colville holds a BSc in Physics from the University of Glasgow and a PhD in nonlinear photonics from the University of St. Andrews.