3D laser time-of-flight imager uses adaptive MEMS to shift its 'attention' to different objects
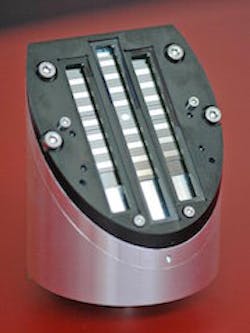
Researchers at the three institutes of the Fraunhofer-Gesellschaft in Germany -- the Fraunhofer Institute for Physical Measurement Techniques IPM in Freiburg, the Fraunhofer Institute for Intelligent Analysis and Information Systems IAIS in Sankt Augustin, and the Fraunhofer Institute for Photonic Microsystems IPMS in Dresden -- have combined laser time-of-flight (TOF) measurement and an adaptive MEMS microreflector component into a novel laser-scanning system.
The system is adaptive in that the image section with concentrated sensing can be quickly adjusted to the respective area of interest, just as the human fovea's photodetectors are concentrated at the center of vision. Software algorithms analyze a quickly recorded 3D overview image and direct the scanner (the "attention" of the system) to interesting image sections, so they can be scanned at a high resolution.
Fraunhofer IPMS was responsible for the scanning system concept, while Fraunhofer IPM provided the TOF laser measurement technology and Fraunhofer IAIS contributed the software development.
"The reflector mechanism of our laser scanner directs the time-modulated transmission beam over the object that is to be measured, says project manager Thilo Sandner. "The light of the transmission beam that is dispersed over that area is shown on a photodetector with a high bandwidth using several receiving reflectors that move synchronous to the beam, and the distance of the object is determined using the measured phase or pulse run time of the light that is received."
Pivoting 1D MEMS array
The scanning system concept is based on a 1D MEMS array that performs resonant scanning in a vertical direction, which can be pivoted and rotated with a conventional electrodynamic drive. The researchers were able to significantly increase the visual fill factor with the use of 22 receiving reflectors with individual apertures of 8.4 × 2.3 mm² and integrated-reflector position sensors, allowing measurements from distances of up to 30 meters.
Similar to conventional laser scanners, and in contrast to camera-based technologies, the strength of the laser-scanning technology is its ability to disregard the presence of different light conditions, an advantage especially for outdoors applications. The high scanning speed of the Fraunhofer scanner of 1.6 kHz makes it possible to scan images almost in real time, and thus it is also suitable for scanning moving objects such as airplanes on the runway or vehicles on construction sites.
The Fraunhofer Institute will present the novel microelectromechanical systems (MEMS) scanning microreflector components at Vision (Nov. 4-6, 2014; Stuttgart, Germany).
About the Author
John Wallace
Senior Technical Editor (1998-2022)
John Wallace was with Laser Focus World for nearly 25 years, retiring in late June 2022. He obtained a bachelor's degree in mechanical engineering and physics at Rutgers University and a master's in optical engineering at the University of Rochester. Before becoming an editor, John worked as an engineer at RCA, Exxon, Eastman Kodak, and GCA Corporation.