Precision drilling of alumina ceramic
There are a large number of lasers being used to drill and cut alumina ceramic for a variety of applications. The laser of choice for this application is CO2 as it is fairly cheap and easy to use and has a very high processing speed with respect to other sources. However, using the CO2 or any other ‘red’ laser has inherent drawbacks in minimum achievable hole size, feature quality and definition, and thermal overload. We describe below a comparison of methods used to laser drill alumina ceramics, taking note of laser drill time, hole quality, system cost, and user friendliness. We present detailed observations using the tripled DPSS laser.
Lasers
CO2 (10 microns). This laser is being used more than any other laser in drilling, cutting, scribing, and marking ceramics. Processing speeds using a fixed-beam, gas-assist setup can be very high, and the ease of use and cost are quite acceptable. The drawback is that this is a thermal laser and the material is ejected as a result of local heating, therefore microcracking is evident. Also, because of the long wavelength, the minimum achievable hole size is too large for many emerging applications. For instance, the hole size and pitch needed for probe applications (<100 microns D and <200 microns P), are probably not achievable using the CO2 laser—speed is fine, but quality is not acceptable.
Fundamental YAG (1064 nm). This laser wavelength does not couple well with the white alumina. We have tried several different lasers and setups and, while the drill speed can be fast, the holes show a lot of taper and the hole quality is much poorer than with a UV laser. This laser is not a good candidate for precision alumina processing.
Doubled YAG (532 nm). This is a decent wavelength with good coupling to the material. We investigated this wavelength using a 4ns pulse length laser. Due to the shorter wavelength and short pulse length, we observed much less thermal damage than using other longer wavelength lasers.
Tripled YAG (355 nm). This is the most convenient UV laser wavelength as it is available in up to 20W Q-switched commercial models, it gives very good hole quality with little thermal damage, and it is easy to use. Processing speed is much slower than when using ‘red’ lasers, but in the UV family it is the most economical of wavelengths. In general, materials over about 250-microns thick take a long time to process. We have made the same part with a 10W 355nm laser and a 500W CO2 laser and, while the 355nm laser gave far superior results, there was about a factor of 18 in speed difference (CO2 laser taking 1 hour and 355nm laser 18 hours).
Quadrupled YAG (266 nm). While this laser shows very good drill quality, it is not available commercially in anything more than a 3W version and, for the additional expense over a 355nm laser, it does not bring a lot better quality and the speed is lower. This laser is used only in applications that require the highest quality and in thinner materials with very dense patterns (see our article on 266nm DPSS lasers in the Dec. 2006 issue of ILS, p. 18, Figure 5).
The 248nm excimer laser is a high-pulse-energy, low-repetition-rate laser that is used in the mask imaging mode. The best feature resolution can be gotten on target and, with the right optics, very little taper can be realized. We have drilled nominal 4mil (100-micron) diameter holes in 1mm thick alumina with the entrance being about 4.2 mils and the exit being about 3.8 mils. The excimer’s main drawbacks are the speed of processing (about a minute per hole as described above) and the hassle factor.
Optics/beam delivery
Galvos- Galvanometers are the fastest way of steering the beam and are used with lasers that have a Gaussian beam profile. The hole-to-hole move time is minimized using galvos. Galvo-based beam deliveries will produce a taper, with the entrance hole being larger than the exit hole by some amount—typically 7 to 10 degrees. For the 355nm laser the beam size on target is about 25 microns or less, and for example the 532nm laser is about 1.5x greater because of the longer wavelength, or about 37 microns. Galvo positioning is limited to an accuracy of about +/-10 microns (depending on field size—larger fields have larger inaccuracies) when using the whole field and drilling many holes within a given field. Better positional tolerances can be gotten by stepping from hole to hole using the table, then using the galvo to simply drill each hole, but at sacrifice in overall speed. The positional tolerance using the above method will depend on the table accuracy and the encoders, but with 0.1-micron encoders the accuracy will be on the order of microns.
Fixed beam. This method uses a fixed beam, usually with a coaxial gas assist, and the hole is drilled by using table motion. It is used primarily with CO2 lasers and is the most common method in use.
