PLYMOUTH, MN--Vixar was awarded a Phase II SBIR grant by the National Science Foundation (NSF; Arlington, VA) for the development of integrated wafer-scale vertical-cavity surface-emitting lasers (VCSELs) and VCSEL arrays with heterogeneous lensing (meaning lens arrays fabricated separately and then combined with the VCSEL arrays). While lenses can be fabricated directly on VCSELs using photolithographic techniques, the heterogeneous alternative--creating lens arrays separately from a material more suited to optics fabrication, then combining them with the VCSELs--can both simplify the process and produce a better end product.
Vixar is an independent designer and manufacturer of high-performance VCSELs that emit at wavelengths from 650 to 900 nm; the company targets new applications and markets driven by miniaturization and high optical output, including sensor and device applications in the biomedical, industrial, office-product (scanners, for example), military, automotive, and consumer industries. Because VCSELs can be made en masse without cleaving, they are especially useful and cost-effective in arrays.
“The primary objective of the NSF small business innovation research/small-business technology transfer (SBIR/STTR) program is to increase the incentive and opportunity for small firms to undertake cutting-edge, high risk, high quality scientific, engineering, or science/engineering education research that would have a high potential economic payoff if the research is successful,” says Mary Hibbs-Brenner, Vixar’s CEO. “We believe we are pursuing a cutting-edge, high quality engineering project that can benefit across many industries.”
Very large VCSEL arrays
Vixar was founded by Hibbs-Brenner and Klein Johnson, both of who were previously at Honeywell International (Richardson, TX), and who initiated Honeywell’s first research work on VCSELs in the early 1990s. Honeywell went on to become the largest supplier of VCSELs for data communications, before selling its VCSEL Optical Products unit to Finisar (Sunnyvale, CA) in 2004.
“In its early stage, Vixar worked on improving performance and reliability of red VCSELs to a point where commercial deployment is now viable,” says Hibbs-Brenner. “The company is leveraging its semiconductor-design expertise in red VCSELs, along with its experience gained in the data communication industry, to cost-effectively package laser-diode arrays up to 14 inches in length.”
In the heterogeneous process, the lenses are typically fabricated in a separate macroscopic molded-plastic array that is then aligned to the VCSEL package as a separate component. “For data communication, two common variants include VCSELs either in a 1 x 4 or a 1 x 12 VCSEL-array format on a 250 micron pitch,” explains Hibbs-Brenner. “In contrast, our project will develop a chip-scale package with the lens array integrated into the package. This will allow more densely spaced arrays, which is of interest for applications outside of data communication--for example, for sensing, scanning, or printing. We intend to develop arrays with as many as 64 elements on a single chip.” The end result of the SBIR will be a packaging technology that is ready to be applied to specific products, including both discrete VCSELs and VCSEL arrays, notes Hibbs-Brenner.
Just one example of the financial benefit of VCSELs can be found in an oxygen sensor from Applied Analytics (AAI; Concord, MA), made specifically to monitor the oxygen line at 760 nm (see www.laserfocusworld.com/articles/367413); the use of a VCSEL rather than a conventional distributed-feedback laser diode lowered the price of the instrument without reducing performance. For uses requiring arrays rather than single VCSELs, the economy of scale is, of course, an even bigger enticement.
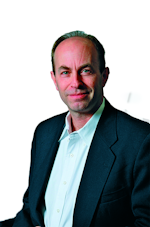
John Wallace | Senior Technical Editor (1998-2022)
John Wallace was with Laser Focus World for nearly 25 years, retiring in late June 2022. He obtained a bachelor's degree in mechanical engineering and physics at Rutgers University and a master's in optical engineering at the University of Rochester. Before becoming an editor, John worked as an engineer at RCA, Exxon, Eastman Kodak, and GCA Corporation.