MOUNTAIN VIEW, CA--Back in early 2008, Optoelectronics Report described the technology behind the fiber laser offering from Mobius Photonics (Mountain View, CA). After its initial launch of green 532 nm and ultraviolet (UV) 355 nm fiber lasers that were meant to replace diode-pumped solid-state (DPSS) lasers, Mobius introduced UV laser sources based on the harmonic wavelength conversion of the output of a seeded optical fiber amplifier (technology obtained by entering into an exclusive licensing agreement with Harvard University). Just two short years later, Mobius has publicly announced that its UV laser sources are performing better than DPSS lasers for thin-wafer dicing, as well as for other materials and microelectronics processing applications.
“Our laser is able to produce a similar high-quality cut and resulting die strength as conventional mechanical methods,” said Manuel Leonardo, Mobius Photonics VP of technology, in Mobius’ latest press release. “It also cuts faster than mechanical methods and avoids the random chipping that those systems often create.” Leonardo said that the use of DPSS lasers for thin-wafer dicing has been hampered due to poor die-strength data: 50 micron thick wafers diced with DPSS UV lasers produced dies with significantly lower break strength than conventional mechanical methods. He adds that the Mobius laser also produces smooth, continuous scribe lines in glass substrates and generates 1-micron-diameter, uniform through holes in 25-micron-thick polyimide.
Application-based performance
“The Mobius laser basically picks up (at 200 kHz) where the DPSS laser ends,” says Kiyomi Monro, VP of business development for Mobius Photonics. Mobius attributes the superior performance of its lasers to the all-fiber-amplifier, master-oscillator-power-amplifier (MOPA) architecture, saying that its nanosecond source can produce several wavelengths and support various pulse repetition frequencies and pulse widths. “We move beyond 200 kHz up to the megahertz level and beyond—with several applications using a 20 MHz repetition rate. Because we don’t mode lock, we can play with pulse width and rep rate, tailoring them to a particular application.”
“For wafer-dicing applications, we have actual die strength data and a min/max value that we can disclose under NDA,” says Monro. “But we can now publicly disclose average die-strength data for our 355 nm UV laser operating at 2 ns of 657 MPa.” Even though mechanical methods can routinely achieve die strengths of 600–700 MPa, the random backside chipping lowers yields significantly, says Monro. “People have their own opinions about why DPSS lasers produce wafers with half the die strength of those cut with conventional methods [367 MPa for DPSS Q switched UV lasers],” says Monro, “but many say it is the thermal interaction between the wafer and the 10 to 60 ns DPSS UV pulse width that produces micro-cracks. Data proves that our 2 ns pulse width with the high rep rate mitigates these issues.”
In addition to wafer dicing, Monro says that Mobius lasers’ ability to select pulse duration on the spot makes it indispensable for thin-film solar-cell scribing. “Because each of the layers has a different property, we can scribe different materials using a single laser by varying the pulse duration on demand.” He also notes that Mobius lasers are ideal sources to provide the depletion beam in stimulated-emission-depletion (STED) microscopy applications. In fact, Mobius issued a release in September 2009 discussing the use of its lasers for STED experiments at the Max Planck Institute for Biophysical Chemistry in Gottingen, Germany.
More than exclusivity
At least for the next seven years, companies wanting to produce a UV fiber laser with a Mobius-like architecture would be violating the Harvard patent. But Mobius is not resting on this reassurance; instead, the company is working tightly with customers on defining the applications for which its lasers are uniquely suited. “We have a flexible platform that truly is a new breed of laser, bridging the gap between DPSS Q-switched lasers and mode-locked lasers,” says Monro. “By working closely with customers and demonstrating the value of our laser through actual performance data, for example, on patterned wafers from customers rather than bare wafers, we hope to let the data speak for itself.”
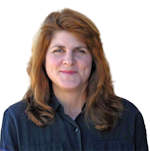
Gail Overton | Senior Editor (2004-2020)
Gail has more than 30 years of engineering, marketing, product management, and editorial experience in the photonics and optical communications industry. Before joining the staff at Laser Focus World in 2004, she held many product management and product marketing roles in the fiber-optics industry, most notably at Hughes (El Segundo, CA), GTE Labs (Waltham, MA), Corning (Corning, NY), Photon Kinetics (Beaverton, OR), and Newport Corporation (Irvine, CA). During her marketing career, Gail published articles in WDM Solutions and Sensors magazine and traveled internationally to conduct product and sales training. Gail received her BS degree in physics, with an emphasis in optics, from San Diego State University in San Diego, CA in May 1986.