Photonics Products: Specialty Fibers: Fibers for sensing extend their reach
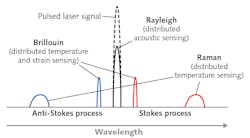
As opposed to telecommunications fiber-optic systems, which are designed to minimize the influence of the surrounding environment on light propagation through the fiber, a fiber-optic sensing system is simply doing what it's supposed to when its performance is affected by its surroundings.
Fiber-optic systems used for sensing can measure environmental influences such as temperature or strain either continuously along the fiber, or at discrete points defined by fiber components. Other types of fiber sensors can measure physical movements such as rotation, as in a fiber gyroscope. The ruggedness and narrow physical path of optical fibers make them ideal for use as sensors in harsh and remote environments.
Remote sensing along a fiber path
An optical fiber can be inserted or embedded along a path—whether it is meters or kilometers long—that is determined mostly by what the sensing system's attendant scientists and engineers want to sense, rather than by limits on the sensing hardware itself.
For example, Nufern (East Granby, CT) offers a range of fibers (the NuSENSOR product line) that can sense temperature, strain, pressure and flow by employing one of three main effects—namely Raleigh, Brillouin, and Raman scattering (see Fig. 1). "Fiber-optic sensors based on these fibers are not only replacing traditional electronic point sensors, but are providing the much desired temperature and strain profiles through distributed sensing," says Daniel Hennessey, technical manager at Nufern. "Laser signals are sent down these specialized fibers that can be kilometers or even tens of kilometers long; the local light scattering, which is affected by the local environment, is measured and a time-of-flight analysis is conducted to precisely determine both the local value of the measurand."
Hennessey notes that electronics and signal processing along with stringent optical-fiber parameters enable users to get sub-1-m resolution along the length of the optical fiber. The sensor fibers are specialized both in the optical waveguide design and glass composition as well as in the specialized polymer coatings, which include high-temperature acrylates, silicone, and polyimides, and even metal coatings such as aluminum and gold that provide added capabilities for the fiber to withstand harsh sensing environments.
As Abdel Soufiane, founder, president, and CEO of Verrillon, an AFL company (Duncan, SC) describes, fiber-based remote sensing can either be done continuously along a fiber via various processes, or at particular points using, for example, fiber Bragg gratings (FBGs). Verrillon offers both multimode (VHM series) and single-mode (VHS series) fibers for harsh-environment sensors. These fibers can be used to sense temperature, the presence and magnitude of acoustic waves, or strain.
"Distributed temperature sensing (DTS) consists of an optical fiber installed in the area where the distributed temperature is to be monitored," says Soufiane. "A laser pulse is launched in the fiber, and as the light pulse propagates along the fiber, it energizes the glass, lattice structure, and molecules and causes a portion of the light to be scattered back to a detector. The main backscattered wave is at the wavelength of the launched pulse and is called the Rayleigh band. This is by far the strongest signal returned. The other waves associated with the lattice vibrations show up as Brillouin and Raman peaks on the backscatter spectrum. These peaks are called 'Stokes' and 'anti-Stokes' signals. Raman DTS is the most used for temperature measurement, as the anti-Stokes peak is strongly temperature-dependent and is the one used to measure temperature at every point of the fiber length. Any change in the intensity of the anti-Stokes peak corresponds to a change in temperature. The Stokes peak is not sensitive to temperature and is typically used for calibration."
In a related manner, distributed acoustic sensing (DAS) consists of injecting a pulse of light in an optical fiber. A small amount of the light is naturally backscattered (through Rayleigh, Brillouin, and Raman scattering) and returns to the sensor unit, Soufiane explains. The nature of this scattered light is affected by small strain events within the optical fiber structure, which themselves are determined by the localized acoustic or seismic environment. By recording the returning signal as a function of time, a measurement of the acoustic field all along the fiber can be determined.
Finally, distributed strain sensing (DSS) uses Brillouin backscattering, which is sensitive to strain (and temperature) changes corresponding to intensity changes of the Brillouin peaks, says Soufiane. "The challenge of the Brillouin sensing method is that the strain and temperature have to be decoupled to have accurate reading of one or the other," he adds. For DSS, Verrillon's single-mode VHS fiber series is especially useful, he notes.
The other approach to fiber-based remote sensing is the use of discrete sensors. To create such a sensor, FBGs can be created in the fiber core of Verrillon's VSS200 photosensitive SM fiber by exposing it to UV light, which creates a refractive-index modulation in the fiber core, according to Soufiane. In use as a remote sensor, "the FBG selectively rejects one wavelength, and by interrogating the specific FBG, the position and the temperature information can be extracted. The FBG-array sensing technique is not fully distributed, but is 'quasi-distributed' depending on the spacing between two neighboring FBGs," he says.
