Components for Fiber Optics: Advanced manufacturing techniques benefit fiber-optic components
Continued advances in optical fiber processing technologies and new research into the field of specialty fibers have helped to create a new generation of fiber-optic components. With the advent of very high precision glass-processing platforms, the fiber-component field has moved from the confines of independent and academic laboratories to the use of commercially available machines with either specific or universal capabilities.
Task-specific machines are available today that can be used for the unique purpose of forming a ball lens or using a carbon dioxide (CO2) laser to ablate fiber to form an axicon lens (a lens with a conical shape). In addition, universal machines have been developed that are capable of several types of tasks such as splicing similar and dissimilar fibers, forming lenses, tapering, manufacturing fiber combiners, and performing component processes that have yet to be revealed to the general public.
It should be noted that without the development of this new era of equipment, the ability to make these components in mass production would still pose many challenges. Although there is a broad spectrum of components in this field, this article will be limited to the following fiber-component technologies: fiber-lensing techniques, endcap technology, tapers, multicore-fiber fan-outs, fiber combiners, mode-field adapters, and overcladding.
Lensing technologies
Today's technologies enable the formation of many lens shapes from optical fiber. For example, axicon lenses are used to increase the efficiency of coupling lasers and LEDs into fibers at the chip level, while ball lenses are used in the medical field for the purposes of detecting cancer and destroying kidney stones.
The axicon lens has typically been produced by either polishing the tip of the fiber with a special polishing process or by using a CO2 laser to obliterate the fiber end to remove the cladding material in a conical shape (see Fig. 1). Fabrication changes the properties of the end of the fiber, exposing the core, which is then surrounded by air rather than cladding material. The difference in refractive index between the air and glass is substantially different than the difference in index between the core and cladding. Additionally, the conical shape produces a lensing effect at the tip of the fiber, enabling the collection of more light into the fiber from an LED or laser diode.
The polishing process used to create an axicon on the end of a fiber, while effective, is also very labor-intensive. The fiber must be held at a very precise angle and rotated while the polishing materials remove a relatively large amount of cladding material. In comparison, the production of ablated axicon lenses are produced on highly automated systems, which typically take longer to load and unload than the time required for the laser to create the lens. Both these axicon lens manufacturing methods produce very similar looking and performing components.
The tapered axicon, by contrast, is produced by heating and drawing the fiber to an abrupt tip. Although the conical lens shape is formed at a much less steep angle, its optical performance is almost exactly the same as for the other two manufacturing techniques. The typical difference with this design is that the core of the fiber is drawn down at the same time as the cladding, as opposed to the other techniques in which the core size is unchanged. However, the reduced core diameter appears to have no effect on the beam quality, as the light at the tip will be guided by the cladding/air interface. The benefit of this technique is that it can be produced on typically any of the specialty splicers on the market today, which enables production via a very cost-effective process.
Ball lenses (see Fig. 2) can be produced using several methods, with the most common being the splicing of a coreless fiber onto the existing launch fiber, then forming the ball at a fixed distance from the end of the launch fiber. Coreless fibers are preferred, as the index of refraction throughout is then uniform and produces an undistorted beam. If coreless fibers are not used, then the core and cladding index materials can intermingle, leading to an inconsistent and poor-quality output beam.The size of the ball and its distance from the point at which the beam begins to diverge into the coreless fiber can be constructed in such a way as to create a converging, diverging, or collimated beam exiting the ball. Several other postprocessing techniques can be done on the ball such as depositing antireflection (AR) coatings and/or polishing a reflective flat to produce a beam that exits from the side. The balls can be mounted in expanded beam connectors to minimize losses and to allow for the addition of external optical elements into the beam path.
The simplicity of ball-lens production allows it to be fabricated using either specialty fusion splicers or machines designed for the specific purpose of making a ball lens. Fortunately, ball-lens production is aided by the physics of the surface tension of the molten glass. As the fiber is heated and fed into the heat source, the glass naturally forms a perfect sphere as the surface tension draws the molten fiber around the fiber end.
Endcap technology
The emergence of higher-powered fiber lasers over the last few years has led to advances in endcap technology. The energy density at the output end of a fiber laser can be extremely high, but with the use of an endcap, this high-density energy can be allowed to diverge in a controlled manner. As the laser light emerges from the endcap, it is refocused onto the work surface using free-space optics.
The challenge with these devices is that the endcap diameter can be extremely large compared to the diameter of the fiber; it is not uncommon for the endcap to be as much as 4 to 8 times larger than the actual fiber output end from the fiber laser (see Fig. 3). This large size can pose a challenge for some of the heating methods used to fuse the fiber to the endcap.When electrical-arc and filament fusion splicers are used, great care must be taken to manage the heat distribution of the much smaller glass fiber with respect to the larger endcap. The energy required to get this larger endcap to the molten phase typically vaporizes the smaller-diameter fiber. This effect is compensated by offsetting the endcap into the heat source.
The one exception to this chain of events occurs when a CO2 laser is used as a heat source. In this case, the CO2 laser works through absorption of the photons by the silica, an effect that is proportional to the surface area and thermal mass of the object being heated. The endcap has a much larger thermal mass surface area than the smaller fiber being connected to it; therefore, the two fibers heat at roughly the same rate when exposed to the energy from the CO2 laser. All these heating methods would benefit from a lead-in on the launch side of the endcap in order to reduce the heat-sinking effect caused by the larger mass of the endcap.
