PHOTONICS APPLIED: OPTICAL SENSING: Downhole sensing puts fiber optics to the test
Energy providers are continuously exploring new methods to improve oil-well yields and expand available energy resources.1, 2Fiber-optic sensors are an established method for downhole oil and geothermal reservoir, well, and pipeline monitoring and are capable of providing temperature and pressure information (with chemical analysis coming soon) in order to maximize resource extraction.
Unfortunately, the downhole environment is not kind to optics: Extremely high temperatures and pressures along with vibration and corrosive chemicals can push optical components—and the associated headend measurement equipment—to the limit. However, several optical technologies are meeting the downhole sensing challenge head on.
Harsh conditions
"Even though some small pilot installations began in the 1980s, optical sensors are installed in a relatively small number of the existing tens of thousands of terrestrial, offshore, and subsea oil and gas wells," says Paul Sanders, founder of Qorex LLC (Rocky Hill, CT) and head of technical marketing and business development.3 Sanders says the low penetration rate is due to the fact that the economics associated with shallow, easily recovered oil do not justify the premium of permanent downhole monitoring. But as this "easy" oil dries up, energy providers are looking to shale oil and oil sands reserves that typically require injection of heat, steam, and/or chemicals directly into the resource to enable recovery of usable oil and gas at the surface (see Figs. 1 and 2)."Optical sensors are crucial in high-temperature, thermal recovery applications to provide insight into the subsurface to optimize resource extraction and to ensure—for safety and environmental reasons—the integrity of the well remains intact," says Sanders. "Processes such as steam-assisted gravity drainage [SAGD] for in situ bitumen recovery is driving the uptake of optical sensors that operate at temperatures between 250°C and 300°C where fiber-optic technology becomes compelling over conventional sensors."
"Besides kilobar pressures and ultrahigh temperatures, the diffusion of hydrogen into the core of the glass sensing fiber-a phenomenon known as hydrogen darkening-impeded practical use of downhole optical sensing systems for many years," says Fereydoun Faridian, president of Intelligent Fiber Optic Systems (IFOS; Santa Clara. CA). "Fortunately, modern pure-silica fibers with virtually no darkening and improved hermetic coatings and packaging techniques can allow fiber operation at temperatures up to 700°C."
Sensing methods
"Most downhole optical sensing systems use Raman distributed temperature sensing [DTS]," says Faridian. "In the inelastic Raman interaction between a photon of light and a molecule of matter, the molecule may gain (Stokes scattering) energy from or lose (anti-Stokes) energy to the photon. The latter happens to be more temperature dependent and is used to measure temperature along the length of a fiber, which can go several kilometers deep (or across) with 1 m and sub 1°C resolutions. Knowing the temperature gradient can tell you where you are in a steam- or hot-water-assisted producing well (see Fig. 3). Also, unexpected variations of temperature gradients along the depth of the well can, for example, pinpoint faults in the casing." Faridian cautions, "The science is impressive, but engineering for price performance is everything-all DTS systems are not created equal.""Raman DTS, Brillouin distributed temperature and strain sensing (DTSS), and fiber Bragg-grating (FBG)-based optical sensors can all provide distributed sensing of temperature, strain, flow, and pressure," says Hua Xia, senior photonics system engineer and physicist at GE Global Research (Niskayuna, NY). "The most common are Raman systems due to their insensitivity to strain. Brillouin DTSS measures frequency shift and intensity of backscattered signals for both strain and temperature monitoring, while FBGs measure the wavelength of the reflected light that satisfies the Bragg resonant condition. The reflected peak wavelength responds to changes in both temperature and strain at the FBG.4 Raman and Brillouin offer continuous sensing with 0.1–1 m spatial resolution, while FBGs offer discrete or quasi-distributed sensing with a spatial resolution as small as 0.01 m."
