OPTOELECTRONIC APPLICATIONS: MATERIALS PROCESSING - New technologies heat up the laser-welding market
When Laser Focus World looked back at the early years of the laser during our 40th anniversary in 2005, laser welding was noted as one of the most obvious of possible uses (see www.laserfocusworld.com/articles/234079). But in his 2007 market forecast for industrial lasers (see www.industrial-lasers.com/articles/316170), David Belforte, editor-in-chief of Industrial Laser Solutions, reported that laser welding accounted for only 12% of the worldwide industrial laser applications by units, or roughly $206 million of the $1.72 billion dollars in total industrial laser sales for 2007.
Market penetration
Reasons for the slower adoption of laser welding compared to cutting, machining, microprocessing, and marking applications continue to be debated. “Only those applications that can take advantage of one or more of the features of laser beams, such as high precision, low heat input (low distortion), deep penetration, and fast speed are particularly suited to laser welding,” says Geert Verhaeghe, principal project leader in the Technical Laser and Sheet Processes Group at TWI (Cambridge, England), a welding research, consultancy, and training services company. “Our laser group is often asked to advise on or demonstrate a change from an arc process to a laser process. The message is always that the process should be considered in its entirety; often the design of products needs to be modified to fully make use of the advantages lasers can offer.”
Further, Verhaeghe‘s says, “Industrial uptake of laser welding was limited for a long time because of its stringent joint fit-up requirements.” That is, the smaller spot size from laser welding requires close proximity of the parts to be joined. “Laser welding is not a problem for high-precision gear-to-shaft welds, but is more difficult for large meter-long 8-mm-thick plates to be butt-welded together. Various techniques exist to compensate, including filler (use of solders), twin-spot (splitting the beam with optics to increase weld coverage), and weaving (wiggling the beam along a seam), but I‘m a big supporter of hybrid laser-arc welding that takes advantage of both processes—the speed of laser welding and the large weld pool from arc welding.”
Verhaeghe believes there is no secret cost/volume formula that manufacturers can apply to ensure the economic viability of laser versus traditional welding. “We often do a techno-economic comparison for our customers prior to investment,” he says. “This takes into account a range of factors that can affect the running cost: laser source, cooling, maintenance/servicing, manipulation, jigging, and consumables.” But he notes that it is more difficult to assess the “secondary” advantages gained from having less distortion and less rework/repair—often the most positive benefit of a highly repeatable laser-welding process.
Market penetration is also a function of geography. “Europe continues to lead the industry in adoption, as well as supply, of laser-welding equipment,” says Archana Chauhan, Frost and Sullivan senior research analyst. Geoff Shannon, laser product manager at Miyachi Unitek (Monrovia, CA), offers some insight. “There is still a distinct lack of laser-welding awareness across all industries,” says Shannon. “Europe has a strong laser market and it is no coincidence that Europe probably has an order of magnitude more educational and research institutes dedicated or offering laser processing, and welding in particular.”
Proven applications
Laser welding has replaced resistance spot welding for riveting of aircraft fuselage structures at companies such as Airbus, and has been adopted at automobile manufacturers including Audi, BMW, and Volkswagen, and several European shipyards. Meyer Werft (Papenburg, Germany), active in the cruise vessel and ferries market, is using laser and laser hybrid welding for steel sandwich panels in combination with conventional stiffened panels. Cruise ship and ferry manufacturer Aker Yards (Finland) uses hybrid laser-metal arc gas (MAG) welding for fabrication of flat panels. Shipbuilder Blohm+Voss (Hamburg, Germany) uses lasers for welding, as well as for cutting and primer removal of conventional stiffened panels. And Odense Steel Shipyard (Odense, Denmark) also uses lasers in a multipurpose format for welding, cutting, primer removal, and marking of steel subassemblies for freight containers.A common thread in many of these applications is the use of lasers for tasks above and beyond welding, such as cutting and marking. If the laser can do double or even triple duty in a particular application, its value proposition is dramatically increased. For example, automaker Daimler (Sindelfingen, Germany) uses scanning optics or so-called “remote welding” to direct a stationary beam along a weld seam or to split a single laser into multiple beams for multiple purposes (see Fig. 1; see also www.industrial-lasers.com/articles/330516 and www.industrial-lasers.com/articles/228106). Holger Schubert, project manager in Production and Materials Technology at Daimler, says that the scanning optics process can reduce production times by almost 80% compared to traditional resistance spot welding. And because automobile components can be spot-welded using smaller laser-beam diameters compared to conventional welders, large joining flanges are not necessary, enabling individual automotive components to be smaller and lighter.
Despite the dominance of laser welding for “macro” or large-scale industrial processing, laser welding also plays a role in microwelding—precision welding of smaller, precision parts and miniature optoelectronic components (see Fig. 2). “Microwelding generally corresponds to welds with a penetration depth less than 1 mm,” says Shannon at Miyachi Unitek. “The medical market is probably where the most growth has occurred—with parts that have good fit-up and material control, the medical industry is well suited to laser welding. Typical applications are welding tool tips for medical instruments, seam-sealing implantable devices, guide-wire welding, and fine-wire attachments.”
