Aachen, Germany--The Fraunhofer Institute for Laser Technology (ILT) has developed a packaging process for microcomponents and electronic parts that is based on laser glass soldering. It is suitable for use in mass production and, because it uses lead-free solders, fulfils the stringent environmental regulations of the EU's RoHS Directive.
Hermetic sealing keeps water, oxygen, and other contaminants out of packages that hold sensitive equipment such as semiconductor chips, sensors, and optical and medical system components. Gas-tight packaging of the complex interiors of these assemblies poses challenges for this last step in the microcomponent manufacturing process.
Conventional hermetic processes are very hot
High-temperature processes such as anodic bonding and glass frit bonding are widely used methods for hermetically sealing components made of silicon and glass. The heat needed for joining is introduced into the component by a kiln process at temperatures of 300°C to 600°C. Because the most temperature-sensitive component determines the maximum allowable temperature of the entire system, these two processes cannot be used for temperature-sensitive functional elements. They are, for example, unsuitable for encapsulating OLEDs, because the functional organic layers would be destroyed at a temperature of even 100°C.
At present, temperature-sensitive components are usually glued, but extended testing on semiconductors and OLEDs has shown that the durability of the glued connection is limited. Oxygen and moisture gradually penetrate the interior of the component and affect its function (glue is not a hermetic seal). The limited durability and the temperature sensitivity of glued connections are a problem, especially for components used in the medical sector, as they cannot withstand sterilization processes in autoclaves.
High-quality hermetic seal with little heat
Laser-based soldering with glass solder materials offers a suitable solution. This is a relatively new joining technique that subjects the entire component to only minimal thermal loading. Research scientists at the Fraunhofer ILT aim to introduce the technique soon into production. In the technique, the solder, which consists of a glass-particle paste, is first applied to the packaging using a mask (no temperature-sensitive components are present at this point). The solder is then pre-vitrified in a kiln at a temperature of 350°C to 500°C depending on the type of glass paste used, so that the binders in the paste evaporate. After the solder has cooled, the sensitive components are joined to the cover. A defined and locally limited temperature increase is achieved by scanning the solder seam with a laser beam. The rest of the component is not affected by this application of heat. The entire solder contour is evenly heated; the cover can sink into the liquid solder bath and is thus hermetically connected to the component.
Compared with gluing, the laser-based method achieves a considerable increase in the durability of the entire microcomponent, and the permeability of liquids and gases is practically zero. What's more, the solder seam is completely free of bubbles and cracks. For the medical sector in particular, this means a significant increase in safety.
No lead solder needed
"A further advantage of laser-based glass soldering is that the solder seam is very narrow, measuring just 300 to 500 microns, whereas glued seams have a width of several millimeters," says Heidrun Kind, project manager at the Fraunhofer ILT. "This fact becomes increasingly important with the advancing miniaturization of precision components. Wide glued seams on OLEDs, for example, are regarded as visual defects. On sensors used in implants, they can change the entire component geometry detrimentally. In environmental terms, too, the technique has a bright future. We are now able to use completely lead-free solder, which means that our method meets the requirements of the EU's RoHS Directive for the minimization of hazardous substances in electrical and electronic components."
The process can be used to join components measuring up to 200 x 200 mm in size. In addition to glass/glass components, substrates with MAM or ITO layers or glass/silicon components can be hermetically connected to each other.
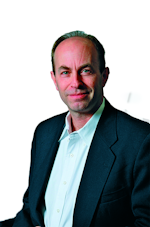
John Wallace | Senior Technical Editor (1998-2022)
John Wallace was with Laser Focus World for nearly 25 years, retiring in late June 2022. He obtained a bachelor's degree in mechanical engineering and physics at Rutgers University and a master's in optical engineering at the University of Rochester. Before becoming an editor, John worked as an engineer at RCA, Exxon, Eastman Kodak, and GCA Corporation.