Industrial lasers have become commodities and high-power optical fiber connectors now work like wall plugs. Well, not exactly. Laser light cables will never get that simple, but a small company from Berlin, Germany has developed a new fiber connector concept that looks promising.
Recent years have seen the advent of industry-ready, high-power solid-state lasers, including fiber lasers. These lasers have taken over leadership in market numbers: after various technological improvements, they have become the undisputed standard tools in the biggest application fields for industrial laser systems—cutting and welding.
Besides the efficiency of these lasers, it is the opportunity to use glass fibers within flexible laser light cables that makes solid-state lasers so handy. “Plug and play” is more or less the promise of this technology for laser light delivery. Inside these connectors is sophisticated optomechanical technology that requires extreme precision. While a few connector systems have become standard in the field, none of them are perfect. Presented here is a new approach that has been developed based on extensive experience with existing fiber-optic laser light cables.
Requirements for high-power fiber connectors
It is tempting to compare laser light cables with electrical supply cords, but laser light is very much different from electrical current and so are the cables. In addition to continuous-wave (CW) power or pulsed energy, laser beams have properties such as beam shape, polarization, and spatial mode number that make their proper transmission much more challenging.
Some requirements for fiber connectors and cables are common sense: the valuable laser power should be transmitted to the processing head with the lowest possible losses of power and beam quality. The cable and connectors must not change the focus position or the beam pointing angle. And, of course, replugging should be possible without realignment of any component.
The next set of requirements is less obvious: the connector and cable have to comply with the specifics of the laser source. While both the connector and cable should tolerate different settings for a specific (class of) laser, it will not be possible to use the same cable for different types of systems such as a green and an infrared laser or an ultrashort-pulsed (USP) laser and a diode laser, even if they work at the same wavelength. Additionally, a fiber-continuity monitoring system (FCMS) must be included, and any mismatch and resulting discontinuity must be avoided by mechanical or electronic means.
This leads to the question of what can be done to maximize fiber durability. For example, inside the connector, the fiber can be protected with antireflection (AR)-coated end caps and optional additional protective windows. Incoupling of the laser beam into the fiber is tricky, too, so the manufacturer has to develop proper alignment, inspection, and cleaning techniques. Packaging and routing have to be ensured as well.
Last, but certainly not least, are demands from end users. Similar to laser sources, laser light cables and their connectors are commodities, so they have to be cheap. Even more important is 24/7 uptime for industrial laser applications such as car manufacturing. Fiber connectors need to be ready for easy system integration while complying with laser safety regulations. Finally, service and availability of spares and support over the product life cycle are important.
A new concept takes the best from current solutions
Historically, fiber connectors have been based either on a long cylinder or a cone that is plugged into the fiber socket (see Fig. 1). Some companies such as Optoskand (Mölndal, Sweden) and Trumpf (Ditzingen, Germany) have done fundamental development work on this technology—the designs are now available to any manufacturer. Both concepts can be seen as the current practice for high-power laser fiber connectors, while the cone concept exists in two embodiments (the “D” and the “QBH” standard) that have been more widely used since fiber lasers have entered into the industry.The cylinder connector needs a long and tight fit. If unplugged, it sucks a lot of air in and, as a result, eventually dust and moisture. Any little bit of dust inside the fit generates abrasion and more dust—additional seal rings collect dust as well. Experience in the field shows that the dust makes its way to the optics. Additionally, the tight fit over a long bore is prone to mechanical damages and wear. Sooner or later, this all leads to damage to optical surfaces and the need for replacement of windows or even cables.
The cone connector relies on two mating conical surfaces. Forcing them together in a tight fit has some effects. First, connector and receptacle require a high-precision manufacturing process—in addition, it is difficult to determine the reference optical axis with respect to the cone. The connector can start to move and wobble since the two mating cones will never be in a perfect match with zero tolerance. The countermeasure to this wobbling is brute force, in which the connector and receptacle are clamped together as tightly as possible. Even so, vibrations and acceleration, as from robots or gantry machines, can cause contact corrosion.
The new approach incorporates ideas from cylindrical as well as from conical connectors (see Fig. 2). It uses a cylindrical flange that is even shorter than the cone on the QBH connector. This short cylinder can be manufactured easily and gives any connection a tight and safe fit. For connection, the male part is simply screwed to the female part with four screws. A minimum of air is exchanged when unplugging this connector.With its centering flange, this connection offers a well-defined surface. The design can be easily customized to particular machine requirements—for example, electrical connections (such as FCMS) can be added and additional electrical signals can be transmitted. To keep the approach as simple as possible, electrical connectors have been kept at a minimum.
First application for ultrashort laser pulses
This connector design was developed by PT Photonics Tools for the transmission of ultrashort laser pulses. The requirements here are rather extreme: most of the systems are single-mode lasers, so the fitting precision of fiber couplers needs to be to within a few microns. The extremely high intensities of the ultrashort pulses create catastrophic damage in any conventional fiber—this problem was solved using special hollow fibers in which the pulses are guided mostly in air. These systems were introduced to the market in 2015. The new flange coupler has passed tests and become the solution of choice.Industrial automation and robotics provider Comau (Turin, Italy) has a strong presence in the automotive market (both traditional and electric), as well as in other industries. Together with Trumpf, Comau developed the first laser robots for automotive manufacturing—these were in high demand especially at General Motors in the 1980s. Now, Comau produces an advanced laser system that supports three major metalworking tasks—welding, brazing, and cutting—with one machine.
An example laser materials-processing system incorporating the new fiber-connector design was developed in a collaboration between several key players in the Italian laser community: Comau, Convergent Photonics (Moncalieri, Italy), and OPI Photonics (see Fig. 5). This machine contains a 6 kW diode laser and a 4 kW fiber laser. The diode modules can be used to pump the fiber laser, which creates substantial savings compared to working with two separate systems. The user simply plugs fiber cables into the appropriate ports and uses either the diode laser (with a beam parameter product, or BPP, of 66) for welding and brazing, or the fiber laser with its fine focus (BPP of 6) for cutting.Beam switching internal to the system required careful engineering—several beamsplitters and mirrors are moved to supply fiber or diode laser radiation to the outlets. The system needed a simple and cheap solution for the internal beam connectors, and the new flange fiber connector was chosen for this purpose. The main argument for this choice was the simplified connection and lower costs. The laser system has since been extensively tested and has been sold to first customers.
PT Photonics Tools is sharing interface details of the new fiber-connector concept with all interested parties.
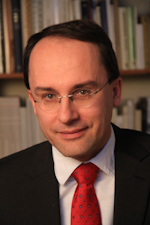
Andreas Thoss | Contributing Editor, Germany
Andreas Thoss is the Managing Director of THOSS Media (Berlin) and has many years of experience in photonics-related research, publishing, marketing, and public relations. He worked with John Wiley & Sons until 2010, when he founded THOSS Media. In 2012, he founded the scientific journal Advanced Optical Technologies. His university research focused on ultrashort and ultra-intense laser pulses, and he holds several patents.
Björn Wedel | Founder and CEO, PT Photonic Tools
Björn Wedel is founder and CEO of PT Photonic Tools (Berlin, Germany).