Microwelding is even playing a role in the jewelry industry. “Most Nd:YAG jewelry laser welders operate in the 35 to 300 J range with beam widths adjustable from 0.2 to 2.0 mm,” says Steve Satow of Satow Goldsmiths (Henderson, NV). “I do laser training for jewelers and it‘s a bit of a learning curve to hold something so steady freehand that you can weld it accurately down to 0.2 mm. But I was hooked when I found I could replace prongs on platinum mountings without removing the stones—a monumental cost savings.”Beyond metal
While lasers are obvious replacements for conventional welding techniques when joining two metals, the laser‘s greatest advantage may lie in the joining of plastic, polymer, and other nonmetal materials traditionally joined with heating elements or through ultrasonic processes (see Fig. 3). One example is the Clearweld process, patented by TWI and licensed to Gentex (Carbondale, PA), a manufacturer of optoelectronic-based devices. The Clearweld process uses near-IR-absorbing welding materials (which can be applied as coatings or incorporated into resins used for molding the parts) to convert laser energy into heat for high-quality welds. Gentex says the advantages are high weld speeds, optically clear joints, elimination of visible markings, reduced thermal distortion, rapid changeover to different products, and simultaneous welding of multiple layers.
In addition to welding clear plastics using the Clearweld process, as well as tackling more challenging ABS-type plastics, bielomatik (New Hudson, MI) typically uses fiber lasers for some of its most rigorous applications (see www.industrial-lasers.com/articles/270904).
Laser welding is also being explored for the joining of textiles in water-proof clothing and upholstery applications. The two-year, European Community (EC)-funded Automated Laser Welding for Textiles (ALTEX) project performed joining of three-layer laminated materials with polyester face, nylon back, and a breathable membrane, as well as polyurethane-coated materials and bi-adhesive laminated materials using a 75 W, 940 nm, six-axis automated laser-diode welding system. Project coordinator Ian Jones says that high-integrity seams were made at speeds four times faster than manual stitching, exceeding current industry requirements for resistance to water penetration and wash-test survivability. The ALTEX project ended in December 2007, but the work continues under the European Union‘s LEAPFROG project (see www.leapfrog-eu.org).
Laser welding has even moved into textiles. The TexWeld Duo, offered by ProLas (WÜrselen, Germany), is a two-laser welder that combines direct and transmission welding with ultrasonic welding and integrates the fabric joining process with continuous seam welding for clothing, container bags, and industrial textiles.
New sources, better welding
Although CO2 and YAG lasers have dominated the laser-welding market, changes are under way. “The last five years have seen a revolution in high-power laser technology,” says Verhaeghe. “Multikilowatt fiber lasers became available sometime in 2003 and I was fortunate enough to be responsible for the installation and commissioning of a 7 kW ytterbium fiber laser early in 2004. The system had a beam quality better than 20 mm mrad, which was then seen as fantastic; the rapid change in technology reminded me of the pace of personal computer development.”
Current YAG laser technology offers beam quality of around 25 mm mrad; however, today‘s fiber lasers easily achieve power levels of 5 kW up to 50 kW, with beam qualities as small as 2 mm mrad. Verhaeghe describes how the threat of fiber lasers spurred on the development of the disk laser, which offers improved heat dissipation and beam qualities of around 7 to 8 mm mrad for an 8 kW device (see www.laserfocusworld.com/articles/330691). “One could say that fiber and disk lasers are the next-generation Nd:YAG lasers,” says Verhaeghe. But with the search for even more efficient lasers, Verhaeghe adds that there is a lot of buzz about direct-diode lasers, which compensate for shortcomings in beam quality by offering lower cost, easy fiber delivery, and power conversion efficiencies of 40% or more, compared to 30% for fiber lasers and only 3% to 5% for YAG lasers.
Precision welding and cladding subcontractor Joining Technologies (East Granby, CT) says that its Trumpf 2 kW disk laser, integrated with a five-axis welding workstation, performs deep-penetration welds that would otherwise need more time-consuming and costly electron-beam welding. “The disk laser is an exceptional welding device, delivering four times the power of our typical Nd:YAG,” says Dave Hudson, president. Deeper penetration, smaller heat-affected zone, and excellent beam quality are attributes of the disk that enable his company to compete in the aerospace and medical-device industries.
“In my opinion, two ’recent‘ developments will push lasers further into industry: the newer laser sources, which are more (power) efficient and more compact, and the hybrid laser-welding technique,” says Verhaeghe. “The laser is now more ’portable‘ than ever before, which means that on-site or remote application becomes easier. In fact, fiber lasers are looking more and more like MAG welding sets. With the use of lasers in shipyards as an example, and handheld, low-power laser welders already demonstrated, the sky‘s the limit for the future of laser welding.”
About the Author
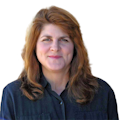
Gail Overton
Senior Editor (2004-2020)
Gail has more than 30 years of engineering, marketing, product management, and editorial experience in the photonics and optical communications industry. Before joining the staff at Laser Focus World in 2004, she held many product management and product marketing roles in the fiber-optics industry, most notably at Hughes (El Segundo, CA), GTE Labs (Waltham, MA), Corning (Corning, NY), Photon Kinetics (Beaverton, OR), and Newport Corporation (Irvine, CA). During her marketing career, Gail published articles in WDM Solutions and Sensors magazine and traveled internationally to conduct product and sales training. Gail received her BS degree in physics, with an emphasis in optics, from San Diego State University in San Diego, CA in May 1986.