MANCHESTER, NH—Anyone who needs precision plastic optics manufactured in quantities from a single optic to millions of components now has a new option: Molded Plastic Optics, LLC (MPO). The company, which recently opened for business, has diamond-turning equipment (for creation of molds, as well as low quantities of optics) and robotically controlled molding facilities (for high-volume manufacturing runs) in its 10,000 sq. ft. plant. Optical components can be produced to meet mil-spec requirements if needed. The four-employee staff of MPO is evidence of its efforts toward robotic manufacture.
Founded by Richard Cartier and William David Schmidt, the company can make aspheric as well as spherical optics, and offers lens-design and mount-design capabilities, subassembly of components, and comprehensive testing and verification of all parts. As described by Cartier, MPO’s president, the company’s metrology lab includes a Mitutoyo profilometer that measures lens sag to 0.1 µm, as well as a “high-end” Zygo interferometer.
Before co-founding MPO, Cartier worked at Insight Technology (Londonderry, NH) for 19 years at various positions, both technical and corporate. Insight designs and makes night-vision and electro-optical systems for the U.S. military and federal law-enforcement agencies, as well as tactical illuminators (weapon-mounted, for example) for use by police and the general public. “When I started there, the company had four employees,” he notes. “During my stay there, I experienced its growth to 1200 people.”
Cartier explains that the process of designing and making plastic optics must compensate for idiosyncrasies that are foreign to the fabrication of glass optics, with one being the shrinkage of a lens during molding. To deal with this, MPO starts out with molding machines that are equipped with injection compression, in which a mold is under continuous impression as the plastic solidifies, keeping the mold in intimate contact with the part to eliminate any air gaps. But just as important is the fact that the company has lens design, mold fabrication, and metrology under one roof: this allows optics to be designed to compensate for any dimensional change; allows for precise quantification of a first prototype, and leads to quick changes to the “mold pin” if needed via diamond-turning (the mold pin is the part of the mold that directly shapes the lens).
One advantage of plastic optics is that spacers, mounts, and so on can be molded into the lens itself. The profilometer can then be used to check the dimensional accuracy of the mount and its positional accuracy relative to the lens. Plastic optics can be optically coated, as well; MPO provides multilayer optical coatings, although it partners with coating suppliers for this.
The manufacturing line’s robotic capabilities at MPO, which are still being set up, according to Cartier, will include unloading parts from molds, placing them on the conveyer belt, and getting them ready for coating. Cartier describes the company’s goal as a “lights out” automated manufacturing system, in which the only cost is electricity.
Cartier was driven to form MPO partly because of previous experiences with plastic optics, in which going from the design phase to having the parts made could take a year. In contrast, MPO can go through the entire cycle in two to four months, depending on the parts’ complexity, says Cartier. “We like to think of MPO as a place that offers ‘one-stop shopping,’” he adds.
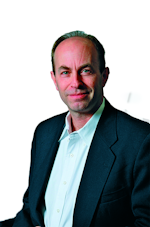
John Wallace | Senior Technical Editor (1998-2022)
John Wallace was with Laser Focus World for nearly 25 years, retiring in late June 2022. He obtained a bachelor's degree in mechanical engineering and physics at Rutgers University and a master's in optical engineering at the University of Rochester. Before becoming an editor, John worked as an engineer at RCA, Exxon, Eastman Kodak, and GCA Corporation.