Laser cleaning offers versatility for broad range of applications
One of the first laser cleaning applications dates back to the early 1970s, when it was proposed for the conservation of artworks by J. F. Asmus and L. Lazzerini through a set of practical tests carried out in Venice on encrusted stone artifacts1—until now, lasers have been used on several unique artworks. Today, the drawings of Leonardo da Vinci on the walls of the Sala delle Asse-Castello Sforzesco (Milan, Italy) are still under restoration. Different laser sources by Quanta System (El.En Group) with emission at 1064 nm and a pulse duration between 10 ns up to 120 ns are being used (see Fig. 1).
After this first sector, the technology was applied to paint stripping from airplanes by J. F. Asmus and through the years has attracted interest from a wide range of industries. The main advantage is that it is an eco-friendly, cost-effective process typically used to remove rust, paint, grease, oxide, and other contaminants from molds and metal surfaces, without the need to involve hazardous chemicals or aggressive processes such as sandblasting, which can damage the underlying material. Market reports predict the global laser cleaning market will reach almost $745 billion by 2026 at a compound annual growth rate of around 4.3%.2 The three main market drivers include the need for automated cleaning processes brought about by miniaturization and Industry 4.0, which has prompted the need to offer adaptable systems that can be used across multiple parts and processes; automotive and aerospace manufacturers’ need for a fast and simple way to treat and clean composite parts before bonding to ensure the integrity of the frame’s structure; and the need for cleaning systems for increasingly small electronic components, such as connectors, insulators, pads, and semiconductors.
The technology
Laser cleaning is based on laser ablation—the process of removing material mainly from a solid surface by irradiating it with a laser beam. Every material is composed of different molecular bonds that determine a specific ablation threshold—that is, the energy required to overcome the binding energy of the contaminant layer and decompose it. To remove the contaminant layer, the energy from the laser must be above the ablation threshold of the particular material; in general terms, as the ablation threshold increases, so does the energy required to remove the contaminant. For efficient laser cleaning, the ablation threshold of the material to be cleaned should be consistently higher than that of the material to be removed.
The types of lasers used for ablation vary according to the contaminant, the composition of the underlying material, the treatment required, and the surface area that needs to be cleaned. For example, near-infrared pulsed lasers of a few tens of watts (or more) are used often because they are more efficient in reaching the ablation threshold than continuous-wave lasers. At the same time, especially short pulses have the further advantage of not heating up the surface to be cleaned.
Environmental and safety issues always accompany laser ablation, as lasers vaporize materials into fumes. In the case of an oxidized metal surface, for example, the oxide particles detach from the surface and create a highly compressed plasma (ionized gas out of equilibrium), which expands and creates a shock wave that then fragments and ejects the layer of pollutant into the atmosphere. For this reason, a fume extraction system is always needed near a laser cleaning system.
Despite these issues, numerous European companies are developing laser cleaning technologies. More and more users are willing to commit to an initial investment to profit from the advantages of this technology for surface cleaning.
Electro-mobility (e-mobility) applications, including preparation of e-drive housings and sealant areas for adhesive bonding and the coating of battery cells, modules, and battery housings/frames, are among the drivers of the laser cleaning market.
A clean surface is a basic requirement for a successful, durable-welded, adhesive bond, and for a contact. Components in e-mobility are often coated with paint and functional layers, such as cathodic dip painting. Laser cleaning and paint removal can be used to strip paint and functional layers from selected areas on the component, precisely at the points where bonding should take place, or where the functional layers are no longer needed. Laser pulses with high peak powers vaporize the razor-thin layers without affecting the component. The absorbing material is heated by the laser energy and vaporized or sublimated. For this use, TRUMPF Laser-und Systemtechnik GmbH has designed a processing head together with Thyssenkrupp Automotive Body Solutions (see Fig. 2).This processing head contains scanner optics (PFO 33-2) and a specially developed suction nozzle with an integrated separator. With it, the particles that are removed and the smoke produced can be directly extracted and separated during the cleaning/paint removal process.
