Carbon-nanotube optical rectenna converts visible light directly to DC current (with video)
Using multiwall carbon nanotubes and nanometer-scale rectifiers fabricated onto them, researchers at the Georgia Institute of Technology (Georgia Tech; Atlanta, GA) have demonstrated the first optical rectenna for visible light, a device that combines the functions of an antenna and a rectifier diode to convert light directly into direct current (DC).1
Potential uses for the optical rectennas include as uncooled photodetectors, energy harvesters that convert waste heat to electricity, and ultimately solar cells.
(Video: Georgia Tech)
In the new devices, metallic multiwall carbon nanotubes act as light-capturing antennas; oscillating charges produced by the impinging light moves through rectifier devices attached to them. The rectifiers switch on and off at record-high petahertz speeds, creating a small direct current. The devices operate at a range of temperatures from 5 to 77 °C.
Fabricating the rectennas begins with growing forests of vertically-aligned carbon nanotubes on a conductive substrate. Using atomic-layer chemical vapor deposition, the nanotubes are coated with an aluminum oxide material to insulate them. Finally, physical vapor deposition is used to deposit optically transparent thin layers of calcium then aluminum metals atop the nanotube forest. The difference in work functions between the nanotubes and the calcium provides a potential of about two eV—enough to drive electrons out of the carbon nanotube antennas when they are excited by light.
In operation, light passes through the transparent calcium-aluminum electrode and interacts with the nanotubes. The metal-insulator-metal junctions at the nanotube tips serve as rectifiers switching on and off at femtosecond intervals, allowing electrons generated by the antenna to flow one way into the top electrode. Ultralow capacitance on the order of a few attofarads enables the 10-nm-diameter diode to operate at these exceptionally high frequencies.
Billions of rectennas in an array can produce significant current, though the efficiency of the devices demonstrated so far remains below 1%. The researchers hope to boost that output through optimization techniques, and believe that a rectenna with commercial potential may be available within a year.
"We could ultimately make solar cells that are twice as efficient at a cost that is ten times lower, and that is to me an opportunity to change the world in a very big way," says Baratunde Cola, an associate professor of Mechanical Engineering at Georgia Tech. "As a robust, high-temperature detector, these rectennas could be a completely disruptive technology if we can get to 1% efficiency. If we can get to higher efficiencies, we could apply it to energy-conversion technologies and solar energy-capture."
The rectennas fabricated by Cola's group are grown on rigid substrates, but the goal is to grow them on a foil or other material that would produce flexible solar cells or photodetectors.
"We think we can reduce the resistance by several orders of magnitude just by improving the fabrication of our device structures," says Cola. "Based on what others have done and what the theory is showing us, I believe that these devices could get to greater than 40% efficiency."
The research is supported by the Defense Advanced Research Projects Agency (DARPA), the Space and Naval Warfare (SPAWAR) Systems Center, and the Army Research Office (ARO). Georgia Tech has filed international patent applications related to this work under PCT/US2013/065918 in the United States (U.S.S.N. 14/434,118), Europe (No. 13847632.0), Japan (No. 2015-538110) and China (No. 201380060639.2)
Source: Georgia Tech
REFERENCE:
1. Asha Sharma et al., Nature Nanotechnology (2015); http://dx.doi.org/10.1038/nnano.2015.220
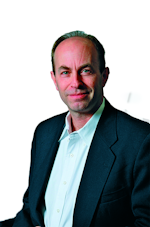
John Wallace | Senior Technical Editor (1998-2022)
John Wallace was with Laser Focus World for nearly 25 years, retiring in late June 2022. He obtained a bachelor's degree in mechanical engineering and physics at Rutgers University and a master's in optical engineering at the University of Rochester. Before becoming an editor, John worked as an engineer at RCA, Exxon, Eastman Kodak, and GCA Corporation.