Use in oil and gas wells
A prime example of using optical fiber to sense along a path is the measurement of temperature and other parameters deep under the earth along the trajectory of an oil or gas well.
"Distributed temperature sensing for oil exploration embodies a real-world application for fiber-optic sensing," says Hennessey of Nufern. "As the worldwide demand for energy continues to increase, efficient recovery of oil from both traditional as well as nontraditional sources such as shale oil and heavy oil sands has become a necessity. Enhanced oil recovery methods such as cyclic steam stimulation (CSS) and steam-assisted gravity drainage (SAGD) are being used, where high-temperature steam is used to heat and reduce the viscosity of the crude to facilitate flow and extraction. Continuous monitoring of the well temperature profile to get active feedback for process optimization has become essential."
Distributed fiber-optic sensing provides the capability to get real-time temperature monitoring with 1 m resolution over lengths as long as 10 km, Hennessey adds. "However, high well temperatures of 250–300°C or higher, high hydrogen partial pressures, and corrosive chemical environments put significant demands on the optical fiber," he explains. "Specialized optical coatings are required that can withstand the high temperature and corrosive environments, while the glass has to be engineered to be resistant to hydrogen darkening. In some cases, depending on the deployment conditions and application needs, special coatings may have to be applied to the glass to improve its dynamic fatigue strength."
Nufern's GR-S50/125-20CP is a good case study when trying to understand fiber-design elements that address the stringent demands of distributed temperature sensing for oil exploration and recovery, notes Hennessey. "This fiber has a 50 μm graded-index core with a numerical aperture (NA) of 0.2," he says. "The graded-index core provides a bandwidth of at least 300 MHz-km, which is needed to achieve a spatial resolution of 1 m or less. The core glass composition is essentially pure silica with fluorine co-doping to achieve the index grading and has no traditional dopants such as germanium and potassium. Such a core composition is designed to make the glass resistant to hydrogen darkening.
He explains that the fiber's carbon coating is hermetic up to 150–200°C (after which the rate of diffusion of hydrogen through carbon increases rapidly); in addition the carbon coating raises the dynamic fatigue strength of the fiber. "The polyimide coating enables use of the fiber up to 300°C and even up to 350°C for modest durations of time," he says. "Nufern's polyimide coating is also chemically resistant to fluids that the fiber may get exposed to during oil exploration and recovery application."
Verrillon's Soufiane also notes that, in applications such as oil production, hydrogen is usually detrimental to DTS measurements. "Our VHM5000 fiber has been created by modifying the glass chemistry of the fiber core, making it immune to hydrogen darkening," he says. As shown in Fig. 2, the 1064 nm wavelength, which according to Soufiane is the most widely used in DTS, is not affected by hydrogen ingression, allowing for an accurate measurement of temperature without hydrogen-induced attenuation errors.Fiber gyroscopes go to Mars
One longtime application of optical fibers for sensing is in fiber-optic gyroscopes (FOGs), which are used in aircraft, missiles, and unmanned autonomous vehicles (UAVs).
"Fibers for FOGs help measure the Sagnac effect, where counterpropagating beams are launched into a highly precisely wound coil of polarization-maintaining fiber such that, if the coil does not rotate, then the phase differential of the two beams will be equal to the differential at the input point," says Andy Gillooly, technical business development executive at Fibercore (Southampton, England). "As the coil rotates, one direction of travel for the light effectively propagates along a longer path length, while the other direction sees a shorter path length. At the output, this is observed as a change in the phase differential between the two directions of propagation."
As the technique ultimately uses an interferometric analysis method, maintaining a high polarization-extinction ratio (PER) along the length of the fiber is essential for high accuracy results, notes Gillooly. At Fibercore, this is achieved through the company's "bow-tie" core design. "Such fibers can be found in FOGs within many of the world's major airliners, assisting with stabilization of the aircraft; they are also used for submarine navigation, turret stabilization, and attitude control within satellites," she adds. "One of the most extreme uses has been the inclusion of this fiber on all three of the Mars rovers, and is still operating today."Nufern also offers optical fibers especially tailored for FOGs, including a radiation-hardened version (see Fig. 3). The company's NuGYRO line of fibers is designed to very precisely sense rotation and current when used in a Sagnac interferometer. In addition, Nufern has a coil-winding service in which it winds a fiber in a quadrupole pattern, which reduces errors associated with thermal gradients and vibration.
As well, Verrillon has a line of fibers for FOGs, including polarization-maintaining (VPM) and single-polarization (VPZ) fibers. These fibers maintain their polarization based on the mechanical stress created in the fiber's elliptical cladding, notes Soufiane (see Fig. 4).An abundance of sensing applications
In addition to fibers for FOGs, Fibercore manufactures specialty optical fibers for a variety of sensing applications that include Faraday effect current sensors (also known as optical current transformers), hydrophones, 3D shape sensors, and FBGs for temperature, strain, pressure, and haptic sensing, according to Gillooly.