CleanLASER also specializes in the development and production of high-precision laser systems for industrial surface processing, particularly for e-mobility applications.
An excellent example of the challenges involved is de-coating copper and aluminum hairpins, which are used to build up electrostatics to produce electromotors. They are made of base material such as aluminum or copper and coated with various temperature-resistant plastics. The challenge is how to remove partial segments of these wires to produce a very good surface quality before a welding or soldering process. Specifically, the coating needs to be removed entirely from all four sides without any wire degradation. High reproducibility with varying coating film thickness is required, and the cycle time needs to be short at a minimal cost. By means of precise laser-based paint removal, it is not only possible to spot-de-coat battery housings made of aluminum or galvanized sheet steel, but also to remove paint from enameled copper wire residue-free. The blank copper wires are thus optimally prepared for the further soldering or welding process in the stator production of the electric motor (see examples in Fig. 3).Compared with welding in atmosphere, laser beam welding in vacuum has the advantage of better quality—that is, an absence of pores or cracks in weld seams, even in alloys difficult to weld. It also has a higher productivity, as the same welding result can be achieved by using lower laser power. Furthermore, laser beam welding in vacuum avoids spatters, vapor deposition, and oxidation, and is a scalable process with a wide range of penetration depths from 10 µm to >100 mm.
LaVa-X, a company developing and producing turnkey-ready machines for laser beam welding in vacuum, is now working with CleanLASER for the welding of aluminum hairpins. The achieved residue-free surface preparation is crucial for high-quality welding processes involving aluminum, which is particularly susceptible to pore formation as well as splattering—any grease, oil, or organic material on the surface evaporates when exposed to the laser beam. This can lead to numerous pores, spatters, and in the worst case, weld pool ejections.
4JET is another developer of laser systems for cleaning, patterning, marking, cutting, and modifying materials to achieve high-quality component surfaces. The company’s laser cleaning and surface preparation activities span various applications, including tire manufacturing and other general automotive products. For industrial cleaning tasks requiring high flexibility or the use of portable systems, 4JET developed the JETLASER series of flexible, handheld laser cleaning systems (see Fig. 4). These portable systems require only an electric power supply for operation. Key applications for handheld laser cleaning include mold cleaning in rubber and injection molding, composite manufacturing, and the food industry.The 15-m-long umbilical from the supply wagon to the sleek and lightweight handheld effector provides flexibility for a comfortable operation over hours. This flexibility allows the user to clean large and complex molds without unmounting heavy tools, and also enables cleaning directly in the press. A significant advantage of their machines is that laser energy densities can be easily adjusted simply by changing the focusing lens via a quick-release system. This enables the user to change the working distance and laser fluence, which considerably enlarges the field of applications.
The wavelength, pulse length, and power of the laser beam can be tailored to the specific material to be removed from a solid surface. For this reason, shorter wavelengths, including the UV spectral range, can be the most efficient choice for laser cleaning.
Laser systems with an emitted wavelength in the UV range show great potential for the bonding or coating pre-treatment of fiber-reinforced plastics (FRPs). Since the pulse energy is mainly absorbed by the resin material, damage to the implemented fibers can be avoided. The pulse energy must be higher than the ablation threshold of the resin to achieve a cleaning and slight activation effect. On the other side, an overtreatment should be avoided, as the resin material will be completely removed around the fibers, leading to a reduction in mechanical stability of the FRP interface.
In this context, UV-excimer laser systems developed by Coherent offer a variety of laser wavelengths (193 nm, 248 nm, and 308 nm), power levels (3 W to 3 kW), and pulse energy levels ranging from 10 to 6000 mJ. Additionally, Coherent supplies its customers with application-adapted beam-shaping optics, leading to defined beam dimensions with a top-hat energy distribution and thereby maximizing the treatment rate. Since UV laser radiation cannot be fiber-guided, treatment of large-scale or simple 3D parts is a complex topic. Typically, parts are moved in front of the exit of the laser optics on a portal system, which limits the possible applications.
