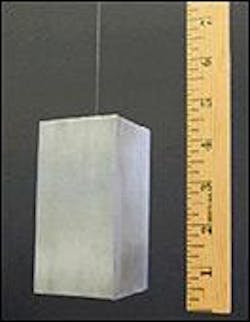
Used almost universally to bond electronic components to circuit boards or to each other, solder has desirable properties apart from its electrical conductivity: it solidifies in seconds, and has the rigidity of metal. In contrast, the epoxy and other cements used to affix optical fiber to optoelectronic components can take up to a day to cure and must be deposited in thin layers to avoid creep. Conventional electronic solder cannot replace cement for these applications because it bonds poorly to oxides such as silica. Although nickel-plating optical fiber permits solder to adhere to it, the plating process is an expensive and time-consuming extra step. Researchers at Agere Systems (Murray Hill, NJ) have developed a solder specifically for optoelectronic use that bonds directly to glass at high strength.1 The lead-free solder contains a small amount of the rare-earth element lutetium (Lu) to promote the formation of chemical bonds.
The solder can have either a tin silver or tin gold base. Anywhere from 0.5% to 2% Lu is added. To make the alloy, the researchers melt the base, heating it to 500°C to 800°C, and lower in a piece of Lu foil. Although Lu itself has a low melting point, it oxidizes when heated, forming a surface layer that melts at 2410°C, preventing the combination of the foil with the base mixture. To avoid this problem, the researchers mix the substances in an evacuated silica tube. The Lu is mounted to a tungsten wire attached to a magnet; at the proper moment, another magnet outside the silica tube is slid downward, propelling the Lu foil to its fate.
Upon solidification, the result is 5-μm-sized blobs of Lu dispersed throughout the base. During soldering, the Lu dissolves in the melted metal. When the solder comes into contact with a silica optical fiber, some Lu migrates to the solder-fiber interface, reducing the amount of silica in contact with the other metals. The Lu itself bonds strongly to glass (see figure).
Creep-resistant solder that binds to optical fiber has a variety of potential uses. A single-mode fiber pigtail carrying light from a laser diode must be aligned to the laser to within a micron or better; solder can fix the fiber in place quickly and rigidly. The spectral properties of optical fiber gratings vary with temperature; by bonding a stretched fiber grating at two points to a substrate having a properly chosen negative thermal expansion coefficient, the wavelength dependence of the grating will be minimized. Assembly of more-complex optoelectronic devices such as wavelength-tunable fiber-grating filters may benefit from the quick-setting bond offered by Lu-containing solder.
The solder developed at Agere is not restricted to use with fused silica; it can also bond silver to sapphire, aluminum to amethyst, gold to diamond, and platinum to turquoise, among other combinations. The researchers are still in the process of bringing the solder into full practical use, according to Ainissa Ramirez, a research scientist at Agere. "It is foreseeable that various processes [proportions and types of metals] would have to be developed for each application, but do not expect any show-stoppers," she notes.
REFERENCE
1.A. Ramirez et al., Appl. Phys. Lett. 21 (January 2002).
About the Author
John Wallace
Senior Technical Editor (1998-2022)
John Wallace was with Laser Focus World for nearly 25 years, retiring in late June 2022. He obtained a bachelor's degree in mechanical engineering and physics at Rutgers University and a master's in optical engineering at the University of Rochester. Before becoming an editor, John worked as an engineer at RCA, Exxon, Eastman Kodak, and GCA Corporation.