2018 was another record year, contending with turmoil
No matter where you looked during 2018, two somewhat-intertwined global economic factors had an adverse effect on the industrial laser market. China, already in the midst of a government effort to reduce a massive indebtedness while still increasing fiscal stimuli to continue bolstering developing industrial laser system exports, was hit by the preliminary results of a trade war spat with the U.S. that started affecting manufacturing output in the second half of the year. What, you may ask, does this have to do with total industrial laser revenues for the year?
China is the single largest market for industrial laser products, with about an estimated third of all industrial lasers—mostly fiber lasers—being imported into or built in that country to power the several thousands of sheet metal cutting systems produced domestically or exported to the Association of Southeast Asian Nations (ASEAN), India, and increasingly into Western world markets. This fulfills government dictates for expanding Chinese exports of machines, integrated with domestic IP technology. Therefore, some of the economic pain being felt by these companies as investment funds to shore up IP funding became difficult to obtain.
Furthermore, global suppliers of imported industrial lasers, from Europe and the United States, took a double hit from this slowdown in Chinese capital investments and, increasingly, from the fallout of a series of targeted tariffs instituted by the U.S. government. For example, about a third of global industrial laser products were exported to China (the Mechanical Engineering Industry Association [VDMA] has noted that German laser exports to China are more than 30% of the total), and as leading fiber laser manufacturer IPG Photonics stated, China “…remains our largest and most competitive market.” Also, currency exchange woes plagued company CFOs, leading to more mitigation statements from CEOs.
As Industrial Laser Solutions went to press in late 2018, it appears that the U.S. and China have agreed to a rapprochement on the issues of trade, which might lead to an easing of tariff barriers. However, the impact of tariffs has already negatively affected 2018 industrial laser revenue numbers, and it is too soon to predict a change in ILS’ projected 2019 revenue numbers.
A record out of a market uncertainty
So, identifying uncontrollable causative actions for second-half lethargy in the market, 2018 was another record year for industrial laser revenues. Led by gains in high-power fiber and excimer laser sales, company revenues cracked the $5-billion level. Looking back to 1970, the date ILS establishes as the beginning of the industrial laser business, revenues have grown a healthy 17.73% in compound annual growth rate (CAGR). And over these 48 years, only four serious downturns affected annual growth: in fact, since the 2009 recession when revenues dipped by up to 60%, the CAGR in more current dollars was 15.18%.
With the above out of the way, it’s appropriate to review ILS’ late-2017 estimates for 2018 annual revenues. Because of a quirk in the timing of official public-company quarterly economic reports, analysts have to rely on corporate guidance for end-of-year reports. As 2017 drew to a close, ILS, in an established process, used the midpoint of company revenue and growth rate guidance ranges to arrive at an estimate for 2018 revenues in the economic report for the January/February 2019 issue. As a consequence, the four Billion-dollar Club industrial laser companies turned in a greater-than-anticipated final quarter with very strong double-digit growth rates, making our mid-single-digit estimate look anemic.
This double whammy, with a currency twist, led to industry management adjusting forecasts in the second half to a level below ILS early 2018 estimates of 7%. Faced with a possible, but less likely, repeat in 2019, ILS went ahead with revised 2017 market numbers and arrived at an estimate of a nominal 5% gain in total 2018 industrial laser revenues. The revised (upward) total revenues in FIGURE 1 are about $4.9 billion (contributing to this increase is very current data from Chinese companies and companies new to the market).
The second-half 2018 market correction led to estimate adjustments and total market revenues should come in slightly above $5 billion, a 4%+ growth over 2017. As has been the case since the 2009 recession, fiber laser revenue growth was a major contributor.
Laser revenues under pressure
As noted in FIGURE 1, fiber lasers (specifically high-power fiber lasers) dominate industrial laser revenues in 2018, as they have since 2013 when revenues first surpassed the then-leading carbon-dioxide (CO2) lasers. In 2018, fiber lasers passed the 50% market share level—a remarkable 25.35% CAGR. After several years of superheated annual growth rates, as the high-power fiber laser became a more cost-effective alternative to high-power CO2 lasers for sheet metal cutting applications, the 2018 annual growth rate settled into a more single-digit growth rate commensurate with annual systems sales demand.
CO2 laser revenues dropped to the second highest revenue spot in 2017 and surrendered that position to other laser types this year and are projected to repeat in 2019.
Solid-state lasers, including the high-power disk laser, along with high-power diode and excimer lasers assumed the second and third revenue spots in 2018. Ultrashort-pulse (USP) solid-state lasers began to find multiple high-volume uses in new UV and femtosecond applications, showing a 12.8% CAGR since 2014. These lasers are projected to increase their growth rate in 2019. Excimer laser revenues slipped in 2018 as installations for faceplate annealing ramped down, a trend expected to continue in 2019.
Although 2018 proved to be a turbulent year for global manufacturing economies, and market turmoil brought on by changes in China domestically and in the export/import market caused second-half revenue adjustments, another record year seems assured (final numbers will be posted in early 2019). And ILS anticipates a continuation of this trend with modest revenue growth in 2019.
Applications growth stabilizes
As seen in FIGURE 2, macromaterial processing, heavily weighted by the slowing of the high-power fiber laser cutting systems market in China, slipped to a modest 3% growth (more about this later). Micromaterial processing grew by 5%, down from the gritting double-digit growth of 2017 that was due to one application—excimer laser annealing of silicon for display faceplates. Also, the delivery curve had flattened as planned, and shipments were ramping down.