The Fraunhofer Institute for Manufacturing Technology (IFAM) is developing concepts to make UV-excimer laser treatment more flexible while increasing the process rate with low- to medium-class power systems (up to 30 W). The two main approaches, namely the application of scan optics and a robotic-based treatment, are demonstrated in the table.Over the next few years, the inherent advantages of laser cleaning over traditional methods will inevitably lead to an increase in laser ablation applications, particularly for manufacturing. An EU-funded initiative supporting the development of laser cleaning and in general of laser-based processes—PULSATE—aims to connect many digital innovation hubs in Europe with expertise and state-of-the-art equipment in laser-based manufacturing technologies to reach all of the small- and medium-sized enterprises (SMEs) who want to fit in a digital-manufacturing and Industry 4.0 environment and see lasers as a key enabling technology, but are unable to implement it due to the lack of testing capabilities. This initiative will support SMEs through cascade funding and its unique support program created by technology and business experts from consortium partners. Interested companies can apply to the program through two kinds of open calls: Technology Transfer Experiments (launches in July 2022) and Adopter User Cases (launches in March 2022), and laser cleaning could be one of the technologies to be implemented and further developed.
Existing challenges the photonics community could overcome include increasing the throughput of laser cleaning, maintaining high reproducibility with varying coating film thickness, and the possibility of combining laser cleaning with laser-based surface patterning, where fast laser scanners and even robotics play a fundamental role. Furthermore, fast in-line process monitoring systems that support 1 m/s feed-speed and laser beam shaping technology adapting to high velocities are requested by the machine builders.
ACKNOWLEDGMENTS
EPIC wishes to acknowledge its members and collaborators who are always eager to share their ambitions and vision; in particular, Sabrina Vogt from TRUMPF, Benjamin Gerhards from Lava-X, Jan Flohre from 4JET, Ralph Delmdahl from Coherent, Salvatore Almaviva and Antonio Palucci from ENEA, Tobias Weichert and Elena Mekle from cleanLASER, Thomas Lukasczyk from Fraunhofer IFAM, Claudio Salsi, Francesca Tasso and Irene Scarcella from Comune di Milano, and all of the PULSATE partners. PULSATE has received funding from the European Union’s Horizon 2020 research and innovation program under Grant Agreement No. 951998. It is supported by the ICT Innovation for Manufacturing SMEs (I4MS) and the Photonics Public Private Partnership. This content reflects only the authors’ views and the European Commission and Photonics21 are not responsible for any use that may be made of the information it contains.
REFERENCES
1. J. F. Asmus et al., First International Conference on the Deterioration of Building Stones, 72, 1, 63–68 (1972).
2. See https://bit.ly/3qfKaVR.
3. S. Almaviva et al., Fusion Eng. Des., 169, 112638 (2021); doi.org/10.1016/j.fusengdes.2020.111685.
About the Author
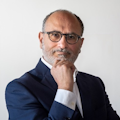
Antonio Raspa
Ultrafast Solid-State Laser Product Manager, Luxinar
Antonio Raspa is ultrafast solid-state laser product manager at Luxinar (Kingston upon Hull, U.K.), and an editorial advisory board member at Laser Focus World. He has more than 35 years of experience with solid-state laser design, photonics components, and fiber optics.
He holds a MSc degree in Electrical Engineering from Politecnico di Milano with a specialization in Quantum Electronics. Before joining Luxinar, he served as senior photonics program manager at the European Photonics Industry Consortium (EPIC; May 2020 – September 2022), preceded by Quanta System (1988-2000) as R&D manager for the development of solid-state laser sources and custom photonics systems for industrial and scientific applications. During this period, he participated, as Ozone LiDAR specialist, to the Italian research program in Antarctica. He then worked at Trumpf (2000-2008) and Rofin-Sinar (2008-2009) as a Product Manager for industrial laser products and processes. In 2009 he returned to Quanta System, organizing and managing a new plant for the production of sterile optical fibers for surgery.
Francesca Moglia
Project Leader, EPIC
Francesca Moglia is a Project Leader at the European Photonics Industry Consortium (EPIC; Brussels, Belgium).