Tapers
Fiber tapering has several applications: for example, mode-field adapting to minimize splice loss; combiner production to increase the power in a fiber; and creation of evanescent-wave fiber sensors, which detect the interaction of an external material via the evanescent wave that exists closely around a severely tapered, very-small-diameter fiber. Adiabatic tapering of a fiber ensures that the light remains confined within the core/cladding or cladding.
With most of the available equipment, it is possible to attain a 10-to-1 taper ratio in a single pass with the two translation stages holding the fiber traveling in the same direction. One important specification for either the universal equipment available today or the specialized tapering machines on the market is the linear travel of the fiber stages. Some fiber tapers require up to 150 mm of stage travel to be produced. Thus, when selecting fiber-tapering equipment, be sure that the stage travel is long enough to meet the requirements of the device being produced.
Multicore fiber fan-outs
Multicore fibers (MCFs), a recent development in the fiber industry, are being used for both sensing applications and for increasing the data-transmission density of a single fiber for long-haul applications. One challenge for these fibers is the launching and retrieving of signals into and from the individual cores. MCF fan-outs provide the ability to do just that.
A multicore fiber fan-out contains a bundle of fibers matching the number of cores in the multicore fiber. The fibers are tapered until their core spacing matches that of the MCF. This composite structure is then cleaved and spliced onto the end of a multicore fiber, thus providing a method to access the individual cores at both the input and output ends of the MCF.
The critical concern for the production of these devices is the core alignment, which must be maintained down to a submicron scale. Accomplishing this feat requires a very uniform heating and tapering process to insure that the taper is adiabatic and that the core spacing remains uniform.
Fiber combiners
Fiber combiners are commonly used to provide laser-diode pump energy to fiber lasers. By tapering several fibers together, the energy from the pump diodes can be combined into a single fiber and spliced to the active fiber to create a lasing cavity. There are several different combiner designs, and each of them has the same goal: to get the largest amount of light into the lasing cavity with the least amount of loss.
Equipment is readily available that can produce reliable and repeatable fiber combiners. Great care must be taken in the production of these combiners; one must ensure that they are adiabatic in design and free from all contamination, as the amount of energy traveling down the combined fibers is sensitive to both of these characteristics. High localized loss can be catastrophic to a fiber laser; if the energy in the fiber escapes from a pump combiner as a result of being nonadiabatic or as a result of contamination, the typical result is overheating at that location. These types of failures are often not recoverable and require rework or replacement of the fiber-laser assembly.
Mode-field adapters
Mode-field adapters modify a fiber's optical properties to match the fiber to which it is being spliced, lowering the loss at the splice point. This can be accomplished in one of two methods: 1) the larger core can be tapered down to match the smaller core size or 2) the smaller core can be expanded by heating it before or during the splice. In the most extreme example, splicing a single-mode fiber to a multimode fiber will typically induce 20 dB of loss when going from the multimode to the single-mode fiber; using MFAs, it is possible to lower this loss to below 1 dB. Most of today's specialty splicers have this capability.
Overcladding
Overcladding is the process of placing a fiber into a capillary tube and collapsing the tube until it fuses with the fiber. Figure 4 shows overcladding used on a fiber combiner. This process can also be used to provide a hermetic seal between a fiber and a capillary tube.One of the more interesting uses of overcladding is to combine it with an inverse-tapered fiber. It is possible to increase the core numerical aperture of the fiber over a short distance by reversing the taper process; after creating this up-taper, the fiber is cleaved in the expanded region. The expanded fiber is then placed in a capillary tube and the tube collapsed to create a hermetic seal. High-energy light can then be launched into the larger core-diameter region that has been created. In the taper, the core adiabatically reduces to its normal size, preventing substantial energy loss.
Many companies in the fiber industry have been fabricating specific discrete components for over 30 years; most of that work was done on customized, proprietary equipment. As a result of the recent developments in specialty splicing and glass-processing equipment, we have seen numerous advances in the capabilities of fiber-optic components. The high-precision fabrication equipment now readily available makes the production of ever-more-complex fiber-optic components easier, a situation conducive to innovation in the industry.
Mike Harju | Application and Process Development Manager, AFL
Mike Harju is application and process development manager at AFL (Duncan, SC).
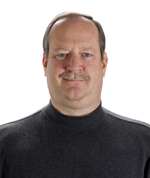
Brad Hendrix | National Sales Manager for OEM
Brad Hendrix’s career in fiber optics spans nearly 25 years. He currently serves as AFL’s national sales manager for OEM. In this capacity, Brad determines marketing and sales strategy for high end splicing, testing cable and connectivity applications in the industrial and university markets as well as oil and gas industry. This role exposes Brad and his team to some of the most difficult and interesting glass processing problems in the fiber optic marketplace.
Brad began his career in fiber optics in 1987 working at the Alcoa Technical Center on embedded fiber sensors in composite materials. He joined AFL in 1989 and has worked in many fiber optic product and business development areas within AFL including Sensor Systems working with PM fibers, optical couplers, WDMs and fiber management solutions.
Brad holds degrees in Computer Science, Laser Electro-Optics and Physics.