Feasibility study tackles effective laser beam cutting underwater
Recall the old saying “What goes around comes around”? Many decades ago, I was associated with an offshoot of an underwater electron beam welding program that was to cut metals in that same environment. This project didn’t pan out for a variety of reasons, mostly associated with cost-effectiveness. Later, when high-power lasers were developed, it arose again and we looked at the laser beam as the heat source. Although the technology was proven, solving the cost-effectiveness barrier shut things down.
Now, scientists at Laser Zentrum Hannover (LZH; Hannover, Germany), an independent, nonprofit research institute, are setting out to answer whether a laser beam can be used for efficient reactor dismantling by cutting underwater (FIGURE 1). This is the scope of the AZULa project (which stands for “Automated separation of reactor pressure vessel installations using underwater laser technology”), a feasibility study that will involve developing a laser beam cutting process and constructing a compact cutting head for use in a radiologically activated and contaminated underwater environment.
FIGURE 1. Underwater laser cutting offers enormous potential for dismantling reactor vessels. (Photo credit: LZH)
This system is supposed to enable the direct dismantling of nuclear facilities (reactor pressure vessels), as laser beam cutting offers significant advantages compared to conventional cutting methods such as water jet cutting or sawing techniques—most significantly, control of the binding of the kerf material on the exit side, which is a standard laser cutting benefit. The expense for final cleaning of the water basin floor is significantly reduced, as the amount of secondary or technology waste is significantly lower compared to water jet or sawing techniques (FIGURE 2). The disposal of this waste is time-consuming and costly. In addition, sawing techniques are prone to jamming of the tool, which cannot occur with laser beam cutting. Thus, the process times could be shortened. Laser beam cutting would therefore represent a much cheaper alternative for dismantling of reactor components.
FIGURE 2. Less-contaminated secondary materials through an efficient laser cutting process are shown. (Photo credit: LZH)
The AZULa project, in collaboration with Orano (Paris, France), is sponsored by the Federal Ministry of Education and Research under a grant by project coordinator Gesellschaft für Anlagen- und Reaktorsicherheit (GRS; Köln, Germany).
Needless to say, I’ll be following progress with interest because globally, there are 76 nuclear reactors expected to retire by 2019, followed by 183 units in the 2020s and 127 units in the 2030s. It’s been looked at before, but maybe this backlog will be the impetus to ease cost-effectiveness concerns.
About the Author
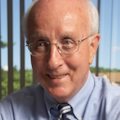
David Belforte
Contributing Editor
David Belforte (1932-2023) was an internationally recognized authority on industrial laser materials processing and had been actively involved in this technology for more than 50 years. His consulting business, Belforte Associates, served clients interested in advanced manufacturing applications. David held degrees in Chemistry and Production Technology from Northeastern University (Boston, MA). As a researcher, he conducted basic studies in material synthesis for high-temperature applications and held increasingly important positions with companies involved with high-technology materials processing. He co-founded a company that introduced several firsts in advanced welding technology and equipment. David's career in lasers started with the commercialization of the first industrial solid-state laser and a compact CO2 laser for sheet-metal cutting. For several years, he led the development of very high power CO2 lasers for welding and surface treating applications. In addition to consulting, David was the Founder and Editor-in-Chief of Industrial Laser Solutions magazine (1986-2022) and contributed to other laser publications, including Laser Focus World. He retired from Laser Focus World in late June 2022.