FIGURE 2 shows that laser marking and engraving is one of only two high-unit-volume fiber laser applications (sheet metal cutting is the other), and is well into the commodity phase with more than 200 systems vendors (25% in China) locked in a selling-price battle covering international markets. CO2 engraving, especially in garment materials, experienced a modest resurgence as fashion changes dictated demand. Together, marking and engraving settled at a low-single-digit level, mainly driven by a few new applications—UV laser marking of previously unmanageable materials is one and a growing replacement market. The low-power laser marking and engraving market, most heavily centered in Asia, is a high-volume, low-profit business that for the past two years has been the scene of a bruising selling price battle between domestic and imported laser suppliers. For the past two years, marking and engraving laser revenues plateaued around 13%, and expectations are that this split will remain in the near-term.
Micro applications
Micromaterial processing, buoyed by deliveries from the faceplate annealing project, held a 32% share of the 2018 total market revenues (FIGURE 2), growing 5% over 2017. In the opinion of many knowledgeable experts within the industrial laser community, microprocessing offers the potential for the strongest growth opportunity over the next few years. Laser microprocessing tends to be more of a global application, with market strength in most established and developing economies.
The faceplate application that drove microprocessing applications in 2017 plateaued as to essentially no revenue growth in 2018. System deliveries achieved planned levels and display apps began the predicted return to normalcy, returning to a modest single-digit growth in 2019.
A closer look at the micromaterial processing sector for 2018 shows double-digit growth in fine metal and non-metal processing that was able to offset a double-digit decline in additive manufacturing brought about by temporary overcapacity in key user industries. For 2019, ILS expects a healthy double-digit growth 2019 for additive manufacturing revenues. The solar/other category picked up high single-digit growth as solar installations worldwide had a good year, but not in the U.S. where government support for subsidies was stymied by a lack of administration support. Other laser processes associated with alternate energy technologies are limited in size and currently do not contribute significant revenues. ILS expects the micromaterial sector will experience flat revenues in 2019.
Macro applications
Macromaterial processing continues to be the largest revenue sector at 55% of the total, repeating the same 2017 split while growing a modest 4%. A slowing in growth rate for high-power laser cutting arose in 2018 occasioned not by market saturation, but primarily as manufacturing economies globally tightened as the fallout of rising U.S. government tariffs was felt by export manufacturing and the impact of Chinese government tightening lending rates for capital equipment spending, not because of market saturation. A low single-digit growth in 2018 should be followed by a more-conventional, mid-single-digit rate in 2019.
Welding, the second largest macromaterial application (FIGURE 3), did not deliver the anticipated boost in revenues, as system suppliers gained experience with converting proposals into orders and into installations in 2018. Welding is a part-specific process and because the laser is rarely considered as a one-for-one replacement for conventional welding technology, sales occur after the laser is selected for a new or remodeled part is designed and laser welding is an extensively qualified or even certified processes that may take time. China seemed to be ready to make significant use of laser welding, but some near-term opportunities were delayed due mainly to the aforesaid market conditions in China. Mid-single-digit revenue growth in 2018 will likely repeat in 2019.
A cursory glance at the pie chart in FIGURE 3 makes it clear that macromaterial applications are the dominant revenue generator in 2018, with 54% of the total market. Cutting and welding applications are capital equipment-sensitive investments and subject to rapid response when national economies move. A clear example of this was the spurt in high-power fiber laser orders in the second half of 2017 that led to ILS’ adjustment of final 2017 revenue numbers in FIGURE 1.
The future
As the second decade of the millennium winds down, it is tempting to think about the future for industrial laser material processing. Look again at Figure 3—if we placed a weight on the applications shown, the disk would be tilted precipitously to the right side, as most of this is revenues from high-power cutting and welding applications. And in the near-term, this imbalance should continue with welding making up for some of the softening in cutting revenues brought on by maturation of the latter brought about by higher-productivity, higher-power, more cost-efficient cutting systems.
However, it is apparent that the left side of this pie chart is populated, less marking and engraving, by a wedge of high-growth-potential applications that are rapidly increasing revenues to a level that should shift the balance in the coming decade as a new generation of cost-effective solid-state, diode, and fiber lasers find broad industry acceptance in an increasingly automated manufacturing marketplace.
About the Author
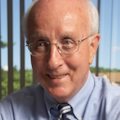
David Belforte
Contributing Editor
David Belforte (1932-2023) was an internationally recognized authority on industrial laser materials processing and had been actively involved in this technology for more than 50 years. His consulting business, Belforte Associates, served clients interested in advanced manufacturing applications. David held degrees in Chemistry and Production Technology from Northeastern University (Boston, MA). As a researcher, he conducted basic studies in material synthesis for high-temperature applications and held increasingly important positions with companies involved with high-technology materials processing. He co-founded a company that introduced several firsts in advanced welding technology and equipment. David's career in lasers started with the commercialization of the first industrial solid-state laser and a compact CO2 laser for sheet-metal cutting. For several years, he led the development of very high power CO2 lasers for welding and surface treating applications. In addition to consulting, David was the Founder and Editor-in-Chief of Industrial Laser Solutions magazine (1986-2022) and contributed to other laser publications, including Laser Focus World. He retired from Laser Focus World in late June 2022.