More flexible display news: full-color AMOLED video from ASU and Universal Display
Tempe, AZ and Ewing, NJ--A lot is happening towards the commercialization of flexible displays. In addition to recent news of a mass-produceable flexible display substrate from ITRI and a very bright electrophoretic flexible display from Sony, The Flexible Display Center (FDC) at Arizona State University (ASU) and Universal Display Corporation (NASDAQ: PANL) have successfully fabricated the first full-color, flexible active-matrix organic light-emitting diode (AMOLED) display prototypes using the Center's bond/de-bond manufacturing process, in combination with Universal Display's full-color, top-emission phosphorescent OLED display technology and materials. The displays also use Universal Display's patented, proprietary single-layer encapsulation technology to seal the OLEDs made on DuPont Teijin Films Teonex polyester film. Successful fabrication of the displays involved incorporating materials and technologies concurrently developed by several additional members of the FDC's 30-member industrial consortium.
Funded by the US Army, the FDC is developing the full-color, flexible OLED displays for use in thin, lightweight, bendable and unbreakable devices capable of displaying full-color, full-motion video. The lower power consumption of Universal Display’s phosphorescent OLEDs compared to other full-color video display technologies is an important advantage for ultralight soldier-portable devices, and a range of OLED display products based on this technology are already in the marketplace.
A key enabler of the flexible displays announced today is Universal Display's recently introduced single-layer encapsulation technology that was designed for plastic substrate systems and thin-film devices, including flexible OLED displays. The encapsulation layer provides an effective barrier to protect thin film devices from environmental conditions, such as moisture and oxygen, which is critical for the long-term performance of OLED displays. Using environmentally benign and non-toxic materials in a potentially low-cost process, the barrier film technology has demonstrated its suitability for high-performance, flexible plastic substrate systems in these new AMOLED displays.
The displays are in a 3.8-inch diagonal QVGA format (320x240 pixels) and use Universal Display's phosphorescent red, green and blue OLED materials, which have already been proven to significantly reduce power consumption in numerous glass-based AMOLED products.
"The combined effort with Universal Display and our other industry partners to successfully produce flexible, full-color AMOLED displays validates our bond/de-bond manufacturing technology," said Nick Colaneri, director of the FDC. "The display industry is actively evaluating a variety of approaches to handling flexible plastic substrates in conventional manufacturing equipment, which is a critical step towards enabling the mass production of flexible displays. The FDC's bond/de-bond process with re-usable carriers adds minimal incremental cost, allows the use of a variety of high-performance plastic substrate materials, and has been proven up to Gen II scale at the FDC's pilot line, making it a leading candidate production technique as flexible electronics continue to evolve."
The Flexible Display Center is a government/industry/academia partnership that's advancing full-color flexible display technology and fostering development of a manufacturing ecosystem to support the rapidly growing market for flexible electronic devices. More information can be found at http://flexdisplay.asu.edu.
Universal Display Corporation is a leader in developing and delivering organic light-emitting (OLED) device technologies, materials, and services to the display and lighting industries. To learn more, visit www.universaldisplay.com.
SOURCE: ASU Flexible Display Center; http://flexdisplay.asu.edu/files/ovprea/FDC-UDC-PressRelease.pdf
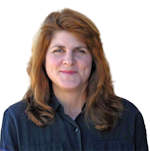
Gail Overton | Senior Editor (2004-2020)
Gail has more than 30 years of engineering, marketing, product management, and editorial experience in the photonics and optical communications industry. Before joining the staff at Laser Focus World in 2004, she held many product management and product marketing roles in the fiber-optics industry, most notably at Hughes (El Segundo, CA), GTE Labs (Waltham, MA), Corning (Corning, NY), Photon Kinetics (Beaverton, OR), and Newport Corporation (Irvine, CA). During her marketing career, Gail published articles in WDM Solutions and Sensors magazine and traveled internationally to conduct product and sales training. Gail received her BS degree in physics, with an emphasis in optics, from San Diego State University in San Diego, CA in May 1986.