These sensing technologies vary not only in functionality but in price and complexity. "A Raman system is in the range of $50-$100K, Brillouin DTSS is $100–$150K, and FBG systems are in the $15–$25K range," says Xia. "Since the fiber itself is the sensor, a fiber cable is all that is required for Raman and Brillouin systems. However, FBG sensors must be inscribed inside the fiber, and then each FBG packaged as a pressure, temperature, flow, seismic, or strain sensor. Making a sensing cable with many packaged FBG sensors can be relatively complicated and requires more engineering effort and expense."
Xia is also a team member of a $2.6 million, two-year US Department of Energy (DoE)-sponsored project initiated in January 2010 that aims to develop an optical sensor suite for the measurement of distributed temperature and pressure in geothermal wells.5 The system must make measurements in a high-temperature (to 374°C) and high-pressure (to 220 bars) environment at depths down to 10 km with a pressure measurement accuracy of <1% and a long-term drift of <1%.
Commercial options
"Raman DTS is followed by FBG technology as the next most exploited optical sensor technology in downhole environments," says Sanders. "FBG is used in two basic implementations: as the point strain and temperature sensing element that FBG is well known for, and to construct interferometric sensors used mostly for strain and acoustic transducers. Recently refined for downhole applications, FBGs are used as distributed multipoint sensors to monitor key production intervals and for sub-sea ocean bottom facility monitoring." Fortunately, FBG interrogation instruments that use a scanning laser from Micron Optics (Atlanta, GA), for example, can also benefit from semiconductor optical amplifiers (SOAs) from companies like Alphion (Princeton Junction, NJ). The SOAs amplify the laser input signal for simultaneous, high-sampling-rate measurements of hundreds of distributed FBG sensors as far as 50 miles away from the headend (although most downhole sensor systems extend to <5 mile depths).
Brillouin optical time-domain analysis (BOTDA) systems from OZ Optics (Ottawa, ON, Canada) use stimulated Brillouin scattering (SBS) from two counter-propagating beams in a two-way optical path, and—unlike point-to-point FBG sensors—can measure strain and temperature simultaneously. Brillouin achieves simultaneous ±2 μstrain accuracy and ±0.1°C temperature accuracy with 0.1 m spatial resolution, compared to discrete ±1 μstrain and ±0.4°C accuracies for a distributed FBG system.
"Our Raman-OFDR [optical frequency-domain reflectometer]—with an installed base of 2200-plus systems and the only frequency-domain-based DTS system on the market—is the most cost-effective system available today," says Daan Van Laar, LIOS (Cologne, Germany) key account manager for the oil and gas upstream sector. The Raman OFDR uses a continuous-wave (CW) laser modulated at different frequencies instead of a pulsed laser as in Raman-OTDR technology. Frequency profiles are generated by measuring amplitude and phase of anti-Stokes and Stokes Raman signals at a range of frequencies, with time- and thus distance-dependent Raman signals obtained after inverse Fourier transform of the frequency profiles. These signals are then used in the calculation of spatially resolved temperature profiles along optical fibers. "Major advantages of Raman-OFDR are CW laser operation for high signal levels at moderate laser peak powers for extended laser lifetimes, as well as economic detection schemes based on the heterodyne concept," adds Van Laar.
"A major application that benefits from fiber-optics is downhole pump monitoring," says Ivan Melnyk, CTO at Photon Control (Burnaby, BC, Canada). "Pumps are placed at the end of vertical well sections to pump crude oil out. In addition to extreme pressures and temperatures, sand can clog pipes, leading to premature ageing of the pumps. Their replacement is a very expensive procedure—not just the high pump cost, but their removal and process interruption." For temperature and pressure monitoring at the pump site, Photon Control uses patented technology based on white-light interferometry in which a tiny displacement of two parallel surfaces (a Fabry-Perot gap) is measured optically over distances up to 5 km and temperatures up to 300 °C. The measurement uses proprietary spectral demodulation techniques in the downhole range from 750–800 nm using Photon Control's spectrometers.
