Fiber-Bragg-grating sensor system developed at PolyU now under test on China's high-speed rail
Hong Kong--Fiber-bragg-grating (FBG) sensor systems developed at Hong Kong Polytechnic University (PolyU) have been installed along several lengths of China's high-speed rail system to monitor structural health of the rails. PolyU is collaborating with Southwest Jiaotong University (Chengdu, China) and Dalian Jiaotung University (Dalian, China) to characterize the performance of the FBG systems.
The PolyU FBG sensors are periodic structures created inside the 10 µm core diameter of standard 125 µm optical fibers. The hundreds of installed optical sensors provide information on vibration, acceleration, and temperature change for engineering staff, helping them to monitor the condition of tracks and railcars as well as the structural health of the rail foundation. They also keep track of train speed, axle balance, and vibration data for record and further analysis. PolyU’s optical sensors have also been installed on the new generation of high-speed trains for monitoring wind pressure.
PolyU hosted the First International Workshop on High-Speed and Intercity Railways from 20 to 22 July in Shenzhen and Hong Kong. The workshop was co-organized with Southwest Jiaotung University, Beijing Jiaotung University, Dalian Jiaotung University, China Engineering Consultants, Inc. (Taiwan), Zhejiang University and Tsinghua University.
A research team in PolyU's department of mechanical engineering has developed an ultrasonic diagnosis system that detects cracks arising from metallic fatigue and corrosion of key parts in the track and rail. The technology can be combined with the use of laser actuating/sensing technology for monitoring the structural health of bridges, tunnels, tracks, train bodies, bogie frames, and wheel axles.
Subscribe now to Laser Focus World magazine; it’s free!
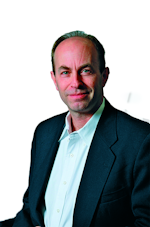
John Wallace | Senior Technical Editor (1998-2022)
John Wallace was with Laser Focus World for nearly 25 years, retiring in late June 2022. He obtained a bachelor's degree in mechanical engineering and physics at Rutgers University and a master's in optical engineering at the University of Rochester. Before becoming an editor, John worked as an engineer at RCA, Exxon, Eastman Kodak, and GCA Corporation.