"Optical current transformers sense magnetic fields induced by electrical current such that polarized light traveling perpendicular to the electrical current and along the path of the magnetic field will observe a Faraday rotation of the polarization state [see Fig. 5]," she says. "By measuring the magnitude of rotation, the electrical current can be measured to high accuracy. This enables current sensors to be manufactured from nonelectrically conductive materials that can be used for metering and protection of the power-distribution grid."Sensor fiber for fiber-optic current sensors, known as spun fiber, displays some of the toughest requirements for an optical fiber, says Gillooly. The fiber must be designed to maintain a circular polarization state, yet still be sensitive to the Faraday effect. This ultimately points to an optical fiber design that is initially a polarization-maintaining fiber, but that exhibits a continuous spin of the fiber along its length. The spin creates a helical path in the bow-tie stress in the core region, ultimately creating the required circular birefringence.
As the sensor system uses an interferometric sensing technique, maintaining a circular core is essential to avoid reflections at splice points, which create unwanted noise within the system. "Then, to ensure the fiber is suitable for extreme operating environments anywhere from Siberia to the Sahara, the coating of the fiber needs to be stable over the expected operating temperature range," says Gillooly. "The introduction of the new HardShell optical fiber coating package ensures intelligent design of the coating materials and ways that they are processed to create a mechanically protective shell around the optical fiber, which distributes externally applied stresses around the surface of the coating without transfer to the glass core. The core of the fiber is typically optimized for operation around 1310 nm, giving a balance between telecom-style optical components (and prices) and the wavelength-dependent magnitude of the Verdet constant which defines the sensitivity to the Faraday effect-shorter wavelengths are more sensitive."
With all of these pieces in place, the fiber is then suitable for mass roll-out into power distribution grids either as a retrofit component or as part of newly built systems, explains Gillooly. The optical design of such a current sensor means that the sensor head does not require large amounts of electrical shielding that are used in the existing products, enabling significantly smaller package sizes and reduced costs. The high-speed sensing ability of an optical technology also makes it highly suitable for grid protection, enabling extremely fast detection of power spikes to trigger circuit breakers and thus prevent brownouts.
As for hydrophones (which detect sound underwater), Gillooly notes that such devices have been shifting towards fiber-optic technology over the last decade because of its higher reliability in comparison with electrically powered hydrophones. Fiber for a hydrophone is designed to be coiled and packaged into a very small space, where approximately 20 m of fiber is coiled onto a mandrel that expands and contracts as the pressure wave from an acoustic signal is incident on the mandrel. The fiber stretches and contracts with the mandrel's movement, which, if matching FBGs are mounted on either side of the coil, results in a highly sensitive interferometer, says Gillooly. The interferometric response can then be analyzed many kilometers away. Such hydrophones find use in towed arrays and permanent reservoir monitoring systems for oil and gas exploration and extraction process optimization, as well as detecting submarines for coastline security.
3D shape sensing
One of the most-complex forms of fiber sensing technology is the ability to sense, in 3D, the path of an optical fiber through space. "3D shape sensing presents a revolutionary technology in which every centimeter of an optical fiber can be analyzed to know exactly where it sits in a 3D shape," says Gillooly. "Fibercore's 3D shape-sensing fiber is made up of between 4 and 7 cores, with the path of the cores following a spiral path along the length of the fiber. Either through the analysis of Rayleigh scatting or the stress effects on FBGs, the exact shape of the optical fiber can be inferred. This allows monitoring of the bend in the X and Y directions, rotation clockwise or anticlockwise, and longitudinal extension or compression.
Gillooly notes that such technology is making an impact on minimally invasive surgery, where existing technologies use continuous x-rays during surgical procedures to help guide and locate catheters. Through use of the 3D shape sensing technology, the x-rays are not required, reducing the need for the patient to be exposed to radiation and removing the need for the surgical staff to wear heavy protective clothing.
For More Information
Companies mentioned in this article include:
Fibercore
Southampton, England
www.fibercore.com
Nufern
East Granby, CT
www.nufern.com
Verrillon (AFL)
Duncan, SC
www.aflglobal.com/products/specialty-optical-fiber.aspx
For a complete listing of companies making specialty fibers, visit the Laser Focus World Buyers Guide (https://www.laserfocusworld.com/directory).
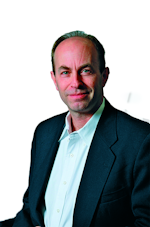
John Wallace | Senior Technical Editor (1998-2022)
John Wallace was with Laser Focus World for nearly 25 years, retiring in late June 2022. He obtained a bachelor's degree in mechanical engineering and physics at Rutgers University and a master's in optical engineering at the University of Rochester. Before becoming an editor, John worked as an engineer at RCA, Exxon, Eastman Kodak, and GCA Corporation.