"One of the most significant advantages of optical sensing for downhole applications is the ability to operate at high temperatures for the lifetime of the well, enabling permanent deployment of optical sensing systems in conditions that are beyond the capability of competing electronic gauges," says Domino Taverner, R&D manager for optical sensing systems at Weatherford (Wallingford, CT). The company offers Raman DTS, FBG-based pressure/temperature point-sensors, and interferometric-based multiphase flow meters and seismic systems. "These sensing systems can be multiplexed in a variety of configurations on a single quarter-inch cable offering permanent deployment of multiparameter sensors in multiple zones in the harshest of conditions; the combination of these different optical sensing technologies offers the most useful information and value to our customers."
Beyond petroleum
"IFOS has focused on the engineering development of three systems for our oil and gas clients: a Raman-based DTS system; a real-time broadband FBG-based pressure sensor; and a fiber-optic gyroscope for directional drilling and measurement-while-drilling applications," says Faridian. "But our FyberSpace side-polish technology platform enables the manufacture of many physical, chemical, and even biological optical sensors, as well as optical components such as tap couplers and polarizers. We do some unique aerospace work with NASA and the DoD [Department of Defense], but equally exciting is work with the DoE in wind-turbine blade-health monitoring and optimization. The most challenging frontier, however, has been that of miniaturizing the optical sensors and fitting them into biopsy needles and catheters for insertion in arteries and veins in image-assisted surgery."
Faridian concludes, "Whether 5 km inside an oil well or 5 cm inside an unfriendly tumor, the challenge is always the same: getting the science to work and the engineering to create features and benefits that can provide a sustainable applications advantage to leading industry players."
REFERENCES
1. "MarketBeat 4Q10," Cushman & Wakefield, http://bit.ly/gSITLQ.
2. "Oil to Reach $100 on OPEC Capacity Drop, Goldman Says," BusinessWeek online, http://buswk.co/i1bTM1 (Dec. 22, 2010).
3. P. Sanders, Opt. & Photon. News (OPN), 22, 1, 36–42 (January 2011).
4. H. Xia, US Patent 7,574,075 (Aug. 11, 2009).
5. W. Challener et al., "Subsystem design and validation for optical sensors for monitoring enhanced geothermal systems," Proc. 36th Workshop on Geothermal Reservoir Engineering, SGP-TR-191, http://bit.ly/hZaHft (Jan. 31–Feb. 2, 2011).
Optical gas-flare monitoring
Besides its suite of interferometric sensors for downhole monitoring, Photon Control also offers a "laser-two-focus" (L2F) system for gas flare and flow monitoring of industrial gases associated with the downhole process (see figure). Recognizing that laser Doppler velocimetry (LDV) falls short for this application due to its high cost and need to particle-seed the flows due to low signal-to-noise ratio, Photon Control adopted L2F optical-transit-time velocimetry and now has more than 100 systems installed in the field for monitoring gas flows in 4–36 in. diameter pipes at flow rates between 0.1–150 m/s.
The L2F technique monitors particle flows in gas flares or pipelines by analyzing the time interval for light scattered onto two different detectors as the particle flows through the system. These optical systems replace thermal dispersion mass-flow meters whose performance is affected by gas composition and ultrasonic gas flow meters that fall short on high gas velocities, price, and installation cost.
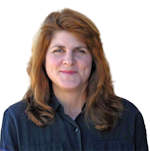
Gail Overton | Senior Editor (2004-2020)
Gail has more than 30 years of engineering, marketing, product management, and editorial experience in the photonics and optical communications industry. Before joining the staff at Laser Focus World in 2004, she held many product management and product marketing roles in the fiber-optics industry, most notably at Hughes (El Segundo, CA), GTE Labs (Waltham, MA), Corning (Corning, NY), Photon Kinetics (Beaverton, OR), and Newport Corporation (Irvine, CA). During her marketing career, Gail published articles in WDM Solutions and Sensors magazine and traveled internationally to conduct product and sales training. Gail received her BS degree in physics, with an emphasis in optics, from San Diego State University in San Diego, CA in May 1986.