Seoul, South Korea, is a sprawling city of 10.3 million people, spread out over 605 km2 on both sides of the Han River. To put it into perspective, New York City with 8 million people covers about 785 km2. If you count the surrounding suburbs, about 17 million people are living in metro Seoul, all, it seems, on the road, all the time.
Seoul is fast approaching world-class status. It's a clean, modern city where 25% of the country's population lives. It's loaded with every convenience you could ask for. Everywhere you go, bright, young, attentive, well-educated, industrious people are eager to advance their prospects in life. Currently a socialist-minded government has put the brakes on economic growth, but you get the feeling that this is a temporary situation.
Soccer's 2002 World Cup, held here jointly with Japan, did wonders to upgrade the city toward international cosmopolitan status. It would hold this title today if it weren't for the persistent traffic which, on a Friday afternoon, can turn a 1.5 km drive into a 45-minute headache. The city government didn't help matters much when, on July 1st, it changed all the bus routes without much advance notice, turning an already bad situation into a nightmare. Even the bus drivers were still confused on the 10th, and heaven help you if you tried to get a transfer.
But the Koreans have a way of persisting. As one company president told me, "We learn fast."
I'm in Korea as an invited speaker, along with Laser Focus World Editor Steve Anderson. We are presenting the Global Laser Marketplace at the Worldwide Photonics Market Trend 2004—Optics & Laser Seminar sponsored by the Korea Association for Photonics Industry Development. It's being held at the big, beautiful COEX, a combined conference and exhibition center located in the southeast of Seoul, near the Olympic Stadium. I place the seminar location because Seoul is a city of multiple centers, all, it seems to me, about 45 minutes from each other, depending on traffic. There's the cluster around City Hall, another around the government center, another around the diplomatic legations, another around the sports complex, etc. You can do them faster by subway, if you don't mind sardine packing.
I'm told everyone wants to live in Seoul because it has the best schools, stores, entertainment, nightlife, culture, universities, housing, lifestyle, etc. For example, I met with three corporate presidents, all with companies located an hour's drive outside the city, who chose to live in the city.
Industrial laser activity is big in Korea, in terms of annual revenues. There are less than 10 domestic laser system suppliers and an estimated additional 30 distributors of imported systems, mainly laser markers. However, the three leading system suppliers estimate that domestic sales of industrial lasers totaled 900 units last year, with another 600 units exported mainly to Asian markets.
Approximately 850 laser cutting systems are installed in Korea, most of which are located in job shops, with another 120 units added each year. The economic picture has been cloudy in recent months as the political situation with a socialist-leaning government has tended to put the brakes on economic growth, much to the concern of industry. As a result, unemployment hovers around 10%.
But you would never know it walking around the city's shopping center, where young people were out celebrating their acceptance by universities by spending large sums of money on clothes, cosmetics, and CDs—money, we learned, provided by parents as a reward for the students' extra study efforts.
Like China, Korea seems committed to full employment nonetheless. Case in point: I was poking around in duty-free shops at Inchon Airport, killing some time. In several I could hardly move without bumping into a clerk and in several I was constantly followed by a clerk who was at my elbow at all times, a most annoying service.
Hankwang Co. Ltd., the largest laser machine manufacturer in Korea, occupies a hilltop in Kyunggi-do about one hour south of Seoul. The company moved to this attractive plant two years ago when the new international airport in Inchon made real estate rates too high for the company, which had formed in Inchon in 1990, to expand.
Company President Jay Kay, returning to Korea with a graduate degree in business from New York University, happened to see a demonstration of laser cutting, decided that this was a technology of the future, and founded Hankwang. Fourteen years later the company, specializing in cutting, welding, and special-purpose laser systems, prides itself on "quality and price," two factors Kay says are synonymous with the company's name.
This year, experiencing the effects of economic downturn, the company will do $23 million, with about 20% of that from exports. Next year Kay expects the company will do about $30 million, of which 50% will come from exports. This represents about 50% of the Korean market for laser cutting equipment. He does this with 100 employees.
Products include the Echo Flying Optic and Koba Hybrid cutters powered by Panasonic CO2 lasers up to 4 kW in power. A new ball-screw driven, high-speed cutter powered by either a high-power Nd:YAG or CO2 laser is about to be introduced. This unit features a gantry with 3D head.
Among the special laser systems built are a diamond saw blade welder, a fan belt pulley welder, laser engraver, seam tracker, and tri-metal welder.
In 1985 Do Youl Kim, then laser group head in the LG Institute at Lucky Goldstar Company (now LG), was called into his boss's office and told to start work to develop a slow axial flow CO2 laser. He produced a simple single-tube, resistor-strip, tube discharge device which eventually morphed into a two-tube unit rated at 200 watts. It was used for engraving applications for about 10 years.
Kim left LG in 1992 to start his own business, Hana Engineering Co. Ltd., in Anyang, which is located about an hour south of Seoul. Hana became a special welding system builder with a reputation for undertaking difficult processing assignments for Korean companies. In the Hana lobby is displayed the first laser Kim built for Lucky Goldstar, a piece of history he is justifiably proud to pose with.