Boring or trepanning head. This method consists of an optical device with rotating pairs of wedged prisms that can be adjusted. The first set of prisms can be adjusted to get the desired hole size—any diameter larger than the minimum D of the beam on target. The second set of prisms controls the taper. One appealing aspect of this design is that it can be used to control a taper, and under the right conditions, one can get positive taper (entrance bigger than exit), negative taper, and also no taper or ‘hourglass’ effects. This boring head is also used in conjunction with a high-pressure gas assist. The placement accuracy is defined by the table motion, so the accuracy can be quite good. The drill speed can be very high with the right laser, but hole-to-hole moves are slower than with the galvos. This technique has many advantages, but some disadvantages are complexity, ease of use (galvos are much easier), and cost. However, if holes are required that are ‘taper free’ or anything other than positive taper, this technique can be used.
Experimental
We limit the scope of the following discussion to the 355nm laser with galvos as this laser is a good compromise for quality vs. speed. Experiments are ongoing using other lasers and also looking at other ceramics and ‘ceramic like’ material.
The laser used was a Coherent Avia. We used 1.5W, 3.0W, and 10W lasers in our experiments, but we have found that in most cases the full power of the laser can be used to increase speed (unless the holes are very closely spaced) so we present results for the 10W laser. The pulse length is about 30 ns. We drilled approximately 200-micron D holes in 400-micron thick alumina. First we optimized for a set of running conditions and then drilled a series of holes and compared them hole to hole under the same operating conditions. The running conditions used the full power of the 10W laser and each hole took about 6 seconds to drill. Note that we can drill these holes in 4 seconds, but when drilling thousands of holes, sometimes a few do not drill through, so we increase drill time to make sure all holes are through. We can drill holes in 2 seconds in 200-micron thick alumina, but we have a difficult time drilling in material more than 500 microns thick as the time to drill increases rapidly and we cannot get through anything over 1 mm at the most. Also, the taper increases. If thicker material is needed, it is much more economical to drill several thinner pieces and laminate. It is also beneficial to drill serially from both sides if alignment accuracy is good. A typical Class I system cost is about $300,000. Figures 1 and 2 show entrance and exit holes in 400-micron thick ceramic with the entrances varying from 205 microns to 214 microns and exits varying from 162 microns to 169 microns.
Results and recommendations
The 355nm laser is easy to use and gives excellent processing results using the galvo or fixed-beam configuration. The boring head configuration requires much more attention. Figure 3 shows a very dense array of 100-micron holes with only about 20-microns rib in between. This was done with a 10W 355nm laser. Figures 4 and 5 are close ups of the entrance and exit holes. We had to slow down the laser to produce this array without cracking. Therefore, in general, the 355nm laser is more subtle and versatile than longer wavelength sources for high-precision applications.
The frequency tripled DPSS lasers have low cost of operation, give acceptable processing speeds on thin materials and have very high up-time and reliability. For alumina material less than 250 microns thick, high hole densities can be achieved with little observable HAZ. Faster processing speeds can be achieved with other laser sources, at some cost in hole quality and HAZ. Further investigations on other materials and using new laser sources are ongoing.
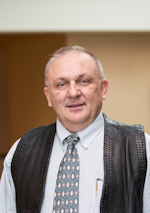
Ron Schaeffer
Ron Schaeffer, Ph.D., is a blogger and contributing editor, and a member of the Laser Focus World Editorial Advisory Board. He is an industry expert in the field of laser micromachining and was formerly Chief Executive Officer of PhotoMachining, Inc. He has been involved in laser manufacturing and materials processing for over 25 years, working in and starting small companies. He is an advisor and past member of the Board of Directors of the Laser Institute of America. He has a Ph.D. in Physical Chemistry from Lehigh University and did graduate work at the University of Paris. His book, Fundamentals of Laser Micromachining, is available from CRC Press.
Gabor Kardos
Gabor Kardos is contract manufacturing manager at PhotoMachining (Pelham, NH).
Oleg Derkach
Oleg Derkach is applications specialist at PhotoMachining (Pelham, NH).