Among Hana's primary markets is the auto industry, where it has installed numbers of Nd:YAG welders for joining fuel injector solenoid valves, ABS brake solenoid valves, and steering control valves. The company also has built welders to join nuclear fuel grids, roll-formed stainless steel pipe, diamond saw blades, home appliances, rechargeable battery cans, and fiber modules. Plus, it has built cigarette perforating machines, glass line fine cutting machines, and laser drilling machines.
I had an opportunity to visit Samhan Jungmil Co., Ltd., where Hana had just installed a rolled steel tubing welding machine. Samhan is a family-owned business in Namyangju-city, nestled in the mountains just below a ski lift. Y.K. Han started the business 35 years ago using a TIG welder to produce thin-wall stainless steel tubing. Samhan is one in a long line of companies that ILS admires; a traditional business not afraid to move with new technology. Until recently this father/son business was successfully meeting the needs of Korean industry. Then the younger Han happened to read about the use of a roll-form laser welder to join stainless steel tubing and he saw some samples which were vast improvements over the TIG welds they currently made. Together they saw laser welding as a way to perhaps sell tubing internationally.The Hans contacted Hana Engineering and eventually contracted with Hana and a tube mill company to produce a continuous roll-form tube welder, shown in the photo, capable of welding stainless steel tubing in a range of diameters from 0.3 to 3.9 inches. This feature is thought to be unique to the Hana system. The majority of the tubing being cut at Samhan is in the 1.0- to 1.5-inch range. Tube thicknesses are 0.027 inch to 0.118 inch with the heaviest demand being in the 0.047-inch thickness. To be practical the Hans requested that the system be capable of welding at speeds up to 14 meters per minute with no evidence of top or under bead. When we visited, 1.0-inch tubing was being run at 10 meters per minute with an amount of under bead that the senior Han suggested was satisfactory for general-purpose but not sterile (i.e., hypodermic needle) applications. However, the younger Han seemed pleased with the progress that had been made in just a few weeks of effort on the new system, and he expressed confidence that he could meet his father's quality and production rate requirements.
As I drove away from Samhan I couldn't help but reflect on a similar visit just three months earlier in Italy (see ILS, April 2004), where another father/son team, also in the shadow of a ski resort, was using laser technology to stay competitive in a global market.
The third in the triumvirate of leading laser system suppliers I met on the Korean trip is EO Technics, whose president, Kyu-Dong Sung, graciously shared with me his views of the Korean market for semiconductors and wafer processing led by Samsung. EO Technics (Anyang) is a pioneer in laser marking technology and laser-related processing equipment. The company was founded in April 1989 and incorporated as EO Technics, Co. Ltd. in December of 1993. In August of 2000, it registered as a public company on the KOSDAQ stock market. EO Technics has grown into a global company with branch offices in the Philippines, U.S., Malaysia, Singapore, Thailand, Taiwan, Indonesia, China, and Japan. Currently the company has about 300 employees worldwide generating annual sales of $32 million last year, and it expects to double that sales volume this year as it continuously delivers advanced-quality laser processing equipment for the semiconductor and other industries.During its early years the company focused on laser marking systems as its main product; however, since then the company has developed equipment such as a laser deflasher, laser wafer level marker, laser via-hole driller, laser trimmer, and laser ITO dry-etcher. Recently the company introduced a laser wafer-dicing system to meet the growing demand in chip scale packages, and this product shows a high-quality dicing with fast speed. This machine will provide for the next generation of wafer-dicing technology and will further improve yield and throughput for wafer-level packaging.
EO Technics has been transforming into a laser solutions provider for the semiconductor and display industry. The company will apply its laser processing knowledge to improve the yield and reliability of production in the high-tech industry. Further, it is building a strong partnership with many high-tech companies for future products.
At a farewell dinner with the three company presidents, each spoke with confidence on prospects for 2004 sales based on global revenues, as they see Korea playing an increasing role in Asia and beyond. I was struck by the positive attitude these industry leaders have in their ability to compete in Asia, where they already are having success in China because of their ability to deliver quality products, and in Taiwan where their products in the semiconductor and microelectronics sector are well established. After dinner we scratched out some numbers to compare laser revenues in China with those in Korea, confirming what my hosts had been saying all evening: Korea far surpasses China in industrial laser revenues.
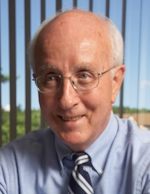
David Belforte | Contributing Editor
David Belforte (1932-2023) was an internationally recognized authority on industrial laser materials processing and had been actively involved in this technology for more than 50 years. His consulting business, Belforte Associates, served clients interested in advanced manufacturing applications. David held degrees in Chemistry and Production Technology from Northeastern University (Boston, MA). As a researcher, he conducted basic studies in material synthesis for high-temperature applications and held increasingly important positions with companies involved with high-technology materials processing. He co-founded a company that introduced several firsts in advanced welding technology and equipment. David's career in lasers started with the commercialization of the first industrial solid-state laser and a compact CO2 laser for sheet-metal cutting. For several years, he led the development of very high power CO2 lasers for welding and surface treating applications. In addition to consulting, David was the Founder and Editor-in-Chief of Industrial Laser Solutions magazine (1986-2022) and contributed to other laser publications, including Laser Focus World. He retired from Laser Focus